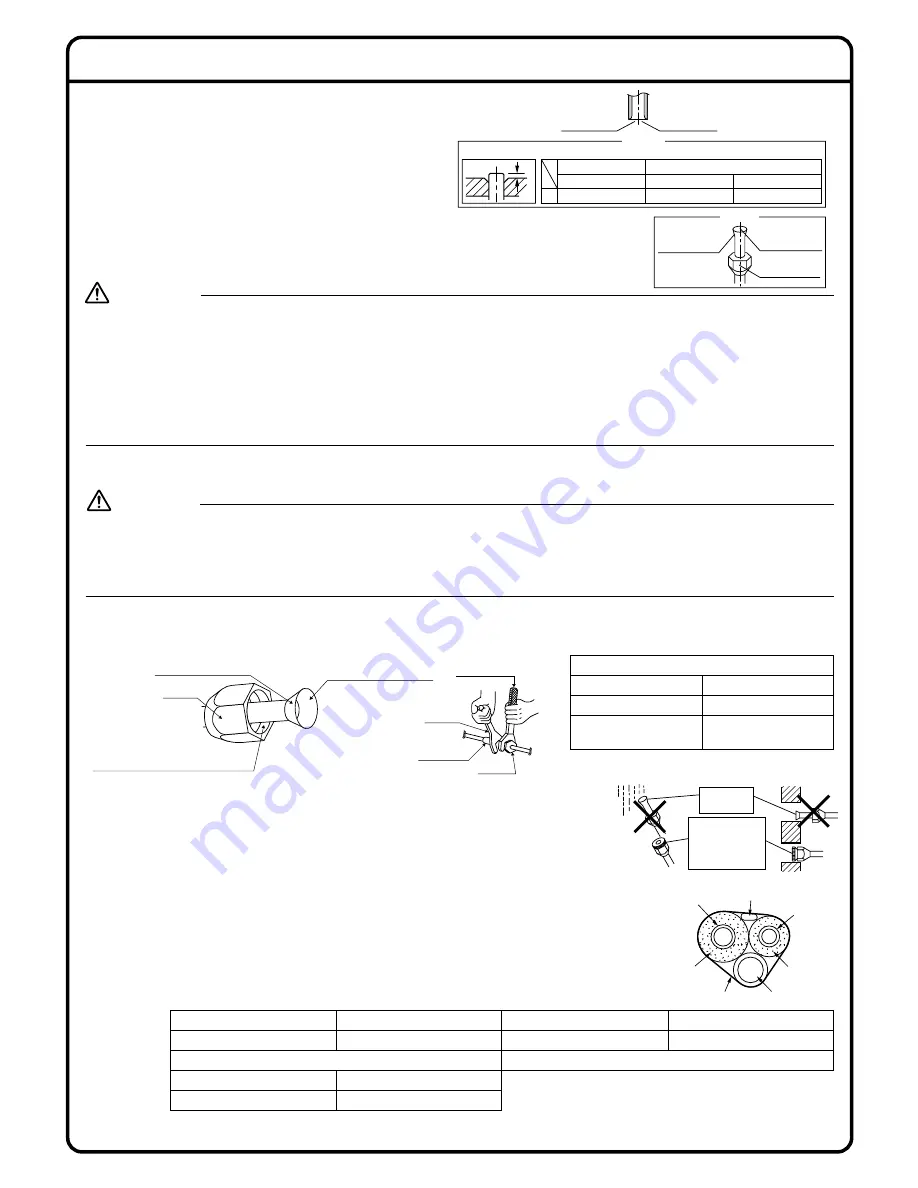
Align the centers of both flares and tighten the flare nuts 3 or 4 turns by hand. Then tighten them fully
with the torque wrenches.
Refrigerant Piping Work
2.
Refrigerant piping.
2-1. Caution on piping handling.
1) Protect the open end of the pipe against dust and moisture.
2) All pipe bends should be as gentle as possible. Use a pipe bender for bending.
2-2. Selection of copper and heat insulation materials.
• When using commercial copper pipes and fittings, observe the following:
1) Insulation material: Polyethylene foam
Heat transfer rate: 0.041 to 0.052W/mK (0.024-0.030Btu/fth˚F (0.035-0.045kcal/mh˚C))
Refrigerant gas pipe’s surface temperature reaches 230˚F (110˚C) max.
Choose heat insulation materials that will withstand this temperature.
2) Be sure to insulate both the gas and liquid piping and to provide
insulation dimensions as below.
3) Use separate thermal insulation pipes for gas and liquid refrigerant pipes.
Flare nut tightening torque
Gas side
Liquid side
45.6-55.6ft
l
lbf
(61.8-75.4N
l
m)
24.1-29.4ft
l
lbf
(32.7-39.9N
l
m)
5/8 inch (15.9mm)
3/8 inch (9.5mm)
1) Use the flare nut fixed to the main unit. (To prevent cracking of the flare nut by aged deterioration.)
2) To prevent gas leakage, apply refrigeration oil only to the inner surface of the flare. (Use refrigeration
oil for R410A.)
3) Use torque wrenches when tightening the flare nuts to prevent damage to the flare nuts and gas leakage.
CAUTION
1.
Flaring the pipe end.
1) Cut the pipe end with a pipe cutter.
2) Remove burrs with the cut surface facing
downward so that the chips do not enter the
pipe.
3) Put the flare nut on the pipe.
4) Flare the pipe.
5) Check that the flaring is properly made.
1) Do not use mineral oil on flared part.
2) Prevent mineral oil from getting into the system as this would reduce the lifetime of the units.
3) Never use piping which has been used for previous installations. Only use parts which are delivered
with the unit.
4) Never install a drier to this R410A unit in order to guarantee it’s lifetime.
5) The drying material may dissolve and damage the system.
6) Incomplete flaring may cause refrigerant gas leakage.
WARNING
Gas pipe thermal insulation
Liquid side
Gas side
Liquid pipe thermal insulation
I.D. 0.630-0.787 inch (16-20mm)
O.D. 3/8inch (9.5mm)
O.D. 5/8 inch (15.9mm)
I.D. 0.472-0.591 inch (12-15mm)
Minimum bend radius
Thickness 0.393 inch (10mm) Min.
1-3/16 inch (30mm) or more
1-15/16 inch (50mm) or more
Thickness 0.031 inch (0.8mm) (C1220T-O)
Thickness 0.039 inch (1mm) (C1220T-O)
Wall
If no flare cap is
available, cover the
flare mouth with
tape to keep dirt or
water out.
Be sure to
place a cap.
Rain
Gas pipe
Liquid pipe
Gas pipe
insulation
Liquid pipe
insulation
Finishing tape
Drain hose
Inter-unit wiring
Torque wrench
Piping union
Flare nut
Do not apply refrigeration
oil to the outer surface.
Flare nut
Apply refrigeration oil to the
inner surface of the flare.
Do not apply refrigeration oil to the flare
nut to avoid tightening with over torque.
Spanner
[Apply oil]
[Tighten]
(Cut exactly at
right angles.)
Remove burrs
Set exactly at the position shown below.
A
Flaring
Die
A
0-0.020 inch (0-0.5mm)
Clutch-type
Flare tool for R410A
0.039-0.059 inch (1.0-1.5mm)
Clutch-type (Rigid-type)
0.059-0.079 inch (1.5-2.0mm)
Wing-nut type (Imperial-type)
Conventional flare tool
Check
Flare’s inner
surface must
be flaw-free.
The pipe end must
be evenly flared in
a perfect circle.
Make sure that the
flare nut is fitted.
Summary of Contents for M08B128
Page 10: ...3P228446 2B M08B128...