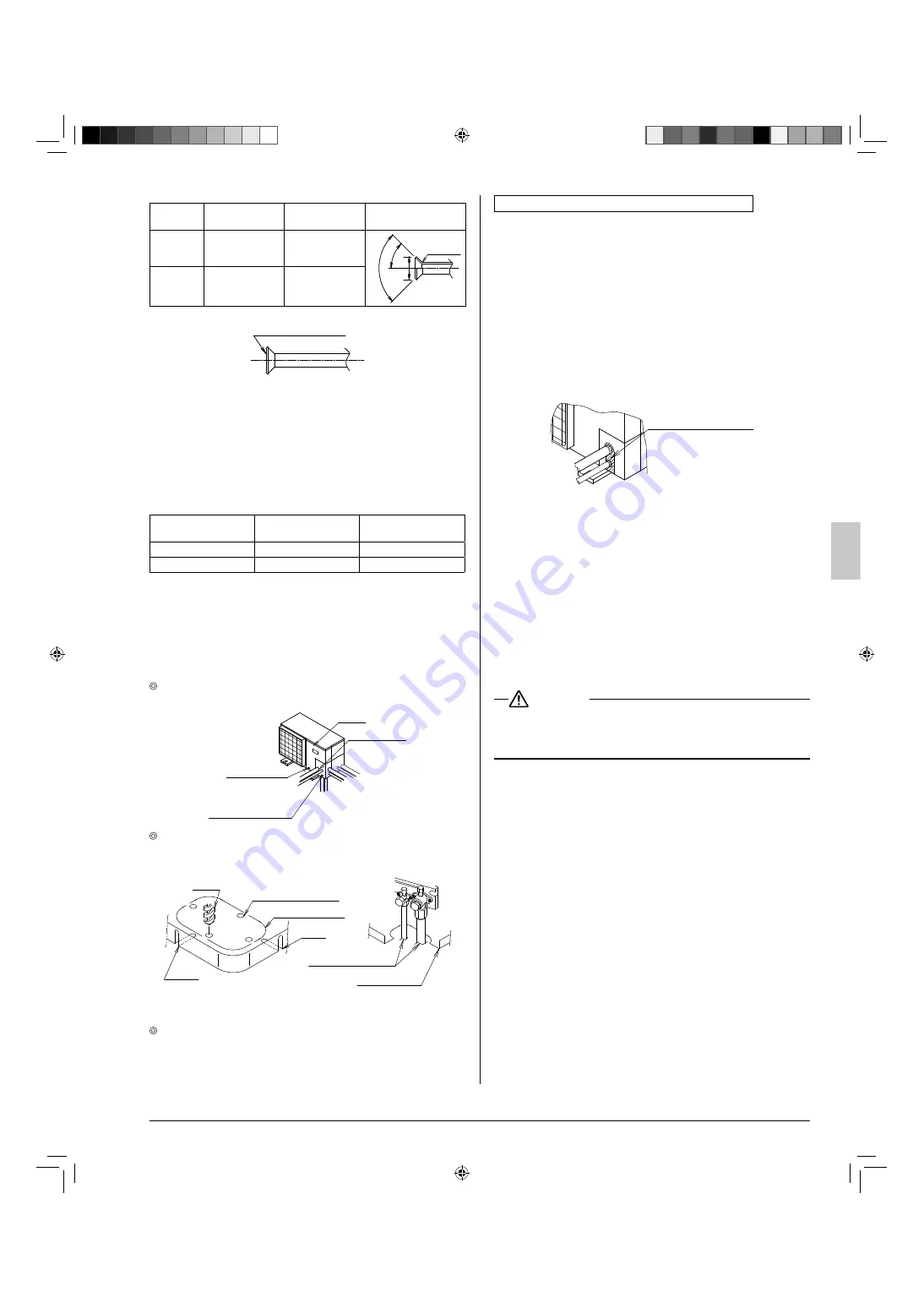
English
10
Pipe size
Tightening
torque (ft·lbf)
Flare dimension
A (in.)
