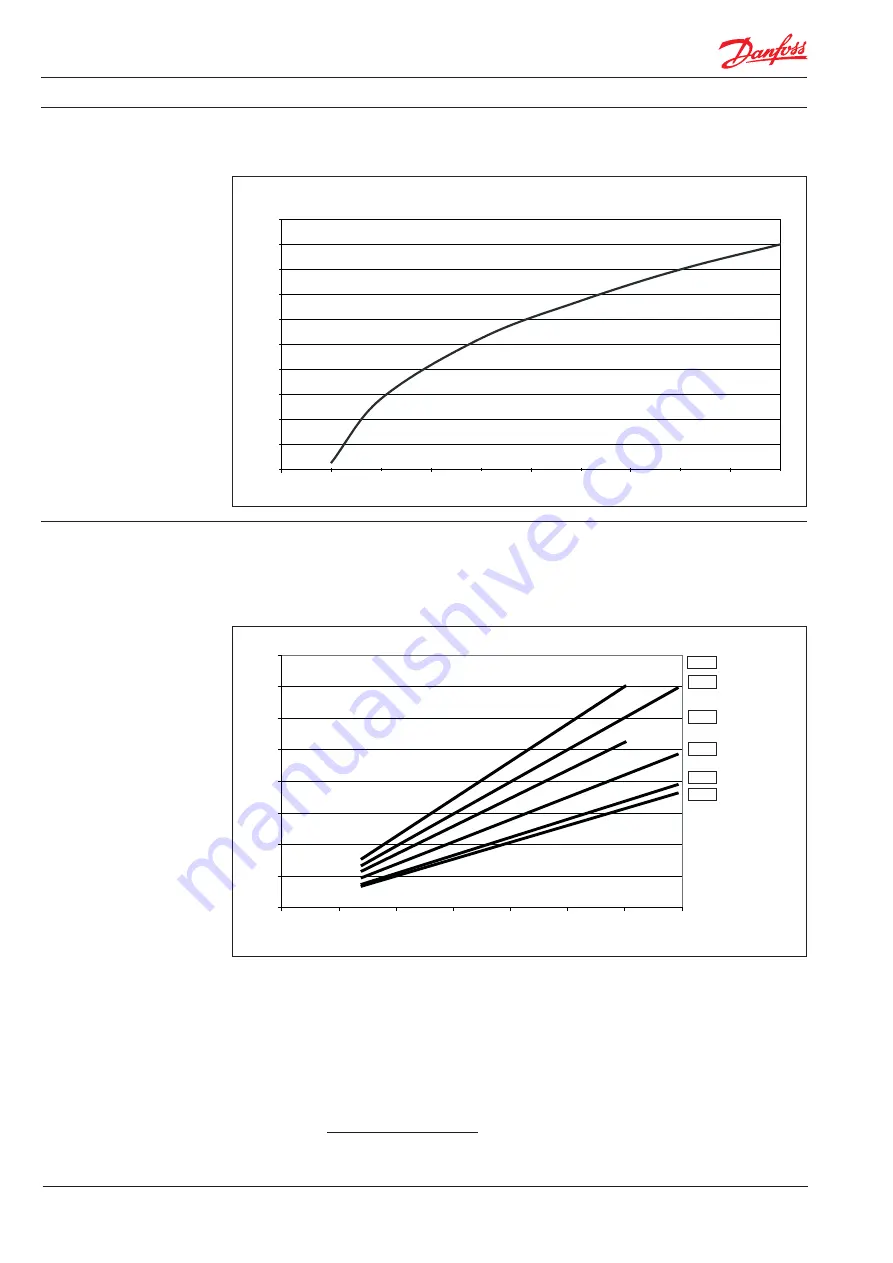
6
180R9267 / IOM APP 1.5-3.5 Appendices - v04 / 11.2013
Data sheet
APP pumps - APP 1.5-3.5
4
521B0850 / DKCFN.PD.013.FA6.02 / 09.2012
The diagram shows pressure differences across
the flushing valve:
4.
Flushing valve
5.
Flow at different rpm
Using the diagram shown below, it is easy to
select the pump which fits the application best if
the flow required and the rotation speed (rpm) of
the pump are known.
Furthermore, this diagram shows that the flow
can be controlled by changing the rotation
speed of the pump. The flow/rpm ratio is
constant, and the “required“ flow can be
obtained by changing the rotation speed to a
corresponding value. Thus, the required rpm can
be determined as:
Required flow × Rated rpm
Required rpm =
Rated flow
521B0850
DKCFN.PD.013.FA6.02
3
5.
Flow at diff erent rpm
Using the diagram shown below, it is easy to select the pump which fi ts the application best if the fl ow required and the rotation
speed (rpm) of the pump are known.
Furthermore, this diagram shows that the fl ow can be changed by changing the rotation speed of the pump. The fl ow/rpm ratio is
constant, and the “required “ fl ow can be obtained by changing the rotation speed to a corresponding value. Thus, the required rpm
can be determined as:
Required fl ow × Rated rpm
Required rpm =
Rated fl ow
6.
