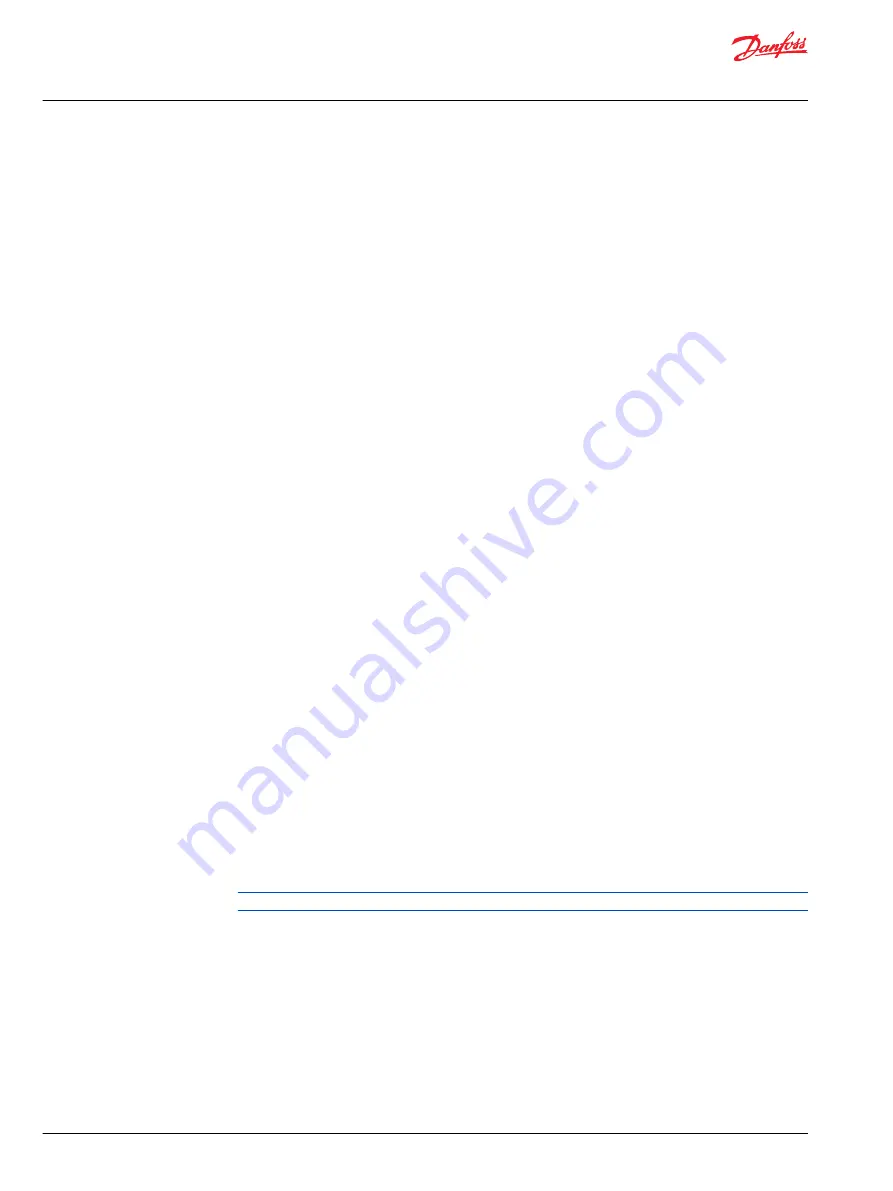
Reassembly
1. Install the servo control orifice (G020), and torque to 2.7 N•m [24 in•lb]. Then install the orifice backup
plug (G030), and torque to 2.7 N•m [24 in•lb].
2. Install the PC spool (C132), spherical end first, into the PC bore. Install plug (C103). Torque the plug to
12 N•m [8.9 lbf•ft].
3. Place the two PC springs (C134, C135) onto the spring guide (C133) and install into the PC bore. Place
a new O-ring (C138A) onto the PC adjusting screw (C138) and thread it into the PC bore until flush,
then make another full turn. Install and torque the PC set screw (C102) to 9.6 N•m [7.1 lbf•ft].
4. Install the LS spool (C112), spherical end first, into the LS bore.
5. Install plug (C104). Torque the plug to 12 N•m [8.9 lbf•ft].
6. Place the two LS springs (C114, C115) onto the spring guide (C113) and install into the LS bore.
Thread adjusting screw (C118) into the LS bore until flush, then make another full turn. Install and
torque the LS set screw (C102) to 9.6 N•m [7.1 lbf•ft].
7. Install the electric control manifold drain orifice (C149) and torque to 2.7 N•m [24 in•lb].
8. Install the cartridge valve (C150) into the electric control manifold (C152). Torque to 27.7 N•m [20.4
lbf•ft]. DO NOT OVERTORQUE the cartridge valve.
9. Install the electric solenoid (C155), and solenoid coil nut (C125). Torque to 8.7 N•m [6.4 lbf•ft].
10. Install plug (C153). Torque the plug to 12 N•m [8.9 lbf•ft].
11. Using petroleum jelly to retain them, install the two interface O-rings (C154) in the recesses on the
electric control manifold.
12. Install the manifold assembly onto the control housing using four screws (C151). Torque the screws to
6.4 N•m [4.7 lbf•ft]. Torque the screws in a criss-cross pattern and re-torque the first screw to ensure
proper torque retention.
13. Using petroleum jelly to retain them, install the four interface O-rings (C200) in the recesses on the
control housing.
14. Install the control assembly onto the endcap using the four screws (C300). Torque the screws to 6.4
N•m [4.7 lbf•ft]. Torque screws in a criss-cross pattern and re-torque the first screw to ensure proper
torque retention.
15. Check and adjust the control setting. See
Adjustments
section.
Fan Drive Control
Disassembly
Use the wrench sizes and torques listed in the table.
1. Remove four screws (C300).
2. Remove the control and discard the 4 interface O-rings (C200).
3. Remove the coil plastic nut (QC125 ) Remove the coil.
Remember the correct coil connector orientation.
4. Remove the solenoid cartridge (C120). Remove O-ring (QC120).
5. Remove spring (C124) and spring guide (C123).
6. Remove the pressure limiter adjuster (C128).
7. Remove spring (C125) and spool (C122).
8. Remove plug (C107) and plug (C129).
9. Remove gain orifice (H030).
Service Manual
Series 45 Frame K2 Open Circuit Axial Piston Pumps
Minor repair
34 |
©
Danfoss | April 2017
AX00000301en-US0101