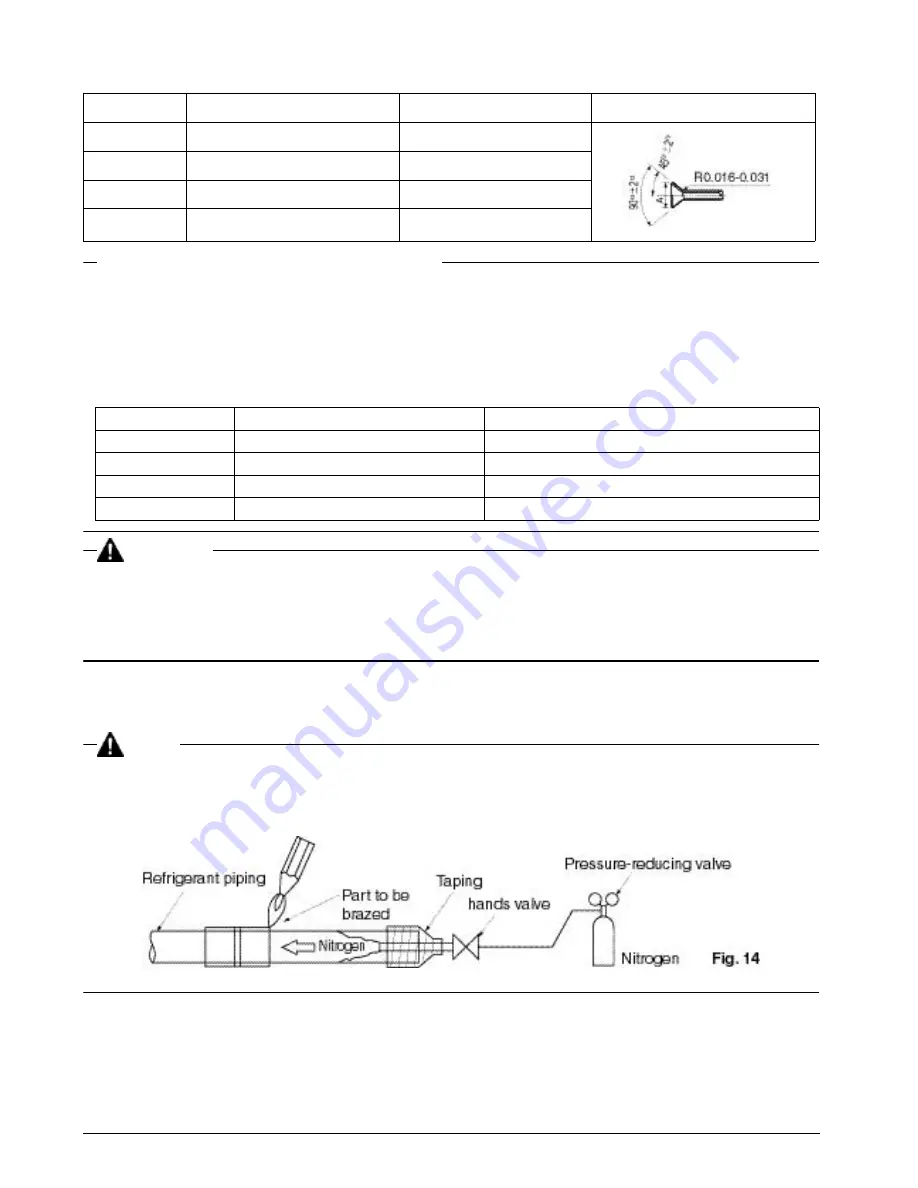
11
•
Refer to Table 1 for tightening torque.
Table 1
Not recommendable but in case of emergency
You must use a torque wrench but if you are obliged to install the unit without a torque wrench, you may
follow the installation method mentioned below.
After the work is finished, make sure to check that there is no gas leak.
When you keep on tightening the flare nut with a spanner, there is a point where the tightening torque
suddenly increases. From that position, further tighten the flare nut the angle shown below:
Table 2
CAUTION
CAUTION TO BE TAKEN WHEN BRAZING REFRIGERANT PIPING
“Do not use flux when brazing refrigerant piping. Therefore, use the phosphor copper brazing filter metal
(BCuP) which does not require flux.”
(Flux has extremely harmful influence on refrigerant piping system. For instance, if the chlorine based flux is
used, it will cause pipe corrosion or, in particular, if the flux contains fluorine, it will damage the refrigerant oil.)
•
When brazing the refrigerant piping, only begin brazing after having carried out nitrogen substitution
(NOTE 1) or while inserting nitrogen into the refrigerant piping (NOTE 2). Once this is done, connect the
indoor unit with a flared or a flanged connection.
NOTE
1.
Refer to the “Manual for Multi Installation for Buildings” for directions on how to carry out nitrogen
substitution. (Inquire with your dealer.)
2.
Nitrogen should be set to 2.9 psi with a pressure-reducing valve if brazing while inserting nitrogen into the
piping.
(Refer to Fig. 14)
•
After checking for gas leaks, be sure to insulate the pipe connections using the supplementary piping
insulation tubing and insulating tape (4). The insulating tape (4) should be wrapped from the L-shaped bend
all the way to the end inside the unit.
(Refer to Fig. 15)
Pipe size
Tightening torque (ft-lbf)
Flare dimensions A (in.)
Flare shape (in.)
φ
1/4”
10.5 – 12.7
0.343 – 0.358
φ
3/8”
24.1 – 29.4
0.504 – 0.520
φ
1/2”
36.5 – 44.5
0.638 – 0.654
φ
5/8”
45.6 – 55.6
0.760 – 0.776
Pipe size (in.)
Further tightening angle
Recommended arm length of tool (in.)
φ
1/4”
60 to 90 degrees
Approx. 5 7/8”
φ
3/8”
60 to 90 degrees
Approx. 7 7/8”
φ
1/2”
30 to 60 degrees
Approx. 9 13/16”
φ
5/8”
30 to 60 degrees
Approx. 11 13/16”