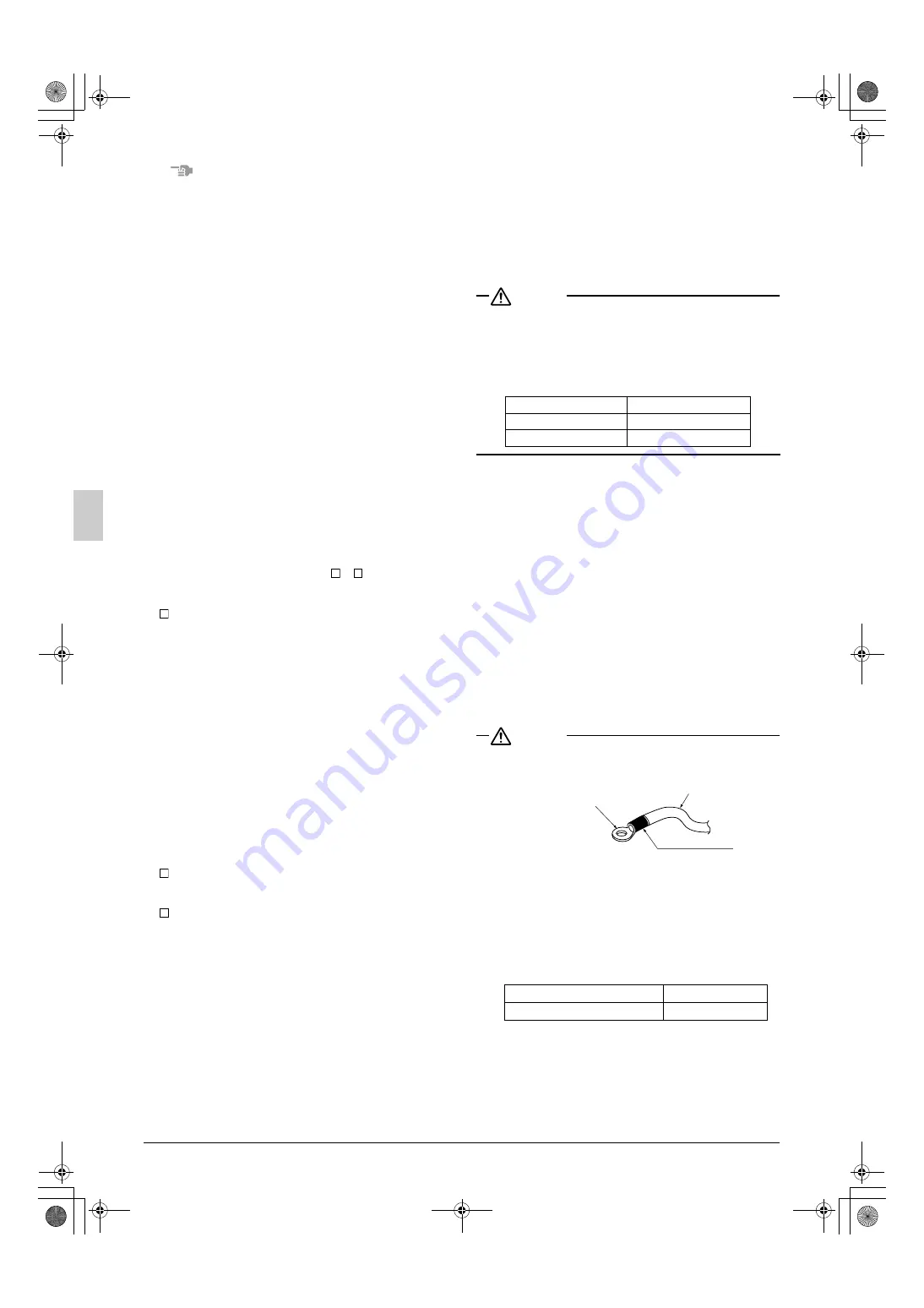
11
English
Note
•
Open the knock holes with a hammer or the like.
•
After knocking out the holes, we recommend you remove any
burrs and paint them using the repair paint to prevent rusting.
•
When passing wiring through the knock holes, remove burrs
around the knock holes and protect the wiring with protective
tape.
(Refer to figure 20)
•
If small animals might enter the unit, block off any gaps (hatching
parts in figure 20) with material (field supply).
7-4 Transmission Wiring Connection Procedure
•
Referring to figure 21, 22 connect the transmission wiring
between outdoor unit and indoor unit, outdoor unit and outdoor
unit of other system, outdoor unit and outdoor unit of same sys-
tem (only multi system) or to COOL/HEAT selector.
(Refer to figure 21)
1.
Connection example for single system
2.
Outdoor unit
3.
COOL/HEAT selector
4.
