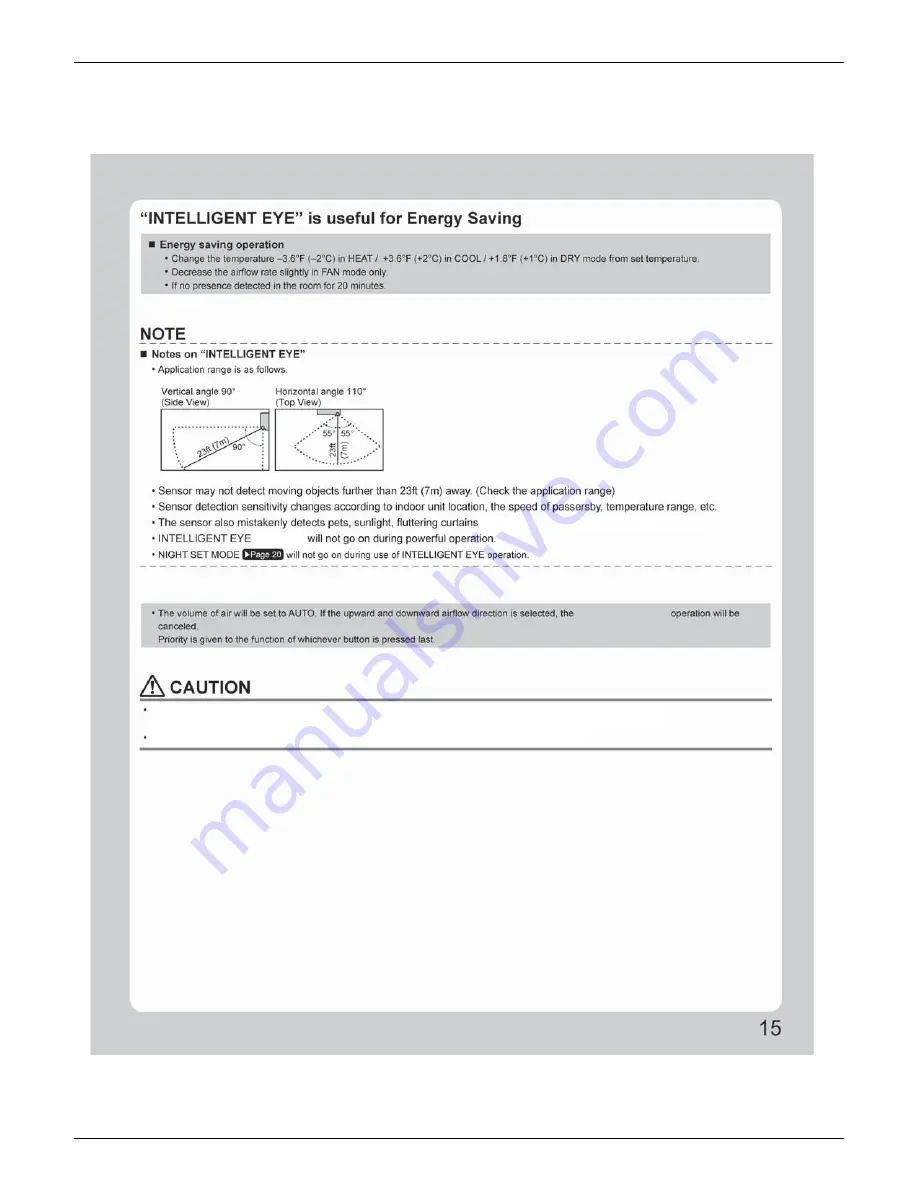
Duct-Free System
SiUS12-928_A
71
Operation Manual
operation
and light reflected off the mirrors on passing vehicles.
COMFORT AIRFLO
W
Do not hit or forci
b
ly p
u
sh the I
N
TELLIGE
N
T EYE sensor. This can lead to damage and malf
u
nction.
Do not place large o
b
jects near the sensor.
Also, keep heating
u
nits or h
u
midifiers o
u
tside the sensor’s detection area. This sensor can detect
u
ndesira
b
le o
b
jects.
Summary of Contents for SUPER MULTI NX G Series
Page 1: ...SiUS12 928_A Applied Models Inverter Multi Heat Pump G Series J Series...
Page 7: ...SiUS12 928_A Table of Contents vi...
Page 10: ...SiUS12 928_A 1 List of Functions Part 1 List of Functions 1 Functions 3...
Page 11: ...SiUS12 928_A List of Functions 2...
Page 17: ...SiUS12 928_A Specifications 8...
Page 23: ...SiUS12 928_A Specifications Specifications 14...
Page 25: ...SiUS12 928_A Printed Circuit Board Connector Wiring Diagram 16...
Page 37: ...SiUS12 928_A Function and Control 28...
Page 69: ...SiUS12 928_A Control Specification Function and Control 60...
Page 71: ...SiUS12 928_A Operation Manual 62...
Page 73: ...SiUS12 928_A Duct Free System Operation Manual 64 2 Duct Free System 2 1 Remote Controller...
Page 84: ...Duct Free System SiUS12 928_A 75 Operation Manual...
Page 85: ...SiUS12 928_A Duct Free System Operation Manual 76 2 8 TIMER Operation...
Page 86: ...Duct Free System SiUS12 928_A 77 Operation Manual...
Page 87: ...SiUS12 928_A Duct Free System Operation Manual 78 2 9 Note for Multi System...
Page 88: ...Duct Free System SiUS12 928_A 79 Operation Manual...
Page 97: ...SiUS12 928_A Slim Duct Built In System Operation Manual 88...
Page 99: ...SiUS12 928_A Service Diagnosis 90...
Page 169: ...SiUS12 928_A Removal Procedure 160...
Page 225: ...SiUS12 928_A Trial Operation and Field Settings 216...
Page 235: ...SiUS12 928_A Appendix 226...