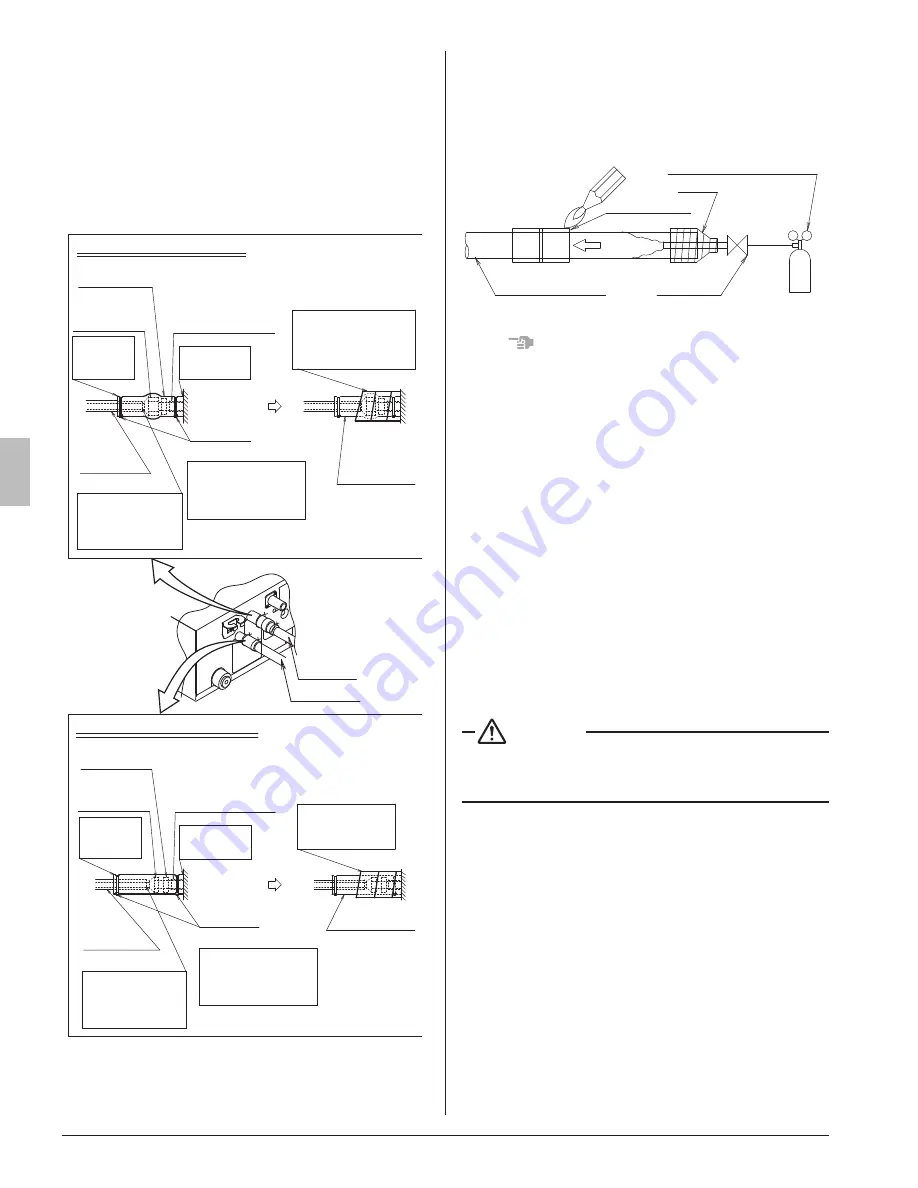
9
English
•
After leak test, referring to
Fig. 11
, insulate both the
gas and liquid piping connection with the attached joint
insulating material (4) and (5) to prevent the pipings from
getting exposed.
Then, tighten both the ends of insulating material with
the clamp (8).
•
Wrap the sealing material (Medium) (7) around the joint
insulating material (4) and (5) (flare nut section), both the
gas and liquid piping.
•
Make sure to bring the seam of joint insulating material
(4) and (5) to the top.
Joint insulating
material (4)
(accessory)
Gas piping
Liquid piping
Liquid piping insulating method
Indoor unit
Indoor unit
Clamp (8)
(accessory)
Sealing
material (7)
Medium
(accessory)
Clamp (8)
(accessory)
Piping
insulating
material
(field supply)
Gas piping insulating method
Joint insulating
material (5)
(accessory)
Piping insulating
material (main unit)
Bring the
seam
to the top.
Flare nut
connection
Piping
insulating
material
(field supply)
Do not leave
clearance.
Flare nut
connection
Bring the
seam
to the top.
Do not leave
clearance.
Piping insulating
material (main unit)
Sealing material
(7) Medium
(accessory)
Wind around the
piping until top of the
flare nut connection,
beginning at the base.
Do not expose the
piping in order to
prevent the vapor
condensation.
Tighten the portion
where overlapped by
the piping insulating
material.
Tighten the portion
where overlapped by
the piping insulating
material.
Do not expose the
piping in order to
prevent the vapor
condensation.
Wind around the
piping, beginning
at the base.
Fig. 11
•
Before brazing refrigerant piping, have nitrogen flow
through the refrigerant piping and substitute air with
nitrogen (NOTE 1)
(Refer to Fig. 12)
. Then, carry out
brazing (NOTE 2).
After all the brazing works are finished, carry out flare
connection with the indoor unit.
(Refer to Fig. 11)
Pressure reducing valve
Nitrogen
Taping
Stop valve
Brazing place
Nitrogen
Refrigerant piping
Fig. 12
NOTE
1.
The proper pressure for having nitrogen flow through
the piping is approximately 2.9 psi (0.02 MPa) , a pres
-
sure that makes one feel like slight breeze and can be
obtained through a pressure reducing valve.
2.
Do not use flux when brazing refrigerant piping.
Use phosphor copper brazing filler metal (BCuP-2,
B-Cu93P-710/795) that does not require flux.
(If chlorinated flux is used, the piping will be corroded
and, in addition if fluorine is contained, the refrig erant
oil will be deteriorated and the refrigerant circuit will be
affected badly.)
3.
When carrying out air tight test of refrigerant piping
and the indoor unit after the installation of indoor unit is
finished, confirm the connecting outdoor unit installation
manual for test pressure.
Refer to also the outdoor unit installation manual or tech-
nical document for refrigerant piping.
4.
In case of refrigerant shortage due to forgetting addition-
al refrigerant charge etc., it will result in malfunc tion such
as does not cool or does not heat.
Refer to the outdoor unit installation manual or technical
document for refrigerant piping.
CAUTION
Do not use antioxidant when brazing piping.
It may result in malfunction of components and clogging of
piping due to residue.
01_EN_3P184443-13Z.indd 9
2/15/2018 9:15:27