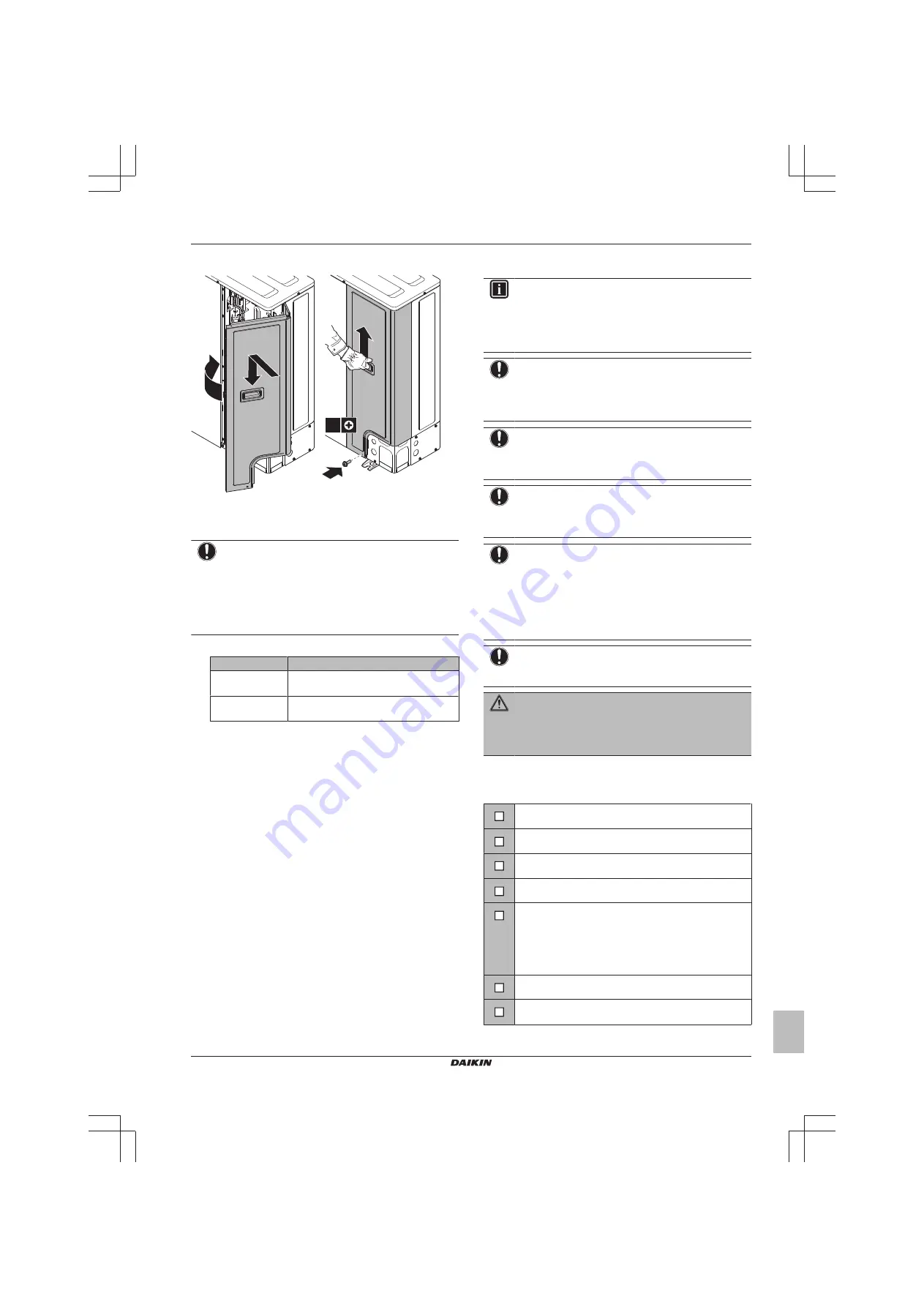
7 Commissioning
Installer reference guide
23
RZASG71~Y1
Sky Air Advance-series
4P486047-1 – 2017.04
6.8.2
To close the outdoor unit
1
3
2
4
1×
6.8.3
To check the insulation resistance of the
compressor
NOTICE
If, after installation, refrigerant accumulates in the
compressor, the insulation resistance over the poles can
drop, but if it is at least 1 MΩ, then the unit will not break
down.
▪ Use a 500 V mega-tester when measuring insulation.
▪ Do not use a mega-tester for low-voltage circuits.
1
Measure the insulation resistance over the poles.
If
Then
≥1 MΩ
Insulation resistance is OK. This procedure
is finished.
<1 MΩ
Insulation resistance is not OK. Go to the
next step.
2
Turn ON the power and leave it on for 6 hours.
Result:
The compressor will heat up and evaporate any
refrigerant in the compressor.
3
Measure the insulation resistance again.
7
Commissioning
7.1
Overview: Commissioning
This chapter describes what you have to do and know to
commission the system after it is installed.
Typical workflow
Commissioning typically consists of the following stages:
1
Checking the "Checklist before commissioning".
2
Performing a test run for the system.
7.2
Precautions when commissioning
INFORMATION
During the first running period of the unit, the required
power may be higher than stated on the nameplate of the
unit. This phenomenon is caused by the compressor, that
needs a continuous run time of 50 hours before reaching
smooth operation and stable power consumption.
NOTICE
Before starting up the system, the unit MUST be energised
for at least 6 hours. The crankcase heater needs to heat
up the compressor oil to avoid oil shortage and
compressor breakdown during startup.
NOTICE
NEVER operate the unit without thermistors and/or
pressure sensors/switches. Burning of the compressor
might result.
NOTICE
Do NOT operate the unit until the refrigerant piping is
complete (when operated this way, the compressor will
break).
NOTICE
Cooling operation mode
. Perform the test run in cooling
operation mode so that stop valves failing to open can be
detected. Even if the user interface was set to heating
operation mode, the unit will run in cooling operation mode
during 2‑3 minutes (although the user interface will display
the heating icon), and then automatically switch to heating
operation mode.
NOTICE
If you cannot operate the unit in test run, see
codes when performing a test run" on page 24
WARNING
If the panels on the indoor units are not installed yet, make
sure to power OFF the system after finishing the test run.
To do so, turn OFF operation via the user interface. Do
NOT stop operation by turning OFF the circuit breakers.
7.3
Checklist before commissioning
Do NOT operate the system before the following checks are OK:
You read the complete installation instructions, as
described in the
installer reference guide
.
The
indoor units
are properly mounted.
In case a wireless user interface is used: The
indoor unit
decoration panel
with infrared receiver is installed.
The
outdoor unit
is properly mounted.
The following
field wiring
has been carried out according
to this document and the applicable legislation:
▪ Between the local supply panel and the outdoor unit
▪ Between the outdoor unit and the indoor unit (master)
▪ Between the indoor units
There are NO
missing phases
or
reversed phases
.
The system is properly
earthed
and the earth terminals
are tightened.
Summary of Contents for RZASG100M7V1B
Page 31: ......