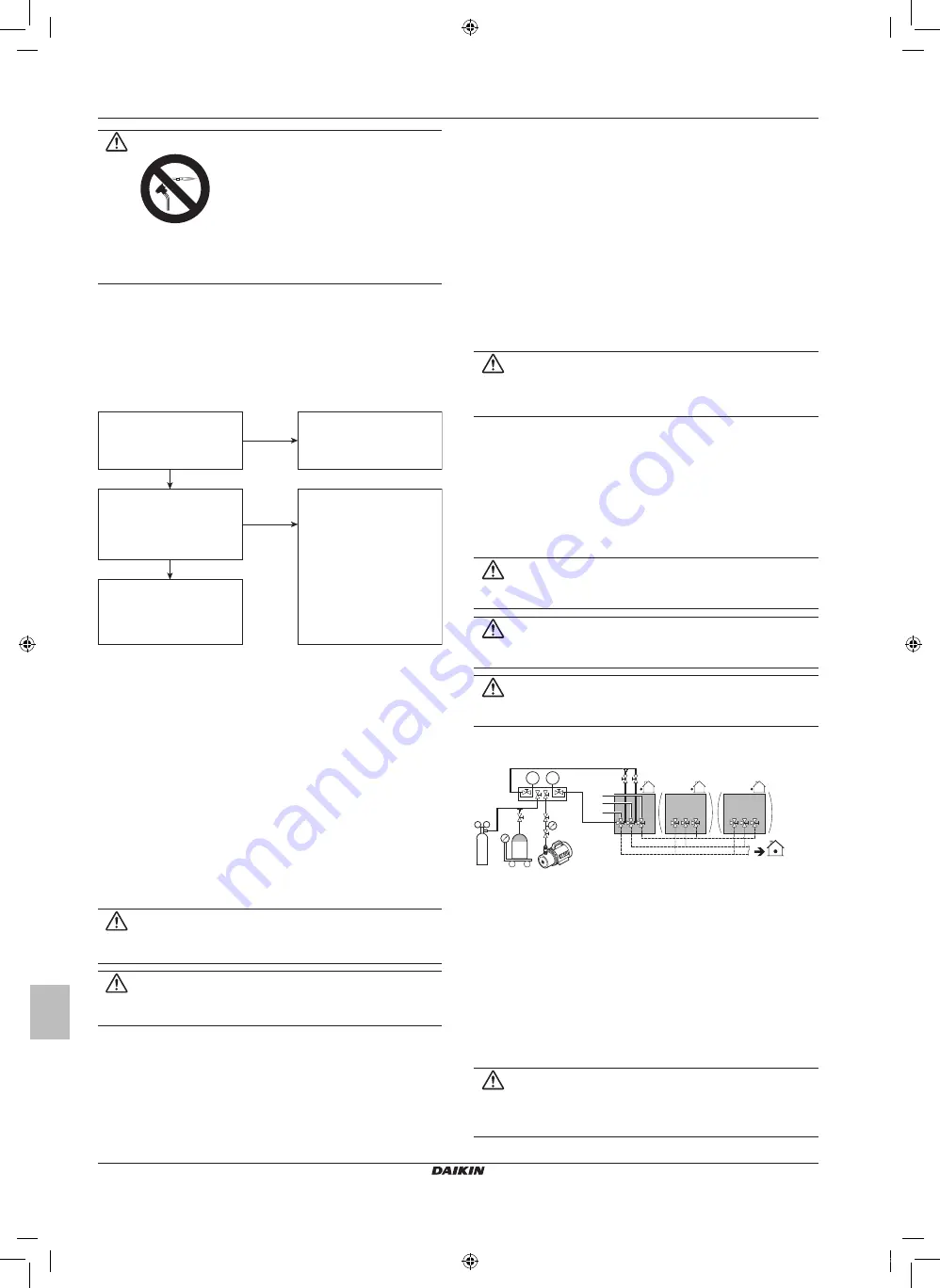
5 Installation
Installation manual
24
RWEQ96~432TAYD
∗
+ RWEQ96~432TATJ
∗
VRV W T-Series water-cooled system air conditioner
WARNING
Never remove the pinched piping by brazing.
Any gas or oil remaining inside the stop valve may blow off
the pinched piping.
6
Make sure that no particles remain in the pipe. Blow out any
particles with compressed air.
5 .4
Checking the refrigerant piping
5 .4 .1
About checking the refrigerant piping
Refrigerant piping works are
finished?
The indoor units and/or
outside unit were already
powered ON?
Use procedure:
"Method 2: After power ON".
Finish piping work.
Use procedure:
"Method 1: Before power ON
(regular method)".
Yes
No
No
Yes
It is very important that all refrigerant piping work is done before the
units (outside or indoor) are powered on.
When the units are powered on, the expansion valves will initialize.
This means that they will close. Leak test and vacuum drying of field
piping and indoor units is impossible when this happens.
Therefore, there will be explained 2 methods for initial installation,
leak test and vacuum drying.
Method 1: Before power ON
If the system has not yet been powered on, no special action is
required to perform the leak test and the vacuum drying.
Method 2: After power ON
If the system has already been powered on, activate setting [2-21]
(refer to "7.2.4 To access mode 1 or 2" on page 36). This setting will
open field expansion valves to guarantee a R410A piping pathway
and make it possible to perform the leak test and the vacuum drying.
NOTE
Make sure that all indoor units connected to the outside
unit are powered on.
NOTE
Wait until the outside unit has finished the initialization to
apply setting [2-21].
Leak test and vacuum drying
Checking the refrigerant piping involves:
▪ Checking for any leakages in the refrigerant piping.
▪ Performing vacuum drying to remove all moisture, air or nitrogen
in the refrigerant piping.
If there is a possibility of moisture being present in the refrigerant
piping (for example, water may have entered the piping), first carry
out the vacuum drying procedure below until all moisture has been
removed.
All piping inside the unit has been factory tested for leaks.
Only field installed refrigerant piping needs to be checked.
Therefore, make sure that all the outside unit stop valves are firmly
closed before performing leak test or vacuum drying.
NOTE
Make sure that all (field supplied) field piping valves are
OPEN (not outside unit stop valves!) before you start leak
test and vacuuming.
For more information on the state of the valves, refer to
"5.4.3 Checking refrigerant piping: Setup" on page 24.
5 .4 .2
Checking refrigerant piping: General
guidelines
Connect the vacuum pump through a manifold to the service port of
all stop valves to increase efficiency (refer to "5.4.3 Checking
refrigerant piping: Setup" on page 24).
NOTE
Use a 2-stage vacuum pump with a non-return valve or a
solenoid valve that can evacuate to 500 microns or less.
NOTE
Make sure the pump oil does not flow oppositely into the
system while the pump is not working.
NOTE
Do not purge the air with refrigerants. Use a vacuum pump
to evacuate the installation.
5 .4 .3
Checking refrigerant piping: Setup
p< p>
R410A
N2
C
(1)
D
b
c
e
a
g
h
f
d
A
B
a
Pressure reducing valve
b
Nitrogen
c
Weighing scales
d
Refrigerant R410A tank (siphon system)
e
Vacuum pump
f
Liquid line stop valve
g
Gas line stop valve
h
High pressure/low pressure gas line stop valve
A
Valve A
B
Valve B
C
Valve C
(1)
D
Valve D
(1) Only for heat recovery mode.
NOTE
Do not connect the vacuum pump to the suction gas stop
valve if the unit is intended to run in heat pump mode. This
will increase the risk of unit failure.
01_EN_4P602454-1C.indd 24
2020/07/29 16:16:46