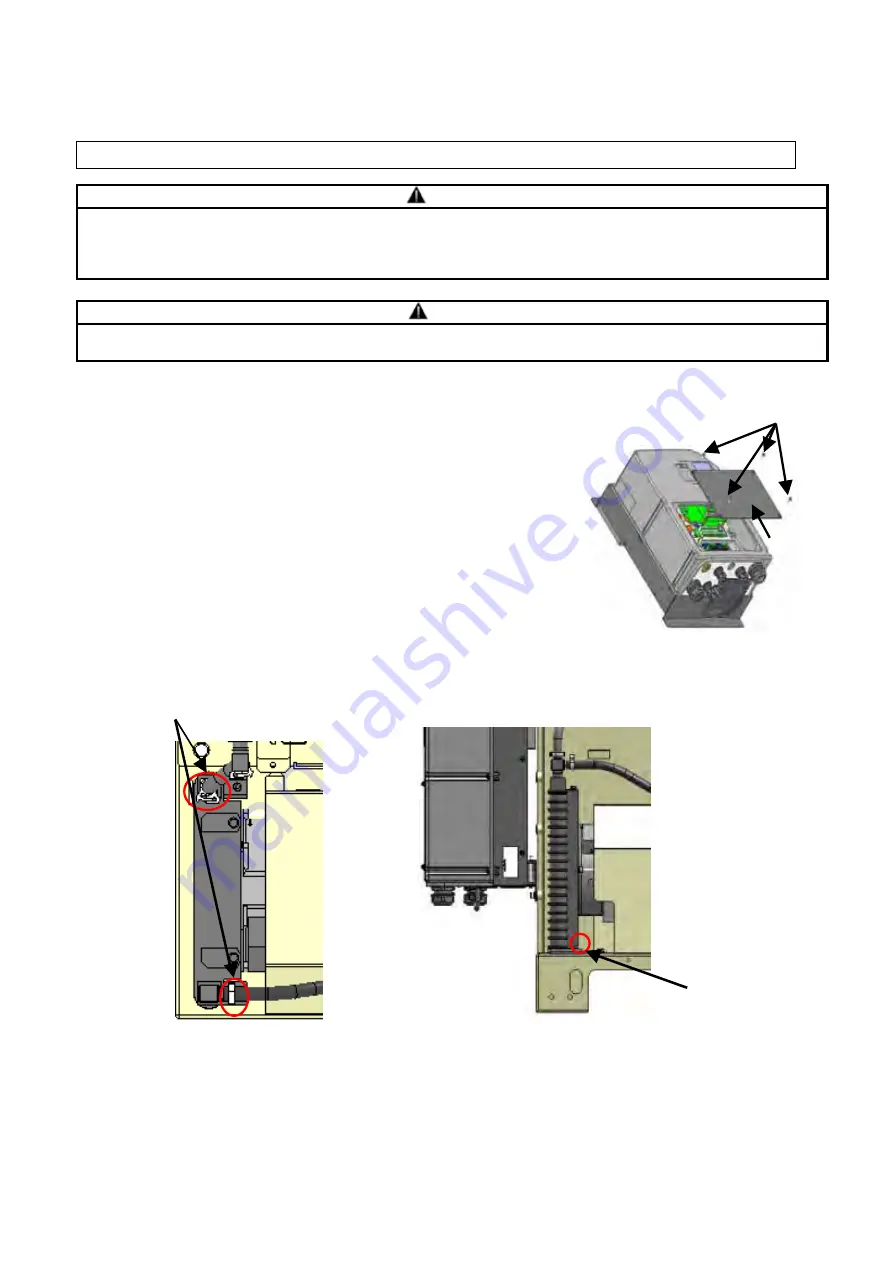
PIM00424
13-8
13.4
Oil cooler maintenance procedure (only for unit type SUT10, SUT16)
WARNING
Please stop operation and turn off the main power before maintenance.
Please wear gloves and protective glasses.
i ) Please pay attention to the fin portion of the core because it is sharp.
ii ) Please note that the foreign matters may enter your eyes at the time of air blow.
CAUTION
Please do not apply strong force to the connector and the power supply line of the AC fan while working.
Please note that the oil will flow out from the pipe or oil cooler during decomposition.
13.4.1
Removing the oil cooler
①
Loosen the cross-recessed truss head machine screws (M4×4, Fastening
torque: 1.0N · m) of the full cover, and remove the full cover.Then
disconnect the connector of the fan, the fan earth cable.
②
Remove the insulation lock which ties the fan harness.
③
Remove the hose bands (at two places), and disconnect the hoses (two
pieces) at the top of the oil cooler. At this time, oil may leak due to
backward oil flow from the tank. Before conducting this step, attach a blind
plug to each hose.
④
Remove the hexagon socket head bolts (M5×16: 2 pieces) with washers, and
dismount the oil cooler.
《Unit top view》
《Unit front view》
Hexagon socket head bolts
(M5×16:2piese)
Hose bands(at 2 places)
Controller cover mounting
screw
Controller small
cover
Summary of Contents for Super Unit SUT00S8007-30
Page 2: ......
Page 12: ......
Page 19: ...PIM00424 3 5 3 4 Dimensions Motor Pump Type SUT00 SUT00S8007 30 ...
Page 20: ...PIM00424 3 6 SUT00D8021 30 ...
Page 21: ...PIM00424 3 7 Unit Type SUT10 SUT16 SUT10S8007 30 ...
Page 22: ...PIM00424 3 8 SUT10D8021 30 ...
Page 23: ...PIM00424 3 9 SUT16D8021 30 ...
Page 28: ......
Page 32: ......
Page 34: ......
Page 38: ......
Page 42: ......
Page 50: ......
Page 60: ......
Page 92: ......