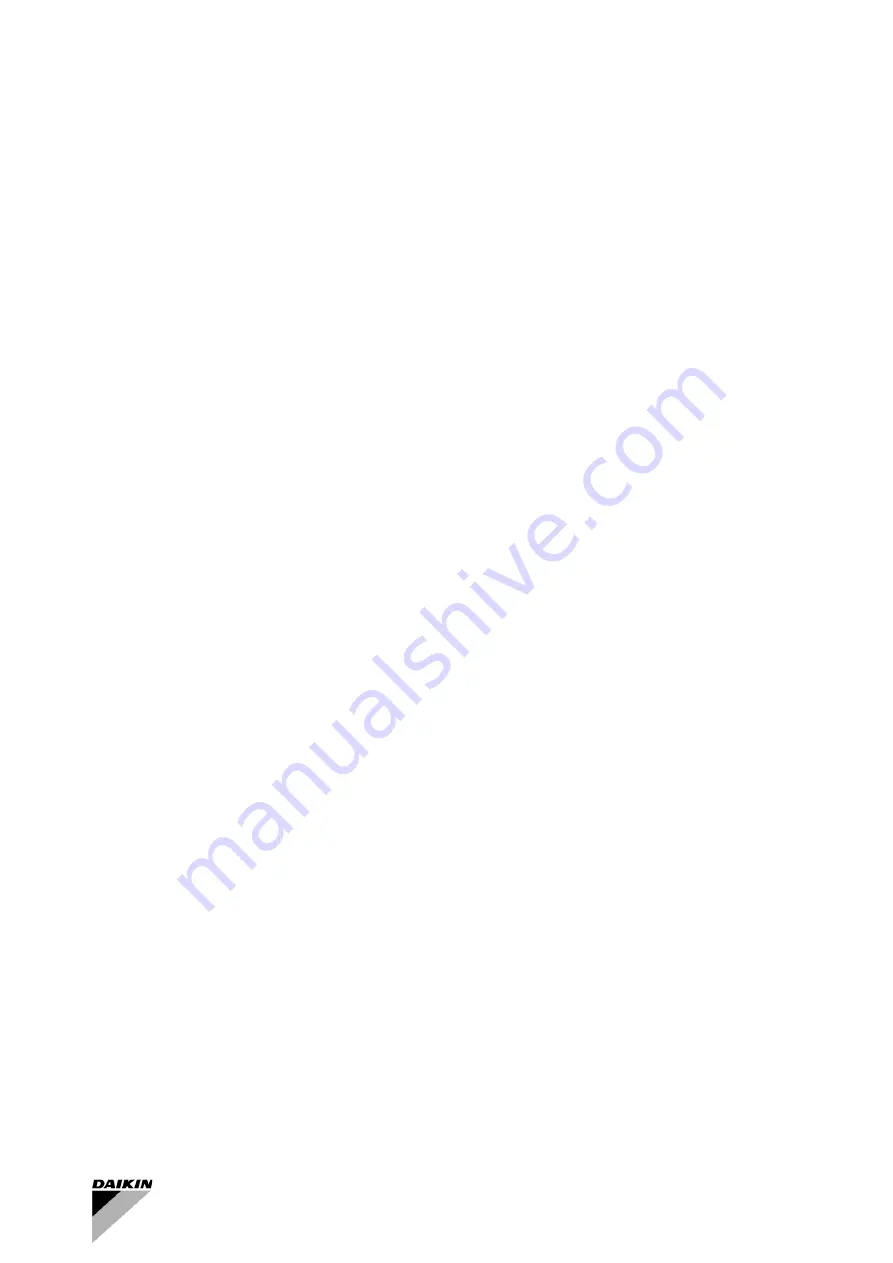
D - KIMAC00512-09EN - 32/40
moisture indicator in the sight-glass indicates excess moisture by the wet system colour indicators. During the first
few months of operation the filter-drier replacement may be necessary if you have bubbles in liquid line as
explained before. Any residual particles from the unit working process, compressor and miscellaneous
components are swept by the refrigerant into the liquid line and are caught by the filter-drier.
