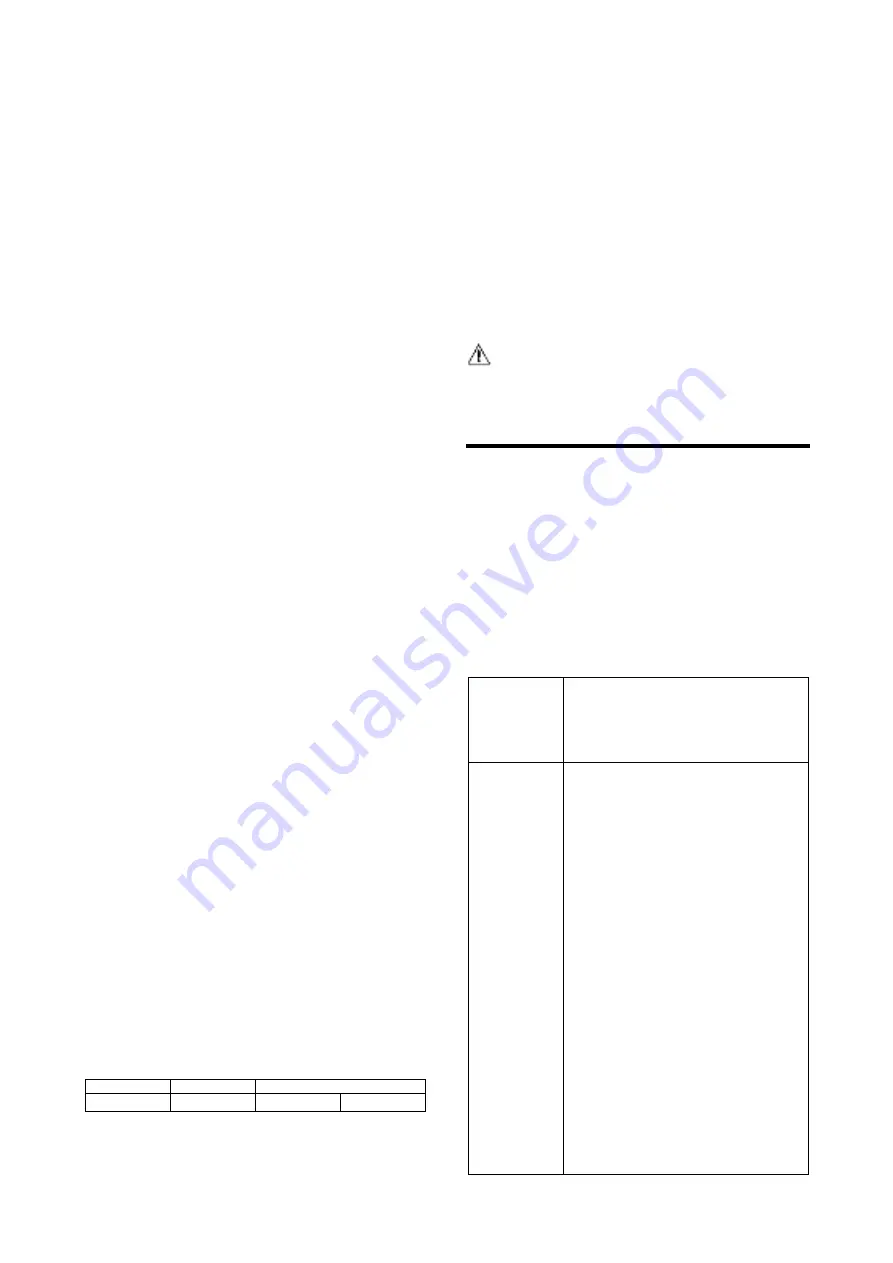
D - EIMWC01008-06_02EU - 11/182
•
Machinery rooms shall have doors opening outward and
sufficient in number to ensure freedom for persons to
escape in an emergency; the doors shall be tight fitting,
self-closing and so designed that they can be opened
from inside (antipanic system).
•
Special machinery rooms where the refrigerant charge is
above the practical limit for the volume of the room shall
have a door that either opens directly to the outside air or
through a dedicated vestibule equipped with self-closing,
tight-fitting doors.
•
The ventilation of machinery rooms shall be sufficient
both for normal operating conditions and emergencies.
•
Ventilation for normal operating conditions shall be in
accordance with national regulations.
•
The emergency mechanical ventilation system shall be
activated by a detector(s), located in the machinery room.
•
This ventilation system shall be:
•
independent of any other ventilation system on
the site.
•
provided with two independent emergency
controls one located outside the machinery
room, and the other inside.
