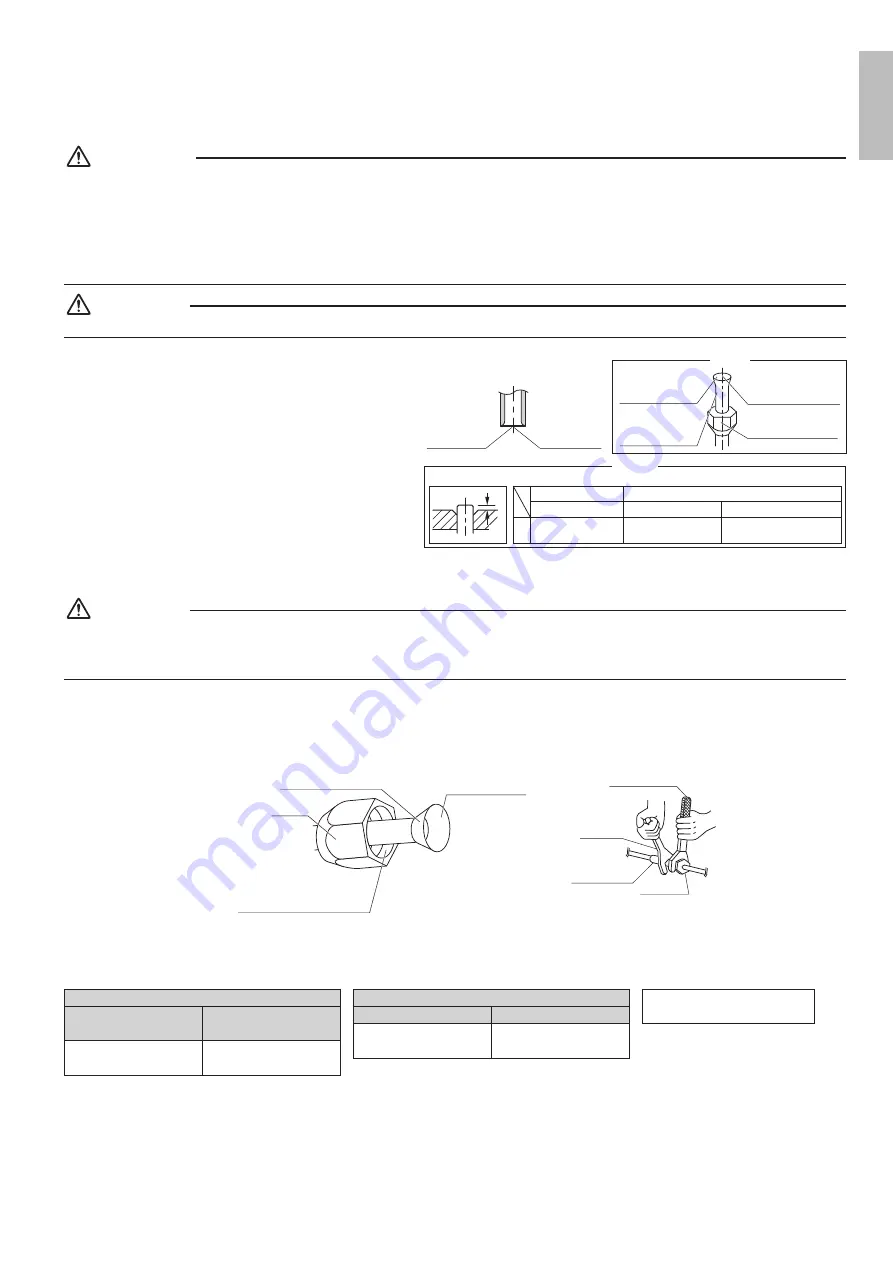
6
■
English
3.
Flaring the pipe end
WARNING
•
Do not apply mineral oil to the flare.
• Prevent mineral oil from getting into the system as this would reduce the service life of the units.
• Never use piping which has been used for previous installations. Only use parts which are delivered with this unit.
• Never install a dryer to this R410A unit in order to guarantee its service life.
• The drying material may dissolve and damage the system.
•
Improper flaring may result in refrigerant gas leakage.
CAUTION
Do not reuse joints which have been used once already.
1) Cut the pipe end with a pipe cutter.
2) Remove burrs with the cut surface facing
downward, so that the filings do not enter the
pipe.
3)
Put the flare nut on the pipe.
4) Flare the pipe.
5)
Check that the flaring has been done correctly.
Check
The flare
’
s inner
surface must be
flaw-free.
When flaring, do
not over-tighten
and crack.
The pipe end must be
evenly flared in a
perfect circle.
Make sure that
the flare nut is fitted.
Set exactly at the position shown below.
Flaring
A
Die
A
0-0.020 inch
(0-0.5mm)
Clutch-type
Flare tool for R410A
0.039-0.059 inch
(1.0-1.5mm)
Clutch-type (Rigid-type)
0.059-0.079 inch
(1.5-2.0mm)
Wing-nut type (Imperial-type)
Conventional flare tool
Cut exactly at
right angles.
Remove burrs.
4.
Refrigerant piping
CAUTION
•
Use the flare nut fixed to the main unit. (This is to prevent the flare nut from cracking as a result of deterioration over time.)
•
To prevent gas leakage, apply refrigeration oil only to the inner surface of the flare. (Use refrigeration oil for R410A.)
•
Use a torque wrench when tightening the flare nuts to prevent damage to the flare nuts and gas leakage.
•
Align the centers of both flares and tighten the flare nuts 3 or 4 turns by hand, then tighten them fully with a spanner and a
torque wrench.
Do not apply refrigeration
oil to the outer surface.
Flare nut
Apply refrigeration
oil only to the inner
surface of the flare.
Do not apply refrigeration oil to
the flare nut to avoid tightening
with excessive torque.
Apply oil
T
orque wrench
Piping union
Flare nut
Spanner
Tighten
Tightening torque
Flare nut
Piping connection
Gas side
3/8 inch (9.5mm)
24-1/8 – 29-1/2lbf • ft
(32.7-39.9N • m)
10-1/2 – 12-3/4lbf • ft
(14.2-17.2N • m)
Liquid side
1/4 inch (6.4mm)
Width across flats
Valve cap
11/16 inch (17mm)
10-1/2 – 12-5/8lbf • ft
(14.2-17.2N • m)
12-5/8 – 15-3/8lbf • ft
(17.0-21.0N • m)
8 – 10-7/8lbf • ft
(10.7-14.7N • m)
3/4 inch (19mm)
Service port cap
English
01_EN_3P658798-1.indd 6
2021/07/14 12:51:31