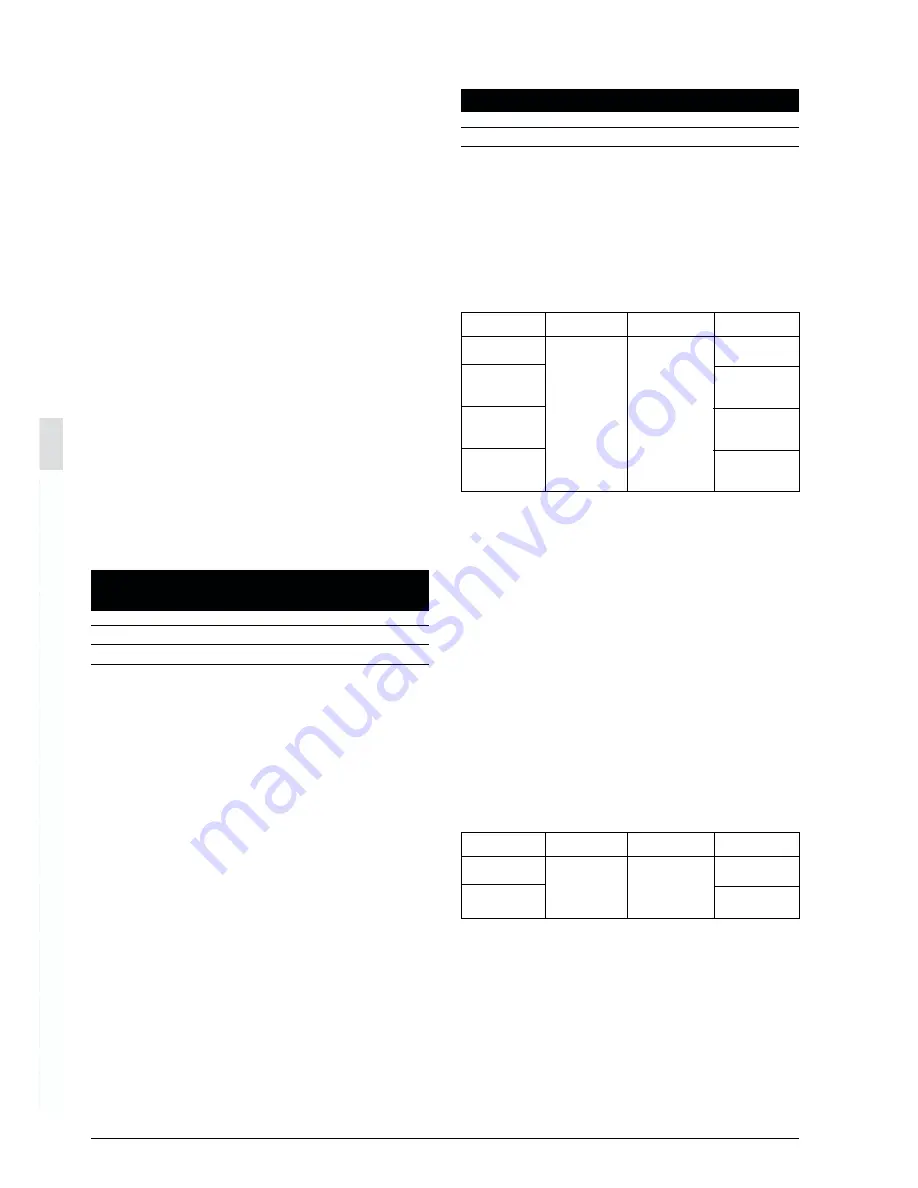
7
Setting
Pair system
(1 unit)
Simultaneous
operation system
(2-unit)
Simultaneous
operation system
(3-unit)
Simultaneous
operation system
(4-unit)
PRECAUTIONS
1. All transmission wiring except for the remote controller wires
is polarized and must match the terminal symbol.
