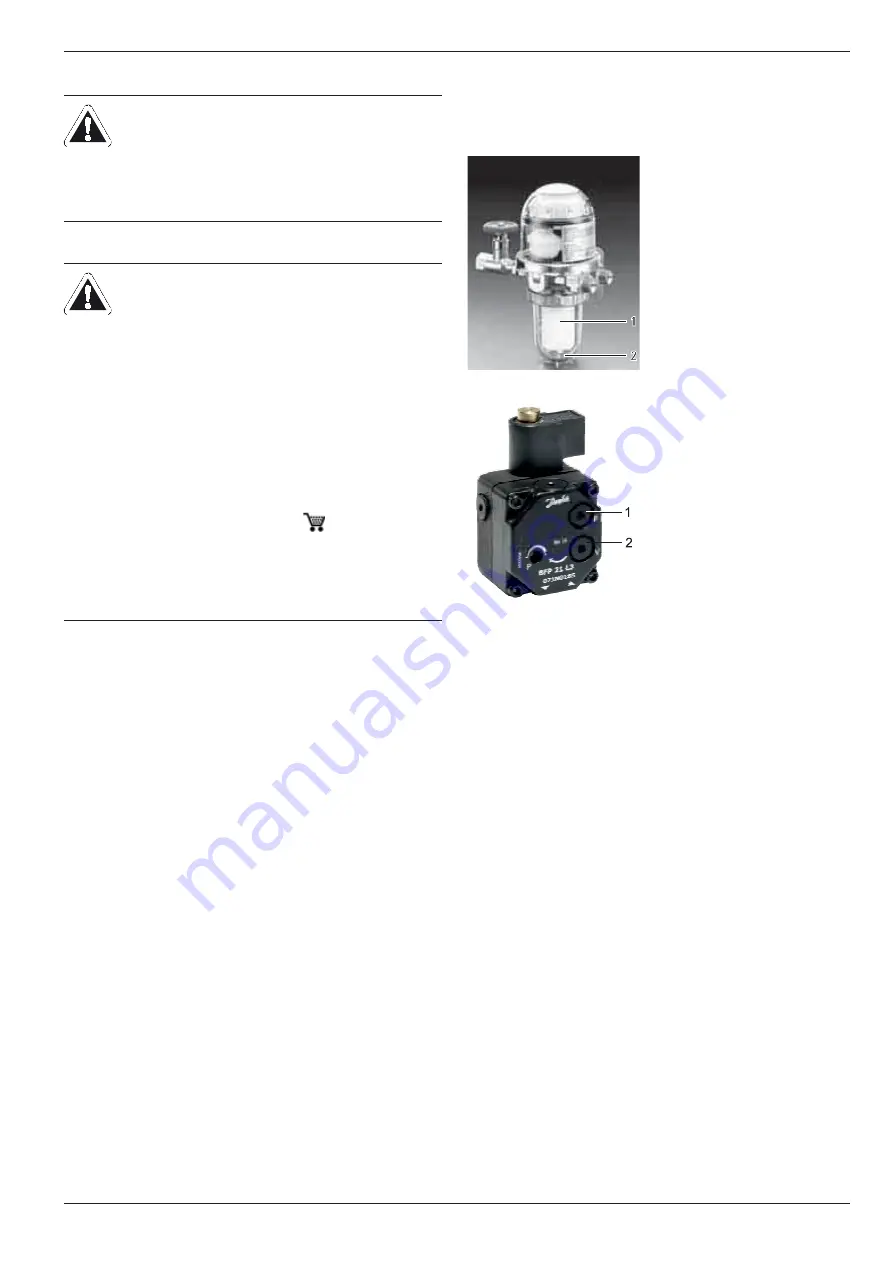
5
x
Start-up
FA ROTEX A1 BOe - 02/2014
21
5 Start-up
Incorrect start-up makes the manufacturer's guarantee for the
unit void. If you have questions, please contact our Technical
Customer Service.
5.1 Initial start-up
Once the ROTEX A1 BO is installed and fully connected, it can
be put into operation by expert technicians.
Requirements
– The ROTEX A1 BO is installed correctly. If a pressure device
is used as separate oil pump, the installation site must also be
secured by using a leakproof tray and a filter cup made of
metal, (see chapter 4.4.1).
– The ROTEX A1 BO is fully connected.
– The heating system is filled and charged at the correct pres-
sure.
– The oil valves are open and the oil line is topped up.
Tests prior to start-up
Ɣ
Check all connections for leakage.
Ɣ
Check all the points in the checklist in section 5.2. Log the test
results on the checklist.
Only if
all points
on the checklist can be answered with
yes
may
the ROTEX A1 BO be put into operation on a
temporarary
basis.
Bleeding the oil line, checking the oil pressure
The oil line must be completely vented at the beginning of the
start-up and the oil pressure must be checked.
Ɣ
Connect vacuum meter to the oil pump (Vacuum meter
connection, fig. 5-2, pos. 2)
Ɣ
Switch on the mains switch. Wait for the start phase.
Ɣ
Open the venting screw on the oil filter.
Ɣ
Vent oil line and measure the oil pressure on vacuum meter.
Î
The vacuum may be maximum 0.4 bar (better: 0.2 bar).
Start-up
Ɣ
Switch on the mains switch. Wait for the start phase.
Ɣ
Adjust the hand operation on the ROTEX Controller
RoCon BF [Special Level] (see documentation "ROTEX
Controller RoCon BF").
WARNING!
If not started up properly, a ROTEX A1 BO can be a
health and safety risk endangering human life and its
operation may be adversely affected.
Ɣ
The ROTEX A1 BO may only be started up by
authorised and trained heating experts.
CAUTION!
A ROTEX A1 BO which was put into operation incor-
rectly can cause damge to property and the envi-
ronment.
Ɣ
Observe the relevant regulations of technology to
prevent creation of corrosion products and
deposits.
Ɣ
Measures for desalination, softening or hardness
stabilization are necessary, if the filling and top-up
water has a high total hardness (>3 mmol/l - sum
of the calcium and magnesium concentrations,
calculated as calcium carbonate).
– We recommend Fernox scale and corrosion
protection agent
KSK
(
15 60 50)
.
Ɣ
Whilst the installation is running, the water
pressure is monitored automatically by the boiler
control system. If the water pressure is too low,
this will be displayed in the boiler control system,
fill up if necessary.
1
Filter
2
Filter cup
Fig. 5-1
Oil connection with bleeding oil filter
1
Manometer connection
2
Vacuum meter connection
Fig. 5-2
Oil pump