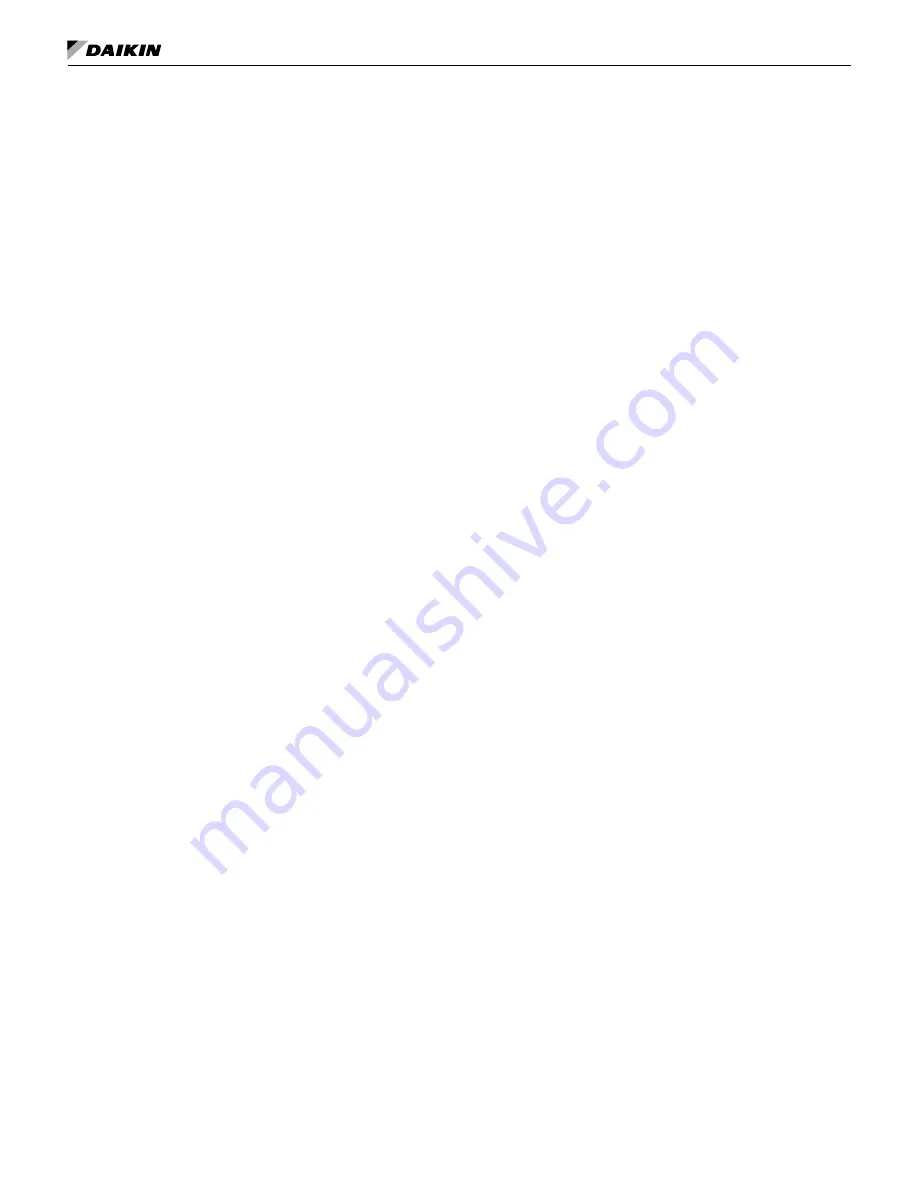
Unit Operation Check List
Connect supply power to the unit and confirm green
LED illuminates on the Mark IV control board.
Adjust all valves to their full open positions. Turn on
the line power to all heat pumps.
Note:
Room temperature should be within the mini
-
mum-maximum ranges. During start-up checks,
loop water temperature entering the heat pump
should be between 55°F [13°C] and 90°F [32°C].
If either return air temperature or water tem
-
perature are at a minimum or maximum level,
the other must be at normal condition for proper
operation of the heat pump.
Adjust the unit thermostat to the fan only position
and check for fan operation.
With the thermostat in “Auto” adjust to minimum
setpoint. Compressor start-up could take up to 6
minutes depending on thermostat configuration.
Verify compressor operates and cool air is delivered.
Complete start-up sheet beginning
on page 32
of this manual. Confirm unit capacity is within 10%
of the catalog THR. It is not necessary to connect
refrigeration gauges unless unit troubleshooting is
required and all external air and water conditions
are verified to be adequate.
Verify the condensate trap fills to provide a air seal
with the drain system.
Adjust thermostat to warmest setting and confirm
compressor operation. Confirm warm air is delivered
after a few minutes of operation.
Check for vibration, noise and water leaks. Inspect
piping and wiring for rubbing. Make adjustments
as needed for rubbing lines or wiring. It is the
responsibility of the installer to make final unit
adjustments.
If unit does not operate properly perform
troubleshooting as needed.
Troubleshooting
Should a major problem develop, refer to the following
information for possible cause and corrective steps.
Neither fan nor compressor runs:
1.
The fuse may be blown or the circuit breaker is
open. Check electrical circuits and motor windings
for shorts or grounds. Investigate for possible
overloading. Replace fuse or reset circuit breakers
after fault is corrected.
2.
Wires may be loose or broken. Replace or tighten.
3.
Supply voltage may be too low. Check it with the
power company.
4.
Control system may be faulty. Check thermostat
for correct wiring and check 24 volt transformer for
burnout.
Fan operates but compressor does not:
1.
Check capacitor.
2.
Wires may be loose or broken. Replace or tighten.
3.
The high pressure may have tripped due to:
a. Fouled or plugged condenser.
b. Lack of or no condenser water.
c. Too warm condenser water.
d. Not enough airflow over the coil due to dirty
filters.
e. Coil or fan motor failure.
4.
The low temperature switch may have tripped due to:
a. Fouled or plugged condenser.
b. Lack of or no condenser water.
c. Too cold condenser water.
d. Not enough airflow over the coil due to dirty
filters.
e. Coil or fan motor failure.
5.
Check thermostat setting, calibration and wiring.
6.
The compressor overload protection is open. If the
compressor dome is extremely hot, the overload
will not reset until cooled down. If the overload
is external, replace it. If the overload is internal,
replace the compressor.
7.
The internal winding of the compressor motor may
be grounded to the compressor shell. If so, replace
the compressor.
8.
The compressor winding may be open. Check
continuity with ohmmeter. If the winding is open,
replace the compressor.
www.DaikinApplied.com 23
IM 447-11