•
The emergency exhaust ventilation fan shall:
•
Be either in the air flow with the motor outside
the airflow or rated for hazardous areas
(according to the assessment).
•
Be located to avoid pressurization of the
exhaust ductwork in the machinery room.
•
Not cause sparks to occur if it contacts the duct
material.
•
Airflow of the emergency mechanical ventilation
shall be at least
𝑉 = 0,014 × 𝑚
2
3
⁄
where
V
is the air flow rate in m
3
/s;
m
is the mass of refrigerant charge, in kg, in the
refrigerating system with the largest charge,
any part of which is located in the machinery
room;
0,014
is a conversion factor.
•
Mechanical ventilation shall be operated
continuously or shall be switched on by the
detector.
•
Detector shall automatically activate an alarm, start
mechanical ventilation, and stop the system when it
triggers.
•
The location of detectors shall be chosen in relation to the
refrigerant and they shall be located where the refrigerant
from the leak will concentrate.
•
The positioning of the detector shall be done with due
consideration of local airflow patterns, accounting for
location sources of ventilation and louvers. Consideration
shall also be given to the possibility of mechanical
damage or contamination.
•
At least one detector shall be installed in each machinery
room or the occupied space being considered and/or at
the lowest underground room for refrigerants heavier than
air and at the highest point for refrigerants lighter than air.
•
Detectors shall be continuously monitored for functioning.
In the case of a detector failure, the emergency sequence
should be activated as if refrigerant had been detected.
•
The pre-set value for the refrigerant detector at 30 °C or
0 °C, whichever is more critical, shall be set to 25 % of
the LFL. The detector shall continue to activate at higher
concentrations.
Refrigerant
LFL
Pre-set alarm
R1234ze
0,303 kg/m
3
0,07575 kg/m
3
16500 ppm
•
All electrical equipment (not only the refrigerating system)
shall be selected to be suitable for use in the zones
identified in the risk assessment. Electrical equipment
shall be deemed to comply with the requirements if the
electrical supply is isolated when the refrigerant
concentration reaches 25 % of the lower flammable limit
or less.
•
Machinery rooms or special machinery rooms shall be
clearly marked as such on the entrances to the room,
together with warning notices indicating that unauthorized
persons shall not enter and that smoking, naked light or
flames are prohibited. The notices shall also state that, in
the event of an emergency, only authorized persons
conversant with emergency procedures shall decide
whether to enter the machinery room. Additionally,
warning notices shall be displayed prohibiting
unauthorized operation of the system.
•
The owner / operator shall keep an updated logbook of
the refrigerating system.
The optional leak detector supplied by DAE with the
chiller should be used exclusively to check
refrigerant leakage from the chiller itself.
9. MAINTENANCE
9.1. Routine maintenance for R1234ze
Personnel working on the electrical or the refrigeration
components must be authorized, trained, and fully qualified.
Maintenance and repair requiring the assistance of other skilled
personnel should be carried out under the supervision of the
person competent in the use of flammable refrigerants. Any
person conducting servicing or maintenance on a system or
associated parts of the equipment should be competent
according to EN 13313.
Persons working on refrigerating systems with flammable
refrigerants should have competence in safety aspects of
flammable refrigerant handling supported by evidence of
appropriate training.
electrical
components
Never work on any electrical components, until the
general supply to the unit has been cut using the
disconnect switch(es) in the control box. The
frequency variators used are equipped with
capacitor batteries with a discharge time of 20
minutes; after disconnecting power wait 20
minutes before opening the control box.
refrigerating
system
The following precautions should be taken before
working on the refrigerant circuit:
— obtain permit for hot work (if required);
— ensure that no flammable materials are
stored in the work area and that no ignition
sources are present anywhere in the work
area;
— ensure that suitable fire extinguishing
equipment is available;
— ensure that the work area is
properly
ventilated
before working on the refrigerant
circuit or before welding, brazing or soldering
work;
— ensure that the leak detection equipment
being used is non-sparking, adequately
sealed or intrinsically safe;
— ensure that all maintenance staff have
been instructed.
The following procedure should be followed
before working on the refrigerant circuit:
1. remove refrigerant (specify the residual
pressure);
2. purge circuit with
inert gas
(e.g.,
nitrogen);
3. evacuate to a pressure of 0,3 (abs.) bar
(or 0,03 MPa);
4. purge again with
inert gas
(e.g.,
nitrogen);
5. open the circuit.
The area should be checked with an appropriate
refrigerant detector prior to and during any hot
work to make the technician aware of a potentially
flammable atmosphere.