To outdoor unit of other system
5.
Match up terminal symbols. (Has polarity)
6.
Use duplex wires
7.
Indoor unit
8.
Never connect the power wire
(Refer to figure 22)
1.
Connection example for multi system
2.
Outdoor unit A (Master unit)
3.
Outdoor unit B (Sub unit)
4.
COOL/HEAT selector
5.
To indoor unit
6.
To outdoor unit of other system
•
All transmission wiring is to be procured on site. All wiring should
use sheathed vinyl cord 0.75-1.25 mm
2
or cable (duplex). (Triplex
only for the COOL/HEAT selector.)
•
Transmission wiring (About the symbol
~
, see figure 21, 22)
should be done within the following limitations.
If they are exceeded, transmission problems may occur.
Between outdoor unit and indoor unit
Between outdoor unit and outdoor unit of other systems
Max. wiring length
: 1,000 m
Max. total wiring length
: 2,000 m
Max. no. of branches
: 16
[Note]
No branch is allowed
after branch
(See figure 23)
Max. no. of outdoor units of other system
that can be connected
: 10
(Refer to figure 23)
1.
Outdoor unit
2.
Indoor unit
3.
Branch line 1
4.
Branch line 2
5.
No branch is allowed after branch
6.
Main line
7.
Central remote controller, etc.
8.
Branch line 3
9.
Transmission wiring between outdoor unit and indoor unit
10.
Transmission wiring between outdoor unit and outdoor unit
Between outdoor unit and outdoor unit of same system
(Only for multi system)
Max. wiring length
: 30 m
Transmission wiring to COOL/HEAT selector
Max. wiring length
: 500 m
•
The transmission wiring inside the EL.COMPO.BOX should be
secured using the clamp (1) as shown in figure 24.
(Refer to figure 24)
1.
In the EL.COMPO.BOX
2.
Retain to the EL.COMPO.BOX with the accessory clamp
(1).
•
Outside the units, the transmission wiring must be finished simul-
taneously with the local refrigerant piping, and wound with tape
(field supply) as shown in figure 25.
(Refer to figure 25)
1.
Liquid pipe
2.
Gas pipe
3.
Transmission wiring
4.
Insulation material
5.
Finishing tape
•
For multi system:
1. Transmission wiring between outdoor units in the same piping
system must be connected to terminals Q1 and Q2 (TO MULTI
UNIT).
Connecting the wires to the F1, F2 (TO OUT/D UNIT) termi-
nals results in system malfunction.
2. Wiring to other systems should be connected to terminals F1
and F2 (TO OUT/D UNIT) on the PC-board of the master unit.
The outdoor unit that connected transmission wiring to indoor
unit is the master unit. The others are sub unit.
CAUTION
• Do not connect the power wiring to terminals for the transmission
wiring. Doing so would destroy the entire system.
•
When connecting wires to the terminal block on the PC-board, too
much heat or tightening could damage the PC-board. Attach with
care.
See the table below for the tightening torque of the transmission
wiring terminals.
7-5 Power Wiring Connection Procedure
Be sure to connect the power supply wiring to the power supply ter-
minal block and hold it in place using the included clamp as shown in
the figure 26.
(Refer to figure 26)
1.
Power supply (3N~50Hz 380-415V)
2.
Earth leakage circuit breaker
3.
Branch switch, Overcurrent breaker
4.
Ground wire
5.
Attach insulation sleeves
6.
Power supply terminal block
7.
Ground terminal
8.
Clamp (1) (accessory)
•
The L1, L2, L3 and N phases of the power wiring should be
secured separately to the hook using the included clamp (1).
•
The ground wiring should be bound to the power wiring using the
included clamp (1) to prevent outside force from being applied to
the terminal area.
•
Wire so that the ground wiring does not come into contact with the
compressor lead wiring. If they touch, this may have an adverse
effect on other devices.
CAUTION
• Be sure to use crimp-style terminal with insulating sleeves for
connections. (See the figure below.)
•
For wiring, use the designated power wire and connect firmly,
then secure to prevent outside pressure being exerted on the ter-
minal board.
•
Use an appropriate screwdriver for tightening the terminal screws.
A screwdriver with a small head will strip the head and make
proper tightening impossible.
•
Over-tightening the terminal screws may break them.
See the following table for the tightening torque of the terminal
screws.
1
3
1
2
2
3
3
Screw size
Tightening torque (N·m)
M3 ABC I/P
0.53 - 0.63
M3.5 (A1P)
0.80 - 0.96
Screw size
Tightening torque (N·m)
M8 Power terminal, ground terminal
5.5 ~7.3
Power wire
Crimp-style terminal
Insulating sleeve
01_EN_3P226891-13Q.fm Page 11 Thursday, December 2, 2010 10:15 AM