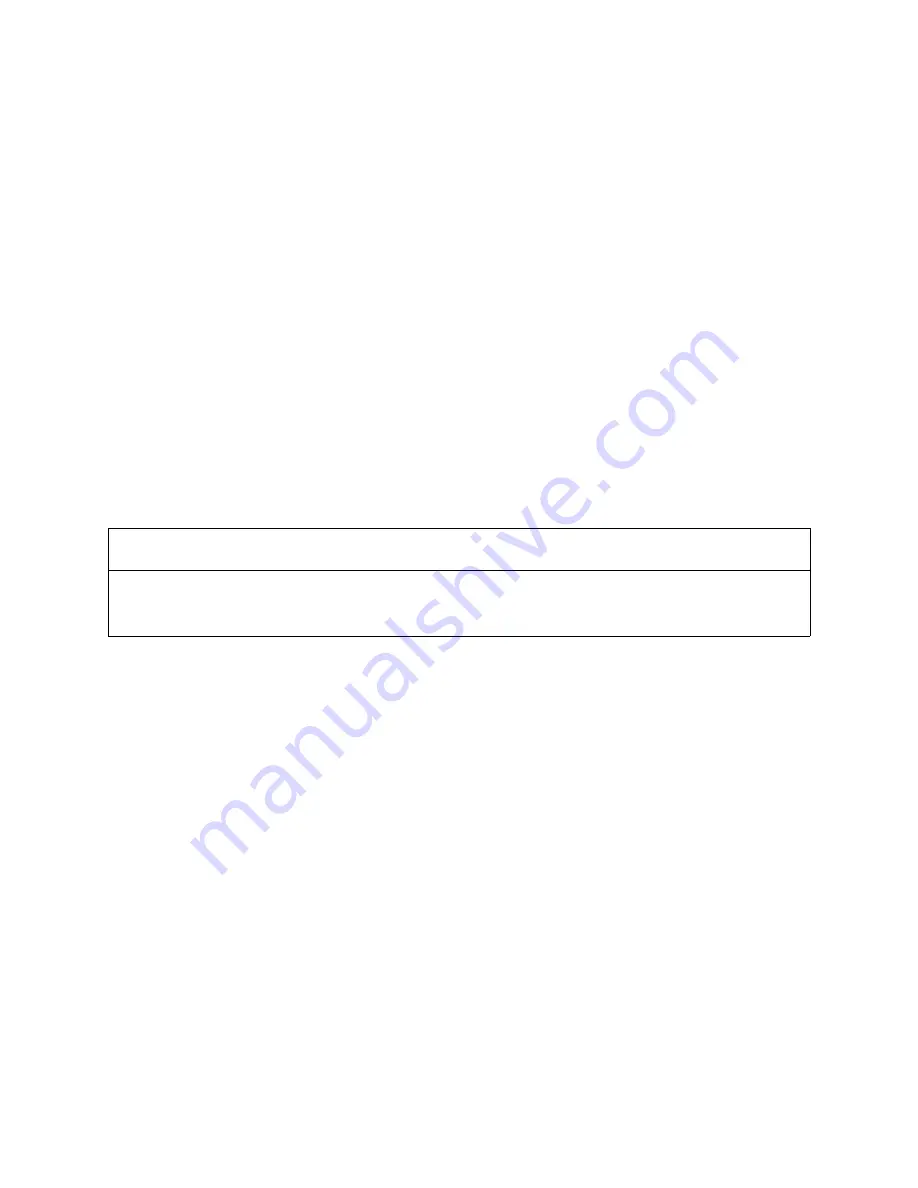
S0302000
Page 6
General Maintenance Procedures
Return to Master Table of Contents
HYDRAULIC SYSTEM CLEANLINESS AND OIL LEAKS
MAINTENANCE PRECAUTIONS FOR HYDRAULIC SYSTEM SERVICE
Whenever maintenance, repairs or any other type of troubleshooting or service is being performed, it’s
important to remember that the hydraulic system - including both the interior and exterior surfaces of
assemblies, and every drop of operating fluid - must be protected from contamination.
Dust and other foreign contaminants are major contributors to premature wear in hydraulic circuits. The
narrow tolerances, rapidly moving parts and high operating pressures of the system require that fluid be
kept as clean as possible. The performance and dependability of the machine (and the service lift of
individual components) can be noticeably reduced if proper precautions are not observed:
•
Use a safe, non-combustible, evaporative-type, low-residue solvent and thoroughly clean
exterior surfaces of assemblies before any part of the circuit is opened up or disassembled.
NOTE:
It’s just as important to clean the cap and reservoir top before routine fluid changes or
quick checