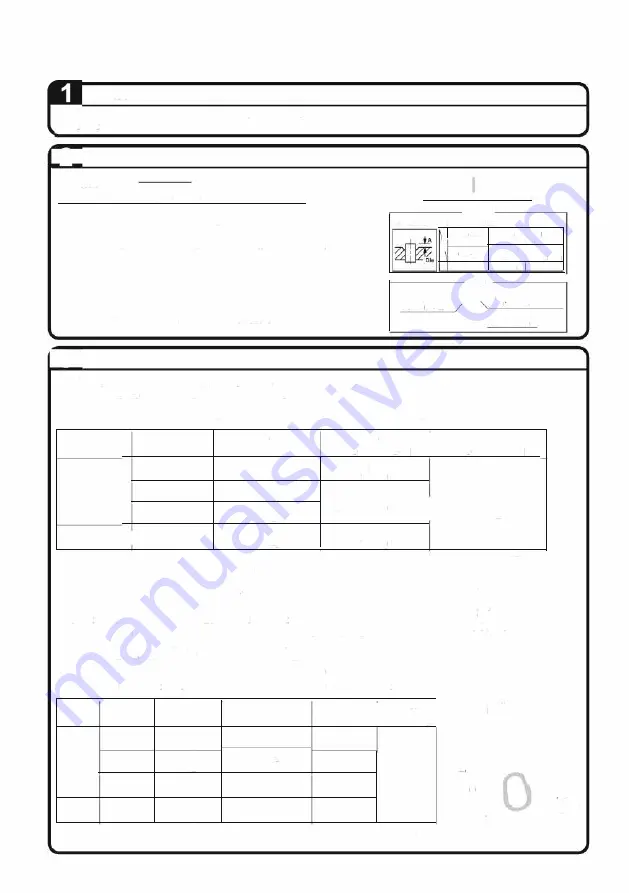
9
OUTDOOR UNIT
INSTALLING THE OUTDOOR UNIT
• When installing the outdoor unit, refer to
"Precautions for Selecting a Location"
and the
"Outdoor Unit
Installation Diagram".
i'..111
FLARING THE PIPE END
it,
WARNING
c"' '"'""• at
[!]
Incomplete flaring may result refrigerant gas leakage.
��Remove burrs.
Flaring
1) Cut the pipe end with a pipe cutter.
Set exactly at the position shown below.
Flare
tool
Conventional
flare tool
2) Remove burrs with the cut surface facing downward, so that the fillings
\ for
R41 0AIR32
Clutch-type I Wing-nut
type
do not enter the pipe.
Clutch-type (Rigid-type) {Imperial-type)
A
0-0.Smm
Check
1.0-1.smm 1.5-2.0mm
3) Put the flare nut on the pipe.
4) Flare the pipe.
5) Check that the flaring has been done correctly.
Tho"'"'''"""'"'""'
i
Tho
pip,
aod m,st ·'' "'"''
must be flaw-free.
flared in a per1ect circle.
1� :�: ::: i
i
���
t
-
he
ICII
REFRIGERANT PIPING
1) To prevent gas leakage, apply refrigeration oil to the inner surface of the flare.
2) Align the centres of both flares and tighten the flare nuts 3 or 4 turns by hand. Then tighten them fully with the torque
wrenches.
• Use torque wrenches when tightening the flare nuts to prevent damage to the flare nuts and escaping gas.
Flare nut
Valve cap
I
Service port cap
Piping size I tightening torque tightening torque tightening torque
32.7-39.9N • m
21.6-27.4N • m
0. D. 9.5mm
(333-407 kgf • cm)
(220-280 kgf • cm)
Gas side
0. D. 12.7mm
49.5-60.3N • m
48.1-59.7N • m
(505-615 kgf • cmJ
(490-61 O kgf • cm)
I
10.8-14.7N • m
0. D. 15.9mm
61.8-75.4N • m
(110-150 kgf • cm)
(630-770 kgf • cm)
14.2-17.2N • m
21.6-27.4N • m
Liquid side
I
O. D. 6.4mm
(144-175 kgf • cm)
(220-280 kgf • cm)
Cautions on Pipe Handling
Table No. 7
1) Protect the open end of the pipe against dust and moisture.
2) All pipe bends should be as gentle as possible. Use a pipe bender for
bending.
Selection of Copper and Heat Insulation materials
1!:
�
i:i
Brn�to
�
,a
R�in
place a cap .
II no flare cap is
�
available.cover
the flare mouth
with tape to keep
dirtor waterout �
When using commercial copper pipes and fittings, observe the following:
1) Insulation material : Polyethylene foam or equivalent.
Heat transfer rate - Co-efficient : 0.041 to 0.052W/m'K
( 0.035 to 0.045kcal/m'h'C)
. Im
2) Be sure to insulate both the gas and liquid piping and to provide insulation dimensions as below.
Piping
Minimum
size
bend radius Piping thickness
0.0.
30 mm or
9.5mm
more
Thickness, 0.6mm
Gas
0.0.
40 mm or
(C1220T-O)
side
12.7mm
more
0.D.
50 mm or
Thickness 0.8mm
15.9mm
more
(C1220T-O)
Liquid
0.0.
30 mm or
Thickness 0.6mm
side
6.4mm
more
(C1220T-O)
Thermal I
Thermal
,I
insulation
insulation size thickness
I.D
12-15mm
I.D
14-16mm
Thickness
I.D
min.6.5mm
16-20mm
I.D
8-10mm
Table No. 8
• Use separate thermal
insulation pipes for gas and
liquid refrigerant pipes.
Heatkisulllionri.>e�
'
�
��
Collll'AlnlcalonMI
oro�i-
�;.:=
Go,�
�
....
Thickness 0.6mm
(C1220T-O)