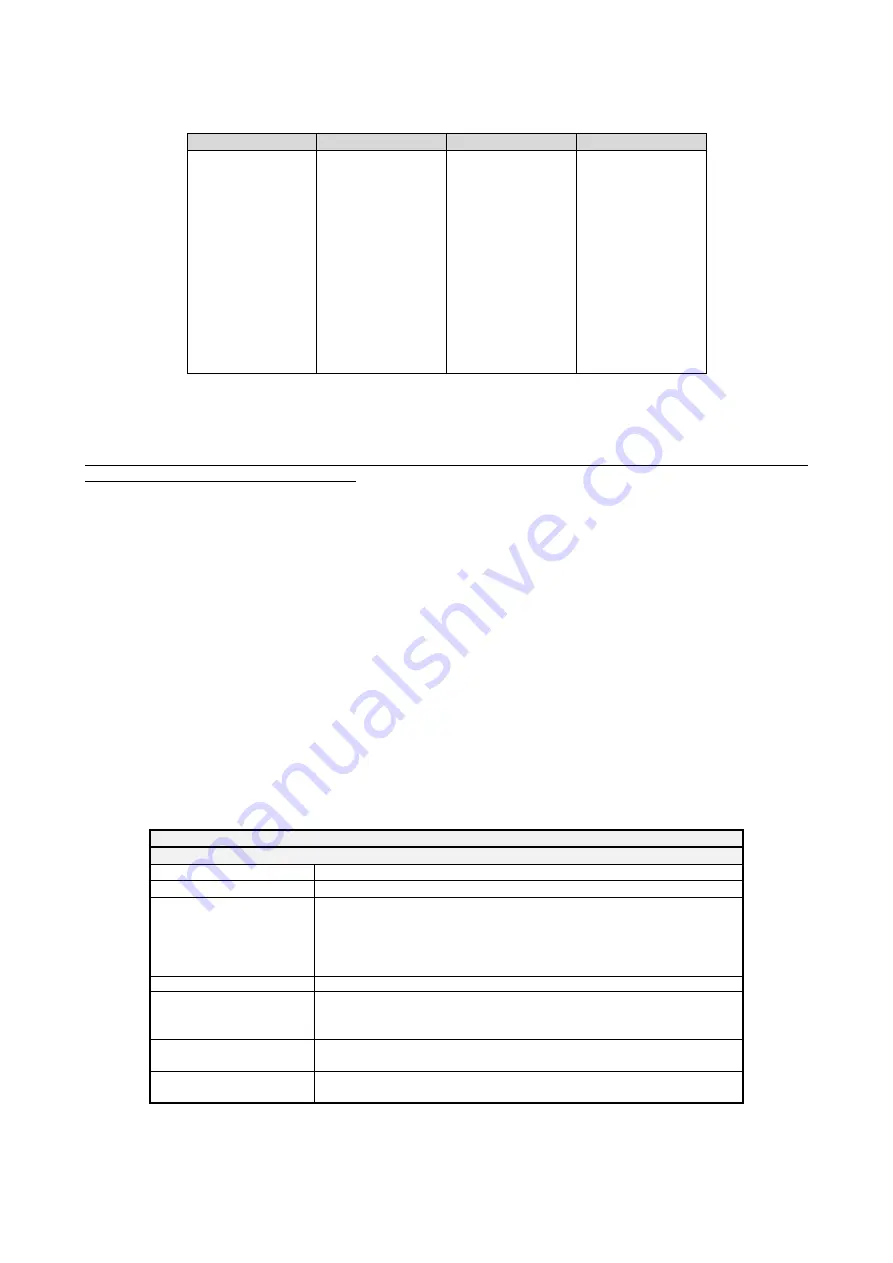
D-EIMHP01505-22_00EN 44/59
8.1. Pressure / temperature table
°C
Bar
°C
Bar
°C
Bar
°C
Bar
28
2.97
2
7.62
24
16.45
50
31.41
26
3.22
0
8.13
26
17.35
52
32.89
24
3.48
2
8.67
28
18.30
54
34.42
22
3.76
4
9.23
30
19.28
56
36.00
20
4.06
6
9.81
32
20.29
58
37.64
18
4.37
8
10.43
34
21.35
60
39.33
16
4.71
10
11.07
36
22.45
62
41.09
14
5.06
12
11.74
38
23.60
64
42.91
12
5.43
14
12.45
40
24.78
66
44.79
10
5.83
16
13.18
42
26.01
68
46.75
8
6.24
18
13.95
44
27.29
70
48.77
6
6.68
20
14.75
46
28.61
72
50.87
4
7.14
22
15.58
48
29.99
74
53.05
Table 18
– R32 Pressure/Temperature
8.2. Routine maintenance
This unit must be maintained by qualified technicians. Before beginning any work on the system, the personnel shall assure
that all security precautions have been taken.
Neglecting unit maintenance could degrade all parts of the units (coils, compressors, frames, pipes, etc.) with negative
effect on performances and functionality.
There are two different levels of maintenance, which can be chosen according to the type of application (critical/noncritical)
or to the installation environment (highly aggressive).
Examples of critical applications are process cooling, data centres, etc.
Highly Aggressive Environments can be defined as follows:
•
Industrial environment (with possible concentration of fumes result of combustion and chemical process).
•
Coastal environment.
•
Highly polluted urban environment.
•
Rural environment close to of animal excrement and fertilizers, and high concentration of exhaust gas from diesel
generators.
•
Desert areas with risk of sandstorms.
•
Combinations of the above.
Unit exposed to a highly aggressive environment can face corrosion in a shorter time than the ones installed on a standard
environment. Corrosion causes a rapid rusting of the frame core, consequently, decreases unit structure lifetime. To avoid
that, it is necessary to wash periodically the frame surfaces with water and suitable detergents.
In case of part of unit frame paint came off, it is important to stop its progressive deterioration by repainting the exposed
parts using proper products. Please contact factory to get the required products specifications.
In case of just salt deposits are present, it is enough to rinse the parts with fresh water.
Checklist for yearly maintenance of the indoor unit
Indoor Unit: Yearly maintenance plan
Element
Description
Water pressure
Water filter
Water pressure relief
valve
Turn the red knob on the valve counterclockwise and check if it
operates correctly: If you do not hear a clacking sound, contact your
local dealer. In case the water keeps running out of the unit, close both
the water inlet and outlet shut-off valves first and then contact your local
dealer.
Water pressure
Keep water pressure above 1 bar. If lower, add water.
Water filter
Clean the water filter.
NOTICE:
handle the water filter with care.
DO
NOT
use excessive force when you reinsert the water filter so as
NOT
to damage the water filter mesh.
Pressure relief valve
hose
Check the condition and routing of the hose. Water must drain
appropriately from the hose.
Switch box
Carry out a thorough visual inspection of the switch box and look for
obvious defects such as loose connections or defective wiring.
Table 19
– Yearly maintenance checklist for the indoor unit