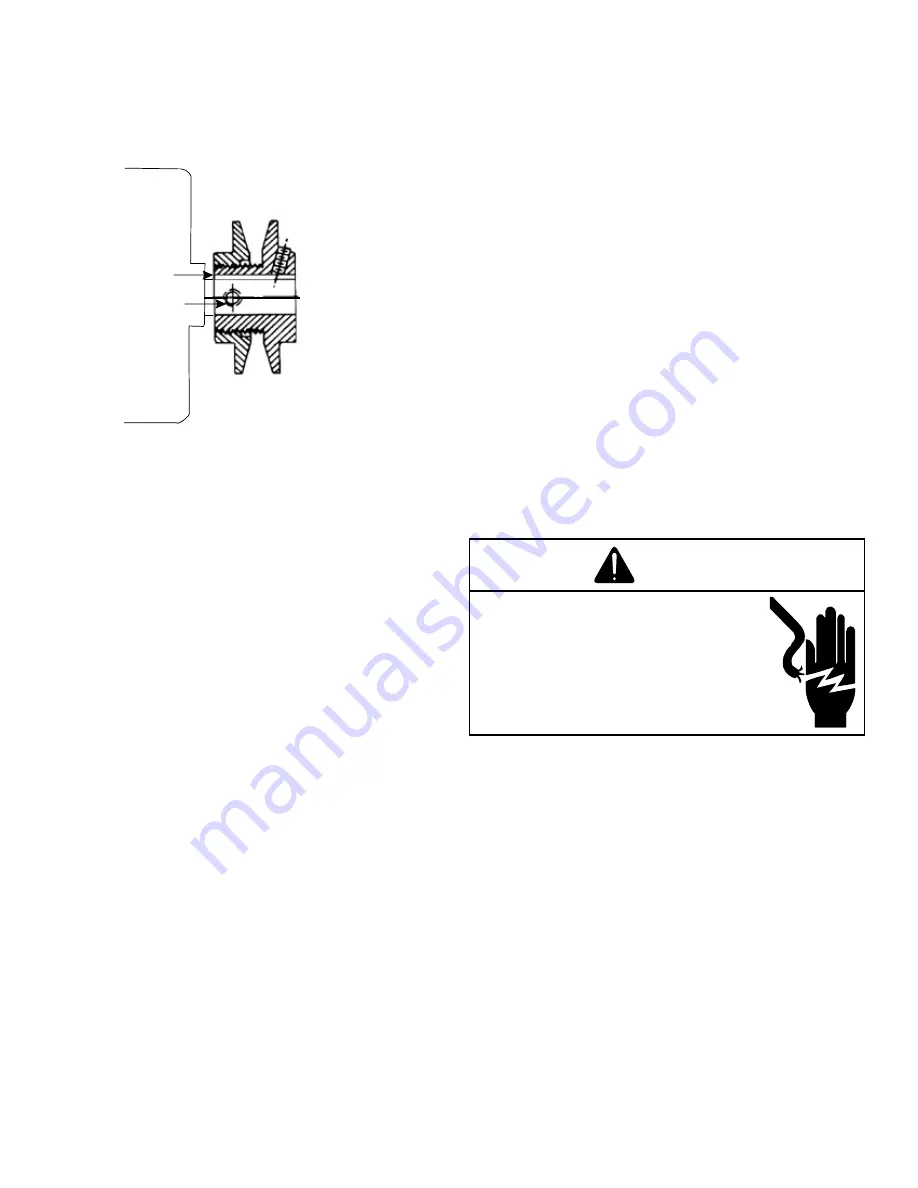
12
before starting drive. Recheck set screws and belt
tension after 24 hours service.
NOTE:
Future adjustments should be made by loosening
the belt tension and increasing or decreasing the pitch
diameter of the sheave by half or full turns as required.
Readjust belt tension before starting drive.
C
B
VL & VM
NOTE:
Do NOT operate sheave with flange projecting
beyond the hub end.
Refrigeration System Checks
This unit is equipped with thermal expansion valves.
Ensure
the hold-down bolts on the compressor are secure and
have not vibrated loose during shipment. Check that the
vibration grommets have been installed and visually check
all piping for damage and leaks and repair if necessary. The
entire system has been factory charged and tested, making
it unnecessary to field charge. Factory refrigerant charge is
shown on the unit’s nameplate.
To confirm charge levels or, if a leak occurs and charge needs
to be added to the system, it is recommended to evacuate
the system and recharge refrigerant to the unit’s nameplate
specifications. This unit has been rated in the cooling mode at the
AHRI rated conditions of: indoor (80°F db/67°F wb) and outdoor
(95°F db). While operating at this condition, the superheat should
range from 9°F to 11°F for each refrigeration circuit measured at
the suction service port located near the compressor.
Start-Up Procedure and Checklist
Begin with power turned off at all disconnects.
Air Conditioning Start-Up Procedure
1. Ensure the thermostat is set to OFF and Fan is set
to Auto.
2.
Inspect all registers and set them to the normal open
position.
3. Turn on the electrical supply at the disconnect.
4. Turn the fan switch to the “ON” position. The blower
should operate after a 7 second delay.
5. Turn the fan switch to “Auto” position. The blower
should stop after a 60 second delay.
6. Set the thermostat to Cool mode and slowly
lower the cooling temperature until the unit starts.
The compressor, blower and fan should now be
operating. Allow the unit to run 10 minutes, make
sure cool air is being supplied by the unit.
7. Check that the compressor is operating correctly.
The scroll compressors in these units MUST operate
in the proper rotation. To ensure the compressors
are operating in the correct direction, check the
compressor discharge line pressure or temperature
after the compressor is started. The discharge
pressure and discharge line temperature should
increase. If this does not occur and the compressor
is producing an exceptional amount of noise,this
indicates that there is a phasing issue.
Perform the following to correct:
7.1 Turn power to the unit OFF.
7.2 Switch any two leads of power supply at unit
Single Point Power Block.
7.3 Turn power to the unit ON.
7.4 Perform step 7 again.
8. Turn the temperature setting to the highest position,
stopping the unit. The indoor blower will continue to
run for 60 seconds.
9. Turn the thermostat system switch to “OFF” and
disconnect all power when servicing the unit.
NOTE: The compressor has 180 second re-start
delay on timer to avoid short cycling.
WARNING
HIGH VOLTAGE!
Disconnect all power before
servicing or installing this unit.
Multiple power sources may be
present. Failure to do so may cause
property damage, personal injury or
death.
Heat Pump Start-Up Procedure
10.
Check the cooling mode for the heat pump in the
same manner as above. The reversing valve is
energized when the thermostat is placed in the
cooling position. A clicking sound should be noticeable
from the reversing valve. By lowering the temperature
setting to call for cooling, the solenoid valve is
energized. The compressor, blower and fan should
then be running. After the cooling mode is checked
out, turn the thermostat system switch to “OFF”.
11. Turn the thermostat system switch to “HEAT” and fan
switch to “AUTO”.
12. Slowly raise the heating temperature setting. When
the heating first stage makes contact, stop raising the
temperature setting.. The compressor, blower and fan
should now be running with the reversing valve in the
deenergized (heating) position. After giving the unit time
to settle out, make sure the unit is supplying heated air.
Note: If the outdoor ambient is above 80°F, the unit
may trip on its high pressure cut out when on heating.
The compressor should stop. The heating cycle
must be thoroughly checked, so postpone the test to