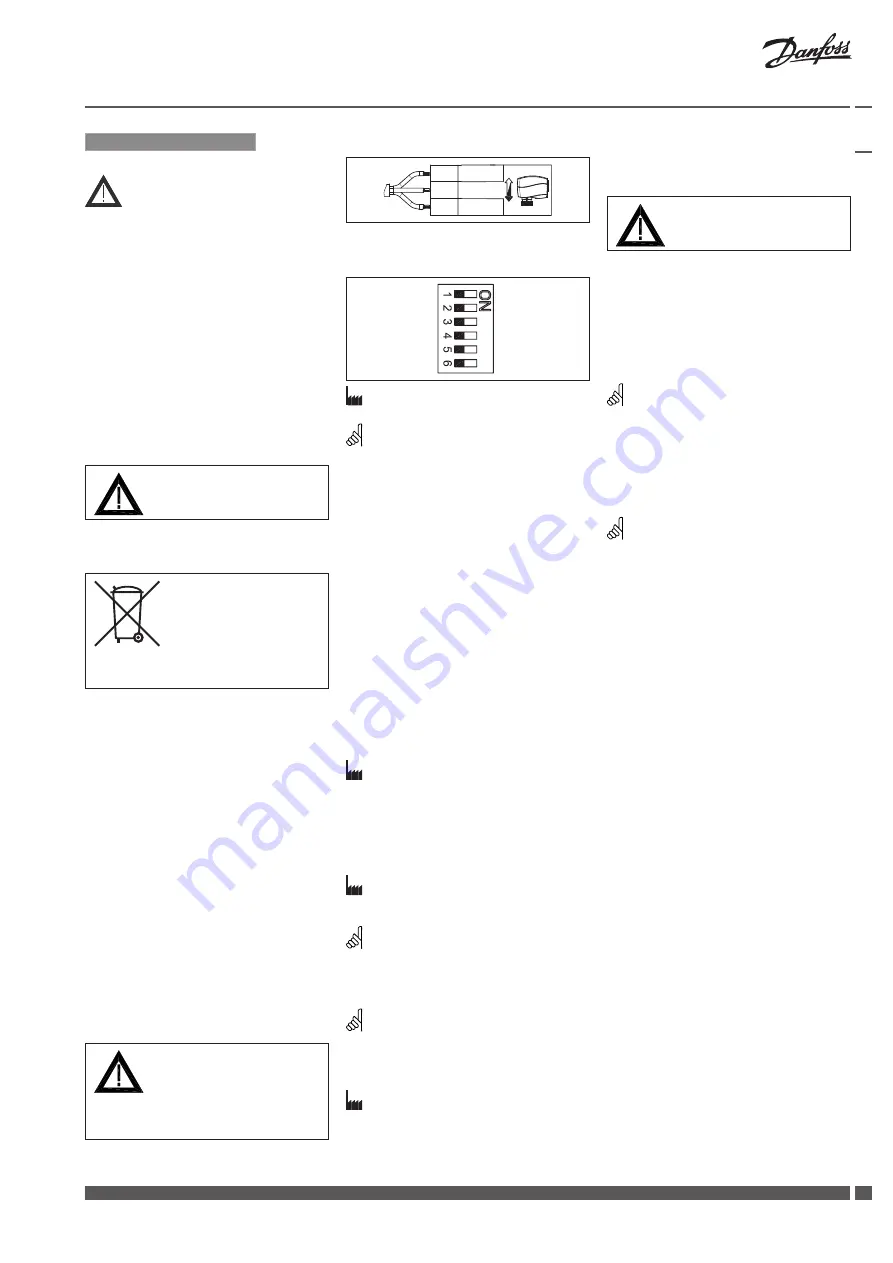
55
Installation Guide
AME 130(H), AME 140(H)
Danfoss Heating
VI.KU.M4.90
DH-SMT/SI
ENGLISH
Safety Note
To avoid injury and damage to persons and
devices, it is absolutely necessary these
instructions are carefully read and observed
prior to assembly and commissioning.