Flare shape (in.)
φ
3/8”
24.1 - 29.4
0.504 - 0.520
A
45°± 2°
9
0°± 2°
R0.016
~0.031
φ
5/8”
45.6 - 55.6
0.760 - 0.776
Ester oil or ether oil
If you are obliged to install the unit without a torque wrench,
•
you may follow the installation method mentioned below.
After the work is fi nished, make sure to check that there is
no gas leak.
When you keep on tightening the fl are nut with a spanner,
•
there is a point where the tightening torque suddenly in-
creases.
From that position, further tighten the fl are nut the angle
shown below.
Pipe size
Tightening angle
(Guideline)
Recommended arm
length of tool (in.)
φ
3/8”
60°~90°
Approx. 7 7/8
φ
5/8”
30°~60°
Approx. 11 13/16
Disposal requirements
Dismantling of the unit, treatment of the refrigerant, oil and
eventual other parts should be comply the relevant local and
national regulations.
Refrigerant piping work procedure
6-4
The fi eld piping can be connected in three directions.
Piping cover
Screw for
front panel
Screw for piping
cover (front)
Front
panel
Lateral
direction
Front direction
Downward
direction
When connecting the piping downward, remove the knock-
out hole by making four holes in the middle on the each side
of the knockout hole with a drill.
Field piping
Bottom frame
Knockout hole
Drill
Slit
Middle on the side
Slit
Then cut out the corner of the bottom frame along the slits (in
two positions) by using a hacksaw.
After removing the parts, it is recommended to apply repair
paint on the edges, to prevent rusting.
Cautions on connecting the connection piping
When it is expected that water condensed in the stop valve
•
will reach the indoor unit through the gap between the heat
insulating material and the piping (for example, when the
outdoor unit is installed in a higher position than the indoor
unit), take proper action such as caulking the connection
area.
[Measures to prevent invasion of small creatures and litter]
Block all gaps in the piping penetration areas with putty or
•
heat insulating material (arranged in the local fi eld) as
shown in the fi gure below.
(If small creatures such as insects or litter enter the outdoor
unit, a short-circuit may be caused inside the control box.)
Putty or heat
insulating material
(arranged in local field)
Heat insulation of piping
6-5
Make sure to insulate the fi eld piping (on both the liquid line
•
and gas line) and refrigerant branching kit.
(If they are not insulated, water leakage may be caused.)
(The maximum temperature of the piping on the gas line is
about 248 °F during heating operation. Use an insulation
suffi ciently resistant to this temperature.)
Reinforce the refrigerant piping according to the installation
•
environment. If it is not reinforced, condensate may form on
the surface of the insulation.
WARNING
Make sure to insulate the fi eld piping up to the piping con-
•
nection area inside the unit. If the piping is exposed, dew
condensation and burn by contact may be caused.
Airtight test and vacuum drying
6-6
The unit has been checked for leaks by the manufacturer.
Confi rm that the valves are fi rmly closed before airtight test or
vacuumdrying.
To prevent entry of any impurities and insure suffi cient pres-
sure resistance, always use the special tools dedicated for
R410A.
Perform the following inspections securely after the
piping work.
Airtight test
•
- Make sure to use nitrogen gas. (For the
service port position, refer to the fi gure in “
Stop valve
operation method
”.)
[Procedure] Pressurize the air conditioner from the liquid
pipe and gas pipe up to 450 psi (Make sure not to exceed
450 psi). When the pressure does not drop for 24 hours, the
piping work shall be accepted.
If the pressure drops, check for leakage positions. (Confi rm
that there is no leakage, then release nitrogen.)
01_EN_3P281953-2A.indd 10
01_EN_3P281953-2A.indd 10
1/18/2011 9:27:20 AM
1/18/2011 9:27:20 AM