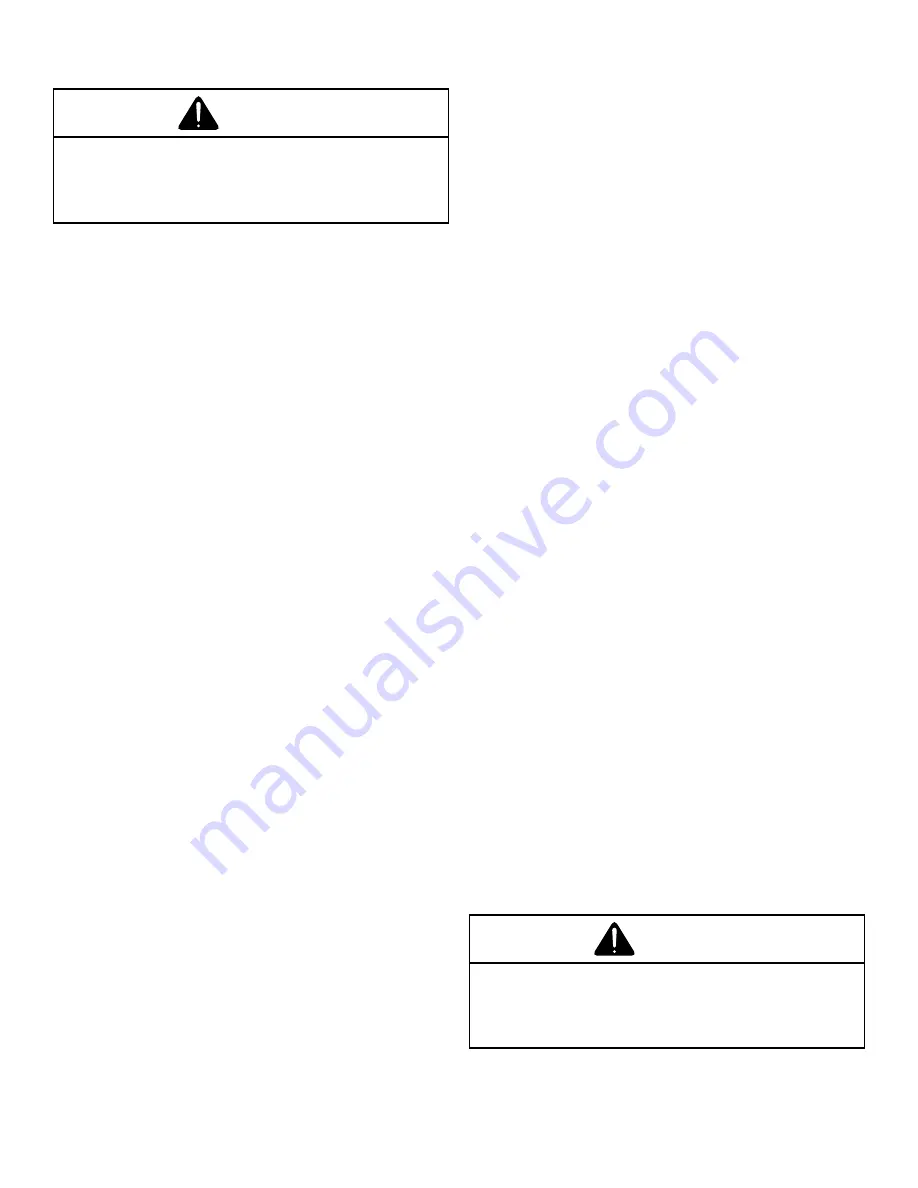
4
UNIT LOCATION
WARNING
To prevent possible equipment damage, property
damage, personal injury or death, the following
bullet points must be observed when installing
the unit.
IMPORTANT NOTE: Remove wood shipping rails
prior to installation of the unit.
All Installations:
Important Note:
Unit should be energized 24
hours prior to compressor start up to ensure
crankcase heater has sufficiently warmed the
compressors. Compressor damage may occur if
this step is not followed.
NOTE: Appliance is shipped from factory for
vertical duct application.
Proper installation of the unit ensures trouble-free
operation. Improper installation can result in problems
ranging from noisy operation to property or equipment
damages, dangerous conditions that could result in injury
or personal property damage and that are not covered by
the warranty. Give this booklet to the user and explain it’s
provisions. The user should retain these instructions for
future reference.
•
To avoid possible illness or death of the building
occupants, do NOT locate outside air intake device
(economizer, manual fresh air intake, motorized
fresh air intake) too close to an exhaust outlet, gas
vent termination, or plumbing vent outlet. For specific
distances required, consult local codes.
•
Allow minimum clearances from the enclosure for
fire protection, proper operation, and service access
(see unit clearances). These clearances must be
permanently maintained.
•
When the unit is heating, the temperature of the return
air entering the unit must be a minimum of 55° F.
Ground Level Installations Only:
•
When the unit is installed on the ground adjacent
to the building, a level concrete (or equal) base is
recommended. Prepare a base that is 3” larger than
the package unit footprint and a minimum of 3” thick.
•
The base should also be located where no runoff of
water from higher ground can collect in the unit.
Roof top Installations Only:
•
To avoid possible property damage or personal
injury, the roof must have sufficient structural
strength to carry the weight of the unit(s) and snow
or water loads as required by local codes. Consult
a structural engineer to determine the weight
capabilities of the roof.
•
The unit may be installed directly on wood floors
or on Class A, Class B, or Class C roof covering
material.
•
To avoid possible personal injury, a safe, flat surface
for service personnel should be provided.
•
Adequate clearances from the unit to any adjacent
public walkways, adjacent buildings, building
openings or openable windows must be maintained
in accordance with National Codes.
Unit Precautions
•
Do not stand or walk on the unit.
•
Do not drill holes anywhere in panels or in the base
frame of the unit except where indicated. Unit access
panels provide structural support.
•
Do not remove any access panels until unit has been
installed on roof curb or field supplied structure.
•
Do not roll unit across finished roof without prior
approval of owner or architect.
• Do not skid or slide on any surface as this may
damage unit base. The unit must be stored on a flat,
level surface. Protect the condenser coil because it
is easily damaged.
Roof Curb Installations Only:
Curb installations must comply with local codes and should
be done in accordance with the established guidelines of
the National Roofing Contractors Association.
Proper unit installation requires that the roof curb be firmly
and permanently attached to the roof structure. Check for
adequate fastening method prior to setting the unit on the
curb.
Full perimeter roof curbs are available from the factory
and are shipped unassembled. Field assembly, squaring,
leveling and mounting on the roof structure are the
responsibility of the installing contractor. All required
hardware necessary for the assembly of the sheet metal
curb is included in the curb accessory.
WARNING
To prevent possible equipment damage, property
damage, personal injury or death, the following
bullet points must be observed when installing
the unit.