To change the filter drier, close the manual liquid line shutoff valve, pump the unit down by opening the switches
Q1, Q2 (ON/OFF switches compressors) in “off” position.
Move the ON/OFF switch unit Q0 to the “off” position.
Close the suction line valve. Remove and replace the filter-drier. Evacuate the liquid line through the manual
shutoff valve removing non-condensable that may have entered during filter replacement.
Open the suction line valve; open the manual liquid line of shutoff valve. A leak check is recommended before
returning the unit to operation.
Electronic expansion valve
These air-cooled chiller are equipped with the most advanced electronic expansion valve to achieve precise
control of refrigerant mass flow. As today’s system requires improved energy efficiency, tighter temperature
control, wider range of operating conditions and incorporate features like remote monitoring and diagnostics, the
application of electronic expansion valves becomes mandatory. The electronic expansion valve proposes features
that makes it unique: short opening and closing time, high resolution, positive shut-off function to eliminate use of
additional solenoid valve, highly linear flow capacity, continuous modulation of mass flow without stress in the
refrigerant circuit and corrosion resistance stainless steel body.
Evaporator
The units are supplied with optimised counter-flow evaporator, single refrigerant pass. It is direct expansion with
refrigerant inside the tubes and water outside (shell side) with carbon steel tube sheets, with straight copper tubes
that are spirally wound internally for higher efficiencies, expanded on the tube plates. The external shell, is linked
with an electrical heater to prevent freezing to -28 C ambient temperature, energised by a thermostat and is
covered with a closed cell insulation material. Each evaporator has 2 or 3 refrigerant circuits one for each
compressor. Each evaporator is manufactured in accordance to PED approval. Normally no service work is
required on the evaporator.
Heat Recovery Condensers
Condensers are shell and clearable, through-tube types. Standard configuration is 2 passes. The unit has
independent exchangers, one per circuit completely assembled. Each heat recovery condenser has a carbon steel
and seamless, integrally finned high efficiency copper tubes, roll expanded into heavy carbon steel tube sheets.
Water heads are removable and include vent and drain plugs. Condensers are equipped spring loaded relief
valves.
Condenser is designed to comply with PED. Waterside working pressure is designed for 10.5 bar. Standard
configuration on water connection side is 2 passes.
The installer has to supply the water header connection for all heat recovery condensers installed on the unit, both
at the entering and leaving water connections and provide the flow switch. All the heat recovery condenser must
be connected together in parallel. At the entering water pipe, must be installed the temperature sensor, supplied
spare with the unit, to control the heat recovery cycle.
Condenser coil fans
The condenser fans are helical types with wing-profile blades to achieve a better performance. The direct coupling
with the electrical motor reducing vibrations caused by the functioning. The three-phase type motors are supplied
as standard with IP54 protection (Insulation class F); they are protected against overloading and short circuits by
circuit breakers located inside the electrical control panel.
Air-cooled condenser (Condensing coil)
The condensing coils are constructed with internally enhanced seamless copper tubes arranged in a staggered
row pattern and mechanically expanded into DAIKIN lanced and rippled aluminum condenser fins with full fin
collars. An integral sub-cooler circuit provides sub-cooling to effectively eliminate liquid flashing and increases in
cooling capacity without increasing the power input.
No maintenance is ordinary required except the occasional removal of dirt and debris from the outside surface of
the fins. DAIKIN recommends the use of foaming coil cleaners available at air conditioning supply outlets. Use
caution when selecting such cleaners as some may contain potentially harmful chemical. Care should be taken not
to damage the fins during cleaning.
Lubricating oils
Summary of Contents for EWAP 800-C18AJYNN
Page 1: ...D KIMAC00512 09EN 1 40 ...