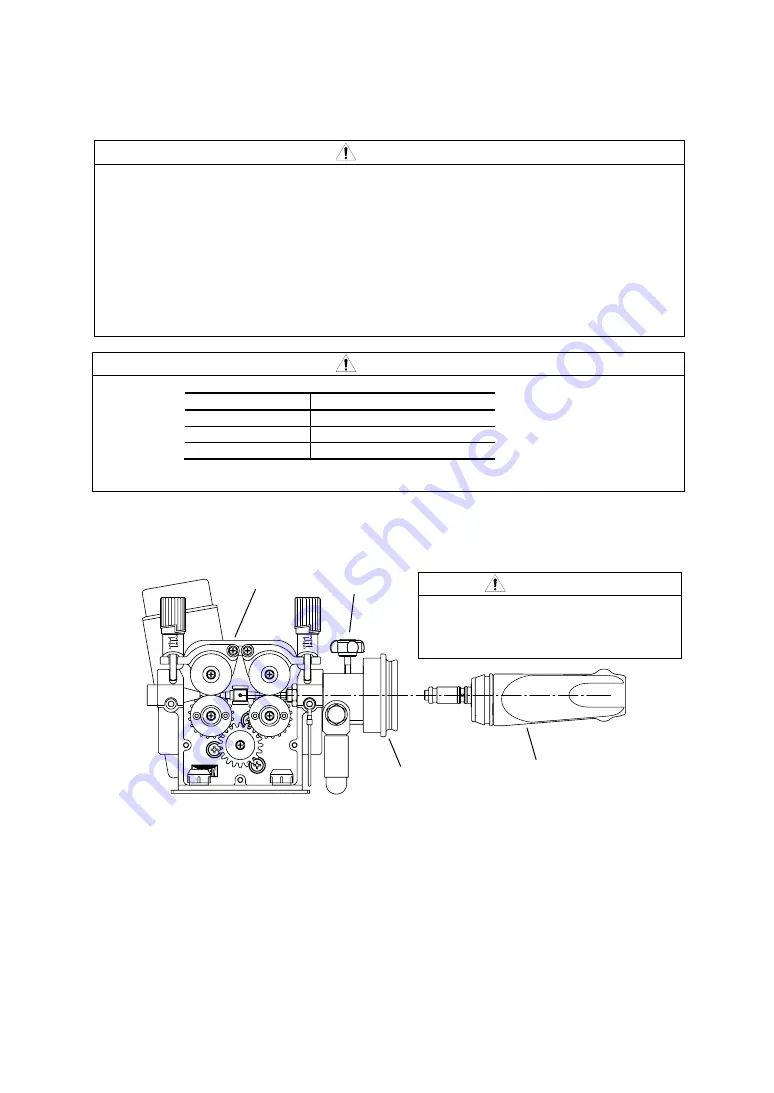
―12―
Welding torch
“WT
●●●●
-S(M)(L)UT” series
Wire feeder
Torch adapter
Fixing bolt
6. CONNECTION PROCEDURE (continued)
6.2 Connection of the Torch Cable
WARNING
∗
Touching the charging parts may result in fatal electric shock and severe burns.
●
Do not touch the charging parts of the welding machine.
●
Have a qualified electric engineer ground the case of the welding power source and the
base metal or jig electrically connected in accordance with a local low.
●
Disconnect the welding power source by turning off the line disconnect switch in the
power box to avoid an electric shock before the welding power source or base metal and
connecting the cables or hoses.
●
After connecting the cables, cover the power source with the cover or case.
●
When using the welding machine in such a humid environment as construction site, on the
steel plate, or on steel structure, install a leakage breaker.
CAUTION
●
Use the proper torch cable that matches the welding current.
Welding current
Cable thickness
200 A
AWG 1 [38mm
2
] or more
350 A
AWG 0 [60mm
2
] or more
500 A
AWG 3/0 [80mm
2
] or more
* When performing pulse welding using a 56ft [17m] or more cable, use the thicker cable by
one rank.
6.3 Connection of the welding torch
Welding torch is connected with the part torch adapter of Wire feeder, fixing bolt is tightened, and
welding torch is fixed.
[Note] This product can connect following welding torch by the standard.
OTC CO
2
/MAG Welding torch
“WT3510- S(M)(L)UT” series, “WT4000- S(M)(L)UT” series
When following welding torch is connected, it is necessary to prepare option parts and option kit
separately.
OTC CO
2
/MAG Welding torch
“WT5000- S(M)(L)UT” series
OTC MIG Welding torch
“WTA200-SUT, “WTA300-SUT”, “WTAW400-SUT”
CAUTION
●
Please tighten fixing bolt surely to fix
Torch.
Otherwise, it causes the electric shock
and a fire by feeding power the defect.
-
12
-