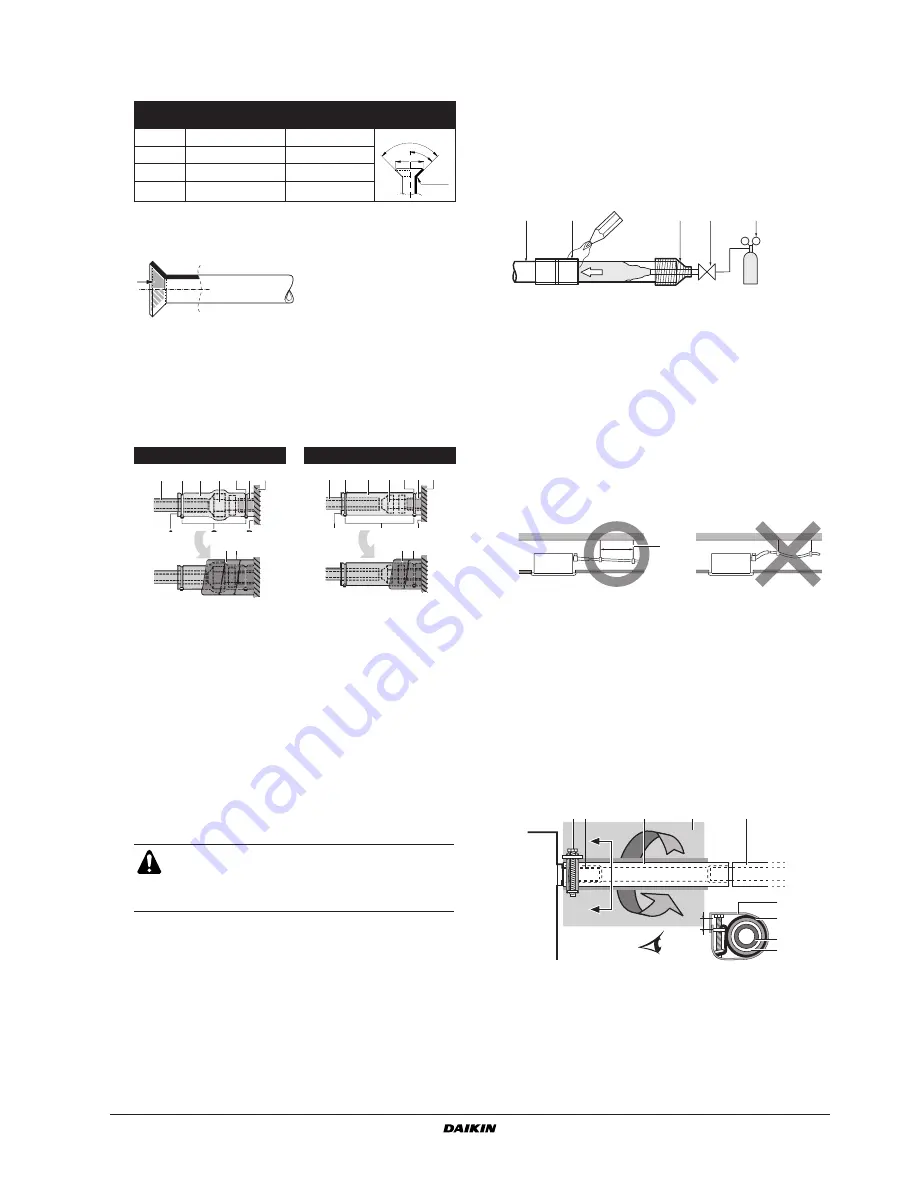
FDQ125C7VEB
Split System air conditioners
4PW71105-1 – 08.2011
Installation manual
4
■
Refer to
Table 1
for the dimensions of flare nut spaces and the
appropriate tightening torque. (Overtightening may damage the
flare and cause leaks.)
Table 1
■
When connecting the flare nut, coat the flare inner surface with
ether oil or ester oil and initially tighten 3 or 4 turns by hand
before tightening firmly.
■
If the refrigerant gas leaks during the work, ventilate the area. A
toxic gas is emitted by the refrigerant gas being exposed to a fire.
■
Make sure there is no refrigerant gas leak. A toxic gas may be
released by the refrigerant gas leaking indoor and being
exposed to flames from an area heater, cooking stove, etc.
■
Finally, insulate as shown in the figures below.
Piping insulation procedure
Cautions for brazing
■
Be sure to carry out a nitrogen blow when brazing.
Brazing without carrying out nitrogen replacement or releasing
nitrogen into the piping will create large quantities of oxidized
film on the inside of the pipes, adversely affecting valves and
compressors in the refrigerating system and preventing normal
operation.
■
When brazing while inserting nitrogen into the piping, nitrogen
must be set to 0.02 MPa with a pressure-reducing valve (=just
enough so that it can be felt on the skin).
D
RAIN
PIPING
WORK
Rig the drain piping as shown in the figure and take measures
against condensation. Improperly rigged piping could lead to leaks
and eventually wet furniture and belongings.
■
Install the drain pipes.
-
Keep piping as short as possible and slope it downwards at a
gradient of at least 1/100 so that air may not remain trapped
inside the pipe.
-
Keep pipe size equal to or greater than that of the connecting
pipe (vinyl pipe of 25 mm nominal diameter and 32 mm outer
diameter).
-
Push the supplied drain hose as far as possible over the
drain socket.
-
Tighten the metal clamp until the screw head is less than
4 mm from the metal clamp part as indicated in the
illustration.
-
Wrap the supplied large sealing pad over the metal clamp
and drain hose to insulate and fix it with clamps.
Pipe
gauge
Tightening torque
(N•m)
Flare dimension
A (mm)
Flare shape
Ø6.4
15~17
8.7~9.1
Ø9.5
33~39
12.8~13.2
Ø12.7
50~60
16.2~16.6
Ø15.9
63~75
19.3~19.7
Gas piping
Liquid piping
1
Piping insulation material (field supply)
2
Flare nut connection
3
Insulation for fitting (delivered with the unit)
4
Piping insulation material (main unit)
5
Main unit
6
Clamp (field supply)
7
Medium 1 sealing pad for gas piping (delivered with the unit)
Medium 2 sealing pad for liquid piping (delivered with the unit)
A
Turn seams up
B
Attach to base
C
Tighten the part other than the piping insulation material
D
Wrap over from the base of the unit to the top of the flare nut
connection
For local insulation, be sure to insulate local piping all
the way into the pipe connections inside the unit.
Exposed piping may cause condensation or may
cause burns when touched.
R0.4~0.8
45
° ±
2
90
°±
2
A
A
B
D
C
7
1
2
3
4
5
6
6
A
B
C
1
2
3
4
5
6
6
D
7
1
Refrigerant piping
2
Part to be brazed
3
Taping
4
Hands valve
5
Pressure-reducing valve
6
Nitrogen
1
Hanging bar
1
Drain socket (attached to the unit)
2
Drain hose (supplied with the unit)
3
Metal clamp (supplied with the unit)
4
Drain piping (field supply)
5
Large sealing pad (supplied with the unit)
1
2
3
4
5
6
6
1-1.5 m
1
1
2
3
5
≤
4 mm
3
5
2
A
A'
A'
A-A'
1
4
A
A'
Summary of Contents for FDQ125C7VEB
Page 1: ...INSTALLATION MANUAL FDQ125C7VEB Split System air conditioners ...
Page 13: ......
Page 14: ......