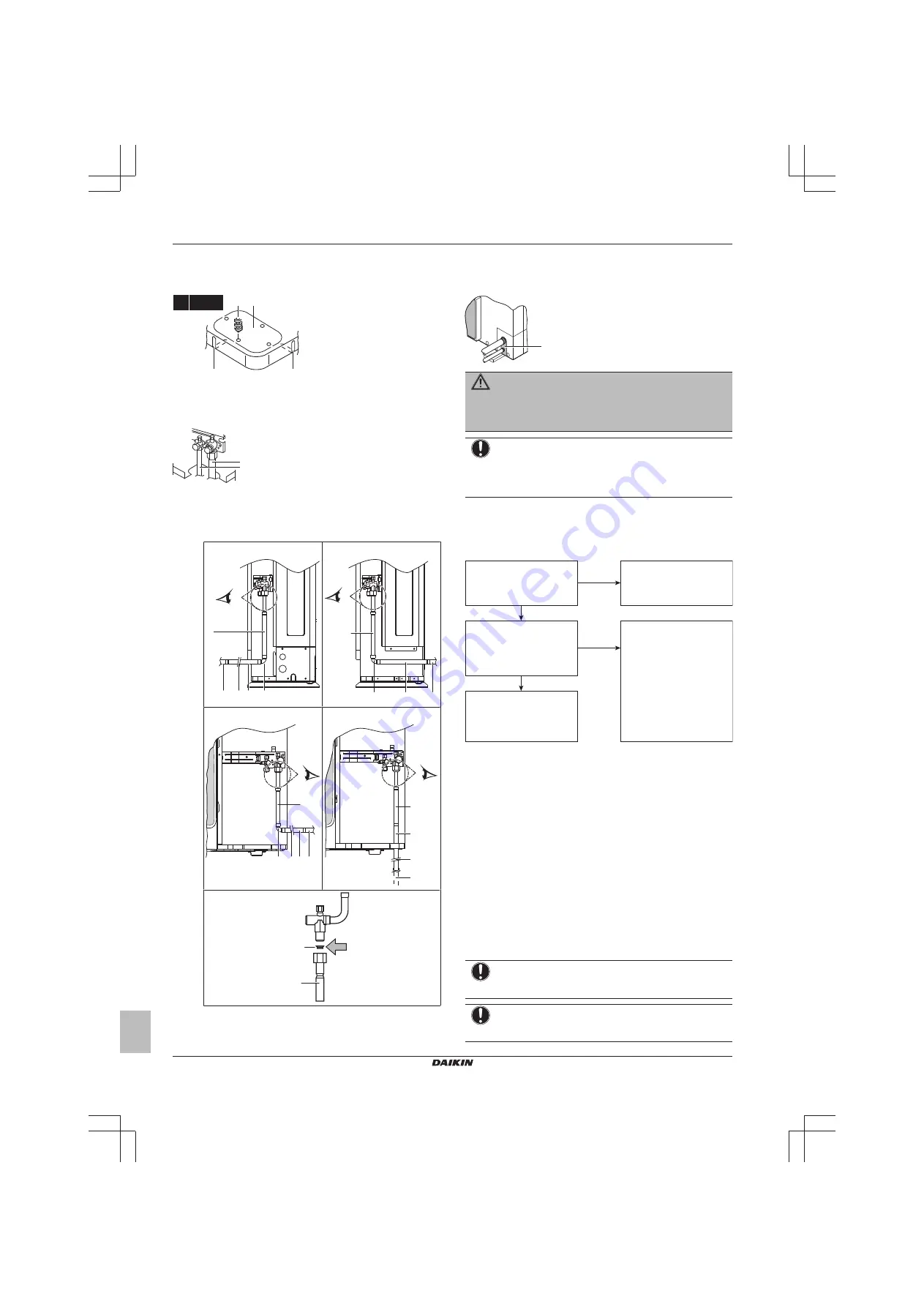
5 Installation
Installation and operation manual
10
RXYSQ6T8Y1B9
VRV IV-S system air conditioner
4P482276-1 – 2017.04
3
If you have chosen the downwards piping route:
▪ Drill (a, 4×) and remove the knockout hole (b).
▪ Cut out the slits (c) with a metal saw.
c
c
b
a
4× Ø6 mm
4
Do the following:
▪ Connect the liquid pipe (a) to the liquid stop valve.
▪ Connect the gas pipe (b) to the gas stop valve.
a
b
▪ Connect the gas piping accessories (c, c1, d, e), and cut
them to the required length (e1). This is necessary because
the size of the gas stop valve is Ø15.9 while the piping
between outdoor unit and first refrigerant branch kit is Ø19.1.
Possibility 1: To the front
A
e1 e
c
d
f
Possibility 2: To the back
A
c
d
e
f
Possibility 3: To the side
A
c
d e1 e f
Possibility 4: Downwards
A
c
e1
f
e
A
c1
c
c, c1
Gas piping accessory 1 + copper gasket (always use it)
d
Gas piping accessory 2
e, e1
Gas piping accessory 3 (cut it to the required length)
f
Field supply
5
Reattach the service cover and the piping intake plate.
6
Seal all gaps (example: a) to prevent snow and small animals
from entering the system.
a
WARNING
Provide adequate measures to prevent that the unit can be
used as a shelter by small animals. Small animals that
make contact with electrical parts can cause malfunctions,
smoke or fire.
NOTICE
Make sure to open the stop valves after installing the
refrigerant piping and performing vacuum drying. Running
the system with the stop valves closed may break the
compressor.
5.4
Checking the refrigerant piping
5.4.1
About checking the refrigerant piping
Refrigerant piping works are
finished?
The indoor units and/or
outdoor unit were already
powered ON?
Use procedure:
"Method 2: After power ON".
Finish piping work.
Use procedure:
"Method 1: Before power ON
(regular method)".
Yes
No
No
Yes
It is very important that all refrigerant piping work is done before the
units (outdoor or indoor) are powered on.
When the units are powered on, the expansion valves will initialise.
This means that they will close. Leak test and vacuum drying of field
piping and indoor units is impossible when this happens.
Therefore, there will be explained 2 methods for initial installation,
leak test and vacuum drying.
Method 1: Before power ON
If the system has not yet been powered on, no special action is
required to perform the leak test and the vacuum drying.
Method 2: After power ON
If the system has already been powered on, activate setting [2‑21]
(refer to
"6.1.4 To access mode 1 or 2" on page 17
). This setting
will open field expansion valves to guarantee a R410A piping
pathway and make it possible to perform the leak test and the
vacuum drying.
NOTICE
Make sure that all indoor units connected to the outdoor
unit are powered on.
NOTICE
Wait until the outdoor unit has finished the initialisation to
apply setting [2‑21].