Necessary assembly, start-up, and
maintenance work must be performed
only by qualified, trained and authorised
personnel.
Prior to assembly and maintenance work on
the controller, the system must be:
- depressurised
- cooled down
- emptied and
- cleaned
Please comply with the instructions of the
system manufacturer or system operator.
Do not remove the cover before
the power supply is fully
switched off.
Disposal instruction
This product should be
dismantled and its
components sorted, if
possible, in various groups
before recycling or disposal.
Always follow the local disposal
regulations.
Mounting
➊
The actuator should be mounted with the
valve stem in either horizontal position or
pointing upwards.
The actuator is fixed to the valve body by
means of a ribbed nut which requires no
tools for mounting. The ribbed nut should be
tightened by hand.
Installation
❷
1. Check the valve neck. The actuator should
be in steam up position (factory setting).
Ensure that the actuator is mounted
securely on the valve body
2. Wire the actuator according to the wiring
diagram
3 The direction of stem movement can be
observed on the position indicator
①
Wiring
❸
Do not touch anything on the
PCB! Switch off the power line
before wiring the actuator!
Lethal voltage!
Wire the actuator according to the
wiring diagram.
Red
Gray
Black
24 VAC
Y 0 - 10 VDC
Common
DIP switch settings
Reset
Reset
0V…---V
Inverse
Sequential
5(6)…10 V
I
Reset
2V…---V
Direct
- - -
0(2)…5(6) V
U
Reset
2 V...---V
0V...---V
Direct
Inverse
---
Sequential
0(2)...5(6)V
5(6)...10V
U
I
Factory settings:
ALL switches are on OFF position!
NOTE:
All combinations of DIP switches are allowed.
All functions that are selected are added
consecutively.
SW1: Reset
❹
After the actuator has been connected to
power supply, the actuator will start the self-
adjustment procedure. The indicator LED
①
flashes until self adjustment is finished. The
duration depends on the spindle travel and
will normally last a few minutes. The stroke
length of the valve is stored in the memory
after self adjustment has been completed. To
restart self adjustment, change the position
of the RESET switch (switch No.1). If the
supply voltage is switched off or falls below
80 % in more than 0.1 s, the current valve
position will be stored in the memory and all
data remain saved in the memory also after a
power supply cut-out.
SW2: 2-10 V/0-10 V
❺
Factory setting is:
2-10 V.
SW3: Direct/Inverse
❻
The actuator can be set for the spindle to
travel downwards on the rising control signal
(DIRECT), OR for the spindle to travel upwards
on the rising control signal (INVERSE)
Factory setting is:
DIRECT
SW4: ---/Sequential
❼
NOTE:
This combination works in combination with
switch No.5: 0(2)-5(6) V/5(6)-10 V.
SW5: 0(2)-5(6) V/5(6)-10 V
❽
NOTE:
This function is available if switch No.4: ---/
Sequential is set.
SW6: U/I
❾
Factory setting:
voltage control signal (2-10 V).
Manual override
(for service purposes only)
Do not manually operate the
drive under power!
AME 130, AME 140
❿
①
Remove the cover
②
Insert the Allen key 6 into the spindle
③
Press and hold the button (on the bottom
side of the actuator) during manual
override
④
Pull out the tool
⑤
Replace cover
Remark:
A ‘click’ sound after energising the actuator
means that the gear wheel has jumped into
normal position.
AME 130H, AME 140H
⓫
Press and hold the button
①
(on the bottom
side of the actuator) during manual override.
Remark:
A ‘click’ sound after energising the actuator
means that the gear wheel has jumped into
normal position.
Function test
The light emitting diode (LED)
❹①
indicates
whether the actuator is in operation or not,
the operating status, and failures, if any.
• No light
- no operation or no power supply
• Constant light
- normal operation
• Flashing light (1 Hz)
- self-adjusting mode
• Flashing light (~ 3 Hz):
- power supply too low
- initial self-adjusting time to short
due too short valve’s stroke must
last more than 12 sec.