Power requirements
Pump model
Flow
Pressure
rpm
Calc. factor
60 bar
70 bar
80 bar
l/min
m
3
/h
gpm
870 psi
1015 psi
1160 psi
APP1.5
25.11
1.51
6.63
3.21 kW
3.75 kW
4.29 kW
2890
468.6
APP1.5
30.17
1.81
7.97
3.86 kW
4.51 kW
5.15 kW
3470
468.6
APP1.8
26.78
1.61
7.07
3.43 kW
4.00 kW
4.57 kW
2890
463.2
APP1.8
32.18
1.93
8.50
4.12 kW
4.81 kW
5.49 kW
3470
463.2
APP2.2
33.48
2.01
8.84
4.29 kW
5.00 kW
5.71 kW
2900
468.6
APP2.2
40.22
2.41
10.63
5.15 kW
6.01 kW
6.87 kW
3480
468.6
APP2.5
41.94
2.52
11.08
5.07 kW
5.92 kW
6.77 kW
2900
484.8
APP3.0
48.2
2.9
12.7
6.2 kW
7.2 kW
8.2 kW
2930
470.0
APP3.5
56.0
3.4
14.8
7.2 kW
8.4 kW
9.6 kW
2930
470.0
The power requirements can be determined using one of the following guiding equations:
l/min × bar
16.7 × m
3
/h × bar
0.26 × gpm × psi
Required power =
[
kW
] or
[
kW
] or
[
kW
]
Calc. factor
Calc. factor
Calc. factor
1 hp = 0.75 kW
1 kW = 1.34 hp
1 gpm = 3.79 l/min
1 l/min = 0.26 gpm
1 m
3
/h = 4.40 gpm
1 gpm = 0.23 m
3
/h
0
0,5
1
1,5
2
2,5
3
3,5
4
0
500
1000
1500
2000
2500
3000
3500
rpm
m³
/h
APP1.8
APP2.2
APP1.5
APP2.5
APP3.0
APP3.5
2
DKCFN.PD.013.FA6.02
521B0850
3.
Technical data
APP pumps
APP1.5
APP1.8
APP2.2
APP2.5
APP3.0
APP3.5
Code number
180B3043 180B3044 180B3045 180B3046 180B3030 180B3032
Geometric displacement
cm
3
/rpm
(in
3
/
rpm)
9.3
(0.56)
10
(0.61)
12.5
(0.76)
15.3
(0.93)
17.7
(1.08)
20.5
(1.25)
Rated fl ow (3000 rpm)
1)
m
3
/h
(gpm)
1.5
(6.6)
1.7
(7.5)
2.1
(9.2)
2.6
(11.4)
3.0
(13.2)
3.5
(15.4)
Outlet min. pressure
2)
bar
(psi)
20
(290)
20
(290)
20
(290)
20
(290)
20
(290)
20
(290)
Outlet max. pressure,
continuous
3)
bar
(psi)
80
(1160)
80
(1160)
80
(1160)
80
(1160)
80
(1160)
80
(1160)
Outlet max. pressure,
intermittent
4)
bar
(psi)
100
(1450)
100
(1450)
100
(1450)
100
(1450)
100
(1450)
100
(1450)
Inlet min. pressure
bar
(psi)
0.5
(7.3)
0.5
(7.3)
0.5
5)
(7.3)
0.5
(7.3)
0.5
5)
(7.3)
0.5
(7.3)
Inlet max. pressure,
continuous
bar
(psi)
5
(72.5)
5
(72.5)
5
(72.5)
5
(72.5)
5
(72.5)
5
(72.5)
Inlet max. pressure, peak
bar
(psi)
10
(145)
10
(145)
10
(145)
10
(145)
10
(145)
10
(145)
Max. speed continuous
rpm
3450
3450
3450
5)
3000
3450
5)
3000
Min. speed continuous
rpm
700
700
700
700
700
700
Power requirement
at 80 bar and 3000 rpm
kW
(hp)
4.5
(6)
4.8
(6.3)
6.0
(7.9)
7.2
(9.6)
8.4
(11.3)
9.8
(13.1)
Torque at 80 bar
Nm
(lbf-ft)
14,2
(10.5)
15.3
(11.3)
19
(14)
23
(17)
25.6
(18.8)
29.7
(21.9)
Weight
Kg
(lb)
8.6
(17)
8.6
(17)
8.6
(17)
8.6
(17)
8.6
(17)
8.6
(17)
Integrated fl ushing valve
YES
YES
YES
YES
YES
YES
1) Typical average fl ow at 80 bar (1160 psi).
4) Intermittent pressure is acceptable for less than
2) For lower pressure, please contact Danfoss RO Sales Organization.
10 seconds per minute.
3) For higher pressure, please contact Danfoss RO Sales Organzation.
5) For speeds above 3000 rpm the pump must be
boosted at a pressure of 2-5 bar (29.0 - 72.5 psi).
4. Flushing valve
The diagram shows pressure diff erence across fl ushing valve
APP1.5-3.5 flushing valve characteristic
0
2
4
6
8
10
12
14
16
18
20
0
1
2
3
4
5
Pressure [bar]
Flow[l/min]
APP 1.5-3.5 flushing valve characteristic
Pressure [bar]
Fl
ow
[l
/m
in
)
20
18
16
14
12
10
8
8
4
2
0
1
22
3
4
5