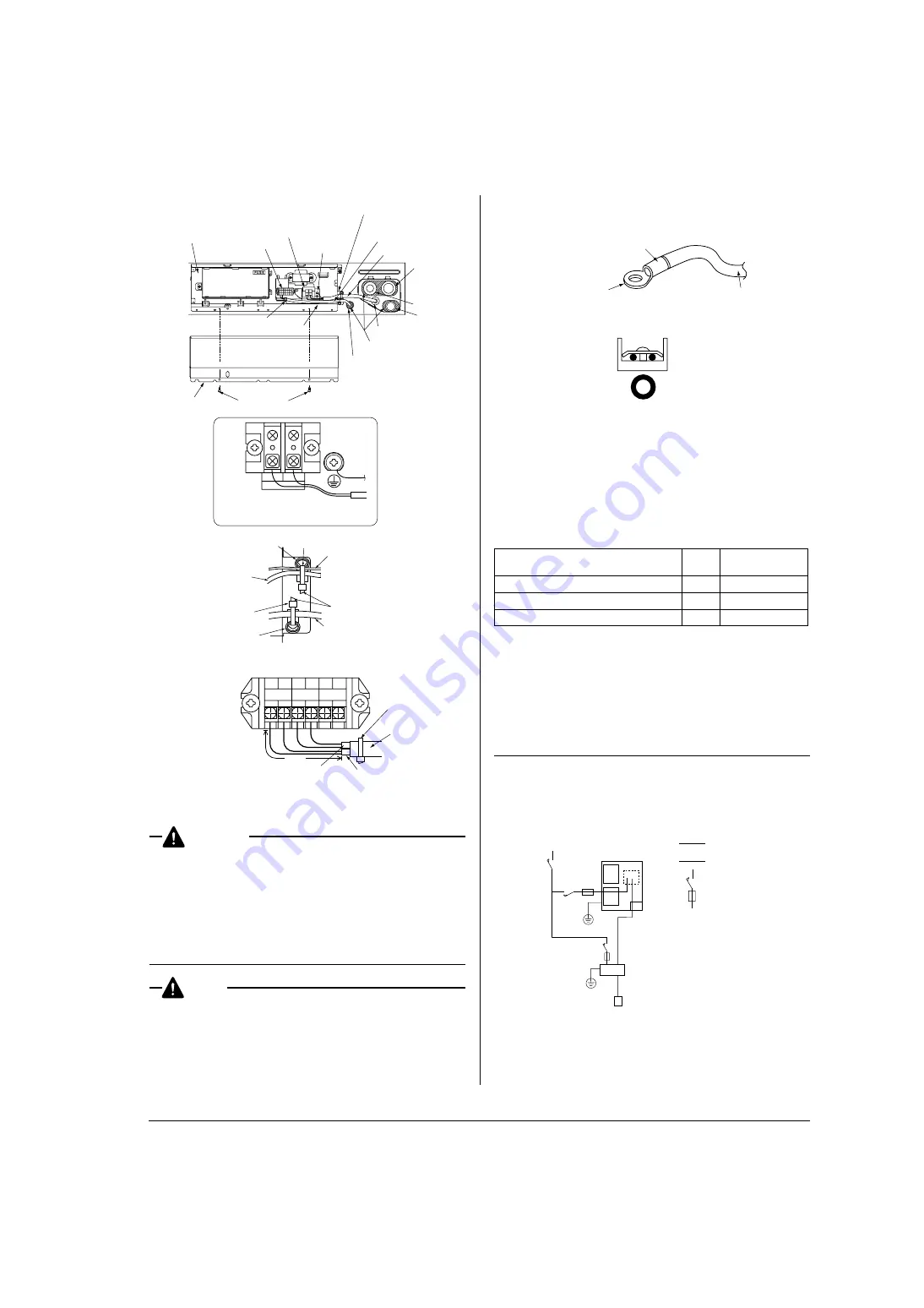
11
• In the insulating tube (11), it can let the remote controller wire
and transmission wire pass to 2.
WARNING
• Never connect power supply wiring to the terminal block for
remote controller wiring as this could damage the entire system.
• Use only specified wire and connect wires to the terminal
tightly. Be careful wires do not place external stress on termi-
nals. Keep wires in neat order so as to not obstruct other
equipment. Make sure that the electric box lid fits tightly.
Incomplete connections could result in overheating and, in
worse case, result in electric shock or fire.
NOTE
1. Use round crimp-style terminals for connecting wires to the
power supply terminal block.
If unavailable, observe the following points when wiring.
• Do not connect wires of different gauge to the same
power supply terminal.
(Looseness in the connection may cause overheating.)
• Use the specified electric wire. Connect the wire securely to
the terminal. Lock the wire down without applying excessive
force to the terminal. (Tightening torque: 0.97 ft lbf ±10%)
2. Tightening torque for the terminal screws.
• Use the correct screwdriver for tightening the terminal
screws. If the blade of screwdriver is too small, the head
of the screw might be damaged, and the screw will not be
properly tightened.
• If the terminal screws are tightened too hard, screws
might be damaged.
• Refer to the table below for the tightening torque of the
terminal screws.
Table 4
3. Do not connect wires of different gauge to the same ground
terminal. Looseness in the connection may deteriorate pro-
tection.
4. Outside of the unit, keep transmission wire at least 5 in.
away from power supply wire. The equipment may malfunc-
tion if subjected to electrical (external) noise.
5. For remote controller wire, refer to the “INSTALLATION
MANUAL OF REMOTE CONTROLLER” attached to the
remote controller.
9-2 WIRING EXAMPLE
• Fit the power supply wire of each unit with a switch and fuse
as shown in the drawing.
COMPLETE SYSTEM EXAMPLE
L
1
POWER SUPPLY
L
2
power supply
How to connect power supply
terminal block (2P)
Control box
Transmission
terminal block (6P)
Power supply
teminal block (2P)
Remote controller wire
and transmission wire
Refer to Fig. 27
Ground terminal
Power supply wire
Gas pipe
Liquid pipe
Drain pipe
Conduit
Corking or Putty
Resin bush (10)
Control box
lid secuing screw (2pcs.)
Control box lid
Insulating tube (11)
Clamp (4)
Fig. 26
Fastener
Clamp (4)
Clamp (4)
Ground wire
After securing the
cramp material
to the bracket,
cut off any extra
material.
Remote controller wire and
transmission wire
Fastener
Power supply wire
Fig. 27
P
1 P2 F1 F2 T1 T2
REMOTE
CNTRL
FORCED
OFF
TRANSMISSION
WIRING
Clamp (4)
Remote controller wire
Transmission
terminal block (6P)
Transmission wire
Insulating
tube (11)
1 in.
Fig. 28
Terminal
Size
Tightening torque
(ft-lbf)
Transmission terminal block (6P)
M3.5
0.58 – 0.72
Power supply terminal block (2P)
M4
0.87 – 1.06
Ground terminal
M4
0.87 – 1.06
Electric wire
Round crimp-style terminal
Attach insulation sleeve
Connect wires of the
same gauge to both side.
Power supply wire
Transmission wire
Switch
Fuse
Power supply
Main
switch
Remote controller
Indoor unit
Outdoor unit
Summary of Contents for SkyAir SkyAir FHQ42MVJU
Page 16: ...0510 3PN06240 2E EM04A051B FS...