2. In case of group control, perform the remote controller wiring
to the master unit when connecting to the simultaneous
operation system (wiring to the slave unit is unnecessary).
3. For group control remote controller, choose the remote
controller that suits the indoor unit which has the most
functions (as attached swing flap).
4. When controlling the simultaneous operation system with 2
remote controllers, connect it to the master unit (wiring to the
slave unit is unnecessary).
5. Be sure to connect the wiring to the master unit when
combining with a simultaneous operating multi-type in group
control.
6. Do not ground the equipment on gas pipes, water pipes,
lightning rods or crossground with telephones. Improper
grounding could result in electric shock.
FIELD SETTING
Field setting must be made from the remote controller in
accordance with the installation condition.
•
Setting can be made by changing the "Mode number", "FIRST
CODE No." and "SECOND CODE No.".
•
For setting and operation, refer to the "Field setting" in the
installation manual of the remote controller.
Setting ceiling height
•
Select the SECOND CODE No. that corresponds to the
ceiling height. (SECOND CODE No. is factory set to "01" for
a ceiling height of 2.7m or less.)
Ceiling height (m)
Mode n
°
1st code n
°
2nd code n
°
units 35~71
units 100~125
<2.7
<3.2
N
13 (23)
0
01
>2.7 or <3.0
<3.2 or <3.6
H
13 (23)
0
02
>3.0 or <3.5
<3.6 or 4.2
S
13 (23)
0
03
The figure of ceiling height is for air discharge in 4 directions.
Setting air discharge direction
•
For changing air discharge direction (2 or 3 directions), refer
to the option handbook of the optional blocking pad kit.
(SECOND CODE No. is factory set to "01" for air discharge in
4 directions.)
Setting when installing high performance filters
•
In case of installing high performance filters, refer to the
option handbook of the high performance filters.
Setting air filter sign
•
Remote controllers are equipped with liquid crystal air filter
signs to display the time to clean the air filter.
•
Change the SECOND CODE No. Depending on the amount
of dirt or dust in the room. (SECOND CODE No. is factory set
to "01" for air filter contamination-light)
Mode No.
11 (21)
FIRST CODE No.
0
SECOND CODE No.
01
02
03
04
Setting
Unified
setting
Individual
setting
Mode No.
11 (21)
FIRST CODE No.
1
SECOND CODE No.
01
02
Air Filter contamination
Setting
Display interval
Mode n
°
1st code n
°
2nd code n
°
Light
±
2500 hrs
10 (20)
0
01
Heavy
±
1250 hrs
10 (20)
0
02
•
When using wireless remote controllers it is necessary to use
address setting. Refer to the installation manual attached to
the wireless remote controller for the setting instructions.
Setting indoor unit number of simultaneous operation
system
•
When using in simultaneous operation system mode, change
the SECOND CODE No. as shown in the table. (SECOND
CODE No. is factory set to “01” for 1 connected unit.)
•
When using in simultaneous operation system mode, refer to
“Simultaneous Operation System Individual Setting” section to
set master and slave units separately.
When using wireless remote controllers
•
When using wireless remote controllers, wireless remote
controller address setting is necessary. Refer to the
installation manual attached to the wireless remote controller
for setting instructions.
Simultaneous operation system individual setting
It is easier if the optional remote controller is used when setting
the slave unit.
Perform the following procedures when setting the master and
slave unit separately.
Procedure (see figure 19)
1. Change the SECOND CODE No. to “02”, individual setting, so
that the slave unit can be individually set. (SECOND CODE
No. is factory set to “01”, unified setting.)
2. Perform field setting for the master unit.
3. Turn off the main power supply switch after (2).
4. Detach remote controller from the master unit and connect it
to the slave unit.
5. Turn on the main power supply switch again, and as in (1),
change the Position No. to “02”, individual setting.
6. Perform field setting for the slave unit.
7. Turn off the main power supply switch after (6).