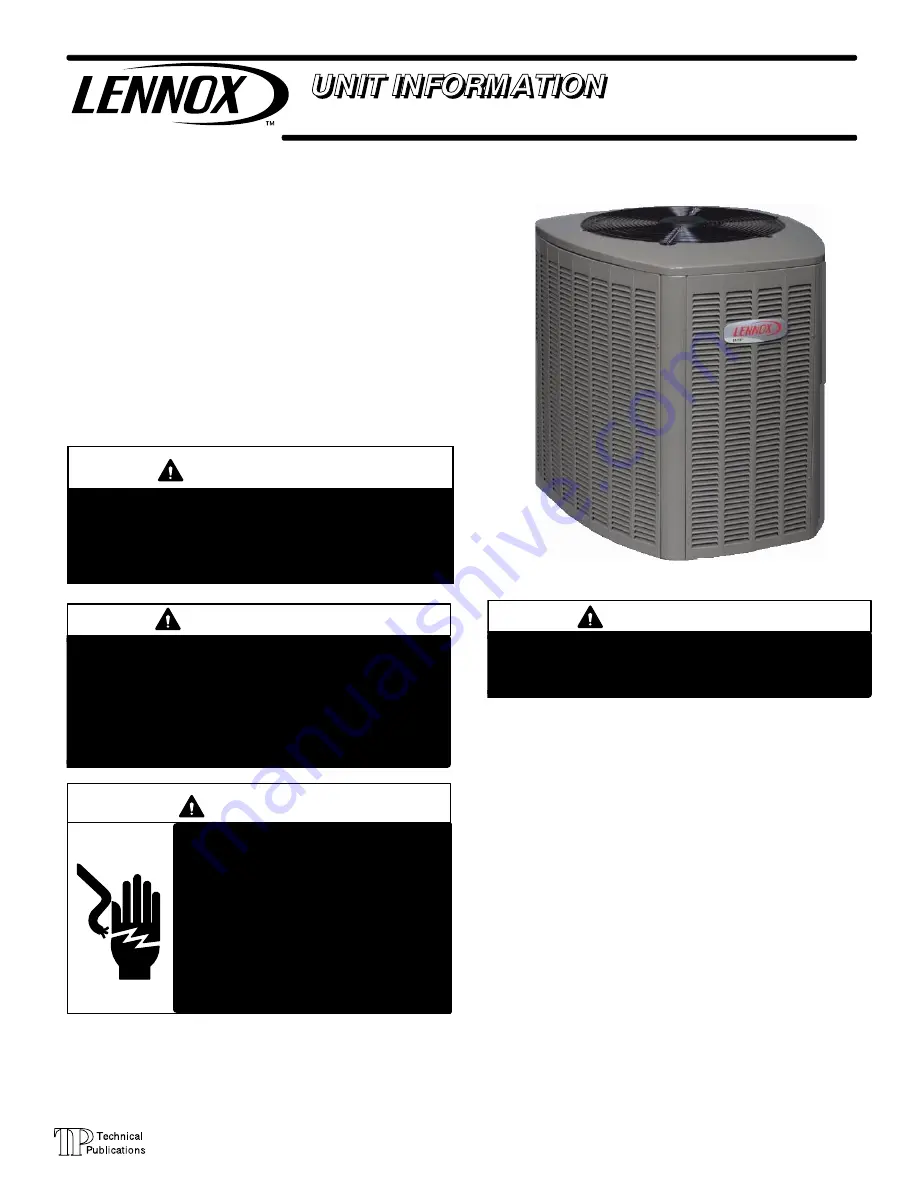
Page 1
©
2005 Lennox Industries Inc.
Corp. 0521−L9
XC13
Service Literature
Revised 12−2005
XC13 SERIES UNITS
The XC13 is a high efficiency residential split−system con-
densing unit, which features a scroll compressor and
R−410A refrigerant. XC13 units are available in sizes rang-
ing from 1 1/2 through 5 tons. The series is designed for use
with an expansion valve or RFC (approved for use with
R−410A) in the indoor unit. This manual is divided into sec-
tions which discuss the major components, refrigerant sys-
tem, charging procedure, maintenance and operation se-
quence.
Information contained in this manual is intended for use by
qualified service technicians only. All specifications are sub-
ject to change.
WARNING
Improper installation, adjustment, alteration, service
or maintenance can cause property damage, person-
al injury or loss of life. Installation and service must
be performed by a qualified installer or service
agency.
WARNING
Warranty will be voided if covered equipment is re-
moved from original installation site. Warranty will
not cover damage or defect resulting from:
Flood, wind, lightning, or installation and operation
in a corrosive atmosphere (chlorine, fluorine, salt,
recycled waste water, urine, fertilizers, or other dam-
aging chemicals).
DANGER
Shock Hazard
Remove all power at disconnect
before removing access panel.
Single phase XC13 units use single-
pole contactors. Potential
exists for electrical shock resulting
in injury or death.
Line voltage exist at all components
(even when unit is not in operation).
IMPORTANT
Operating pressures of this R−410A unit are higher
than pressures in R−22 units. Always use service
equipment rated for R410A.
TABLE OF CONTENTS
. . . . . . . . . . . . . . . . . . . . . . . . . . .
Specifications / Electrical Data
. . . . . . . .
I Application
. . . . . . . . . . . . . . . . . . . . . . . .
II Unit Components
. . . . . . . . . . . . . . . . . .
III Refrigeration System
. . . . . . . . . . . . . .
IV Charging
. . . . . . . . . . . . . . . . . . . . . . . .
V Service and Recovery
. . . . . . . . . . . . .
VI Maintenance
. . . . . . . . . . . . . . . . . . . . .
VII Wiring and Sequence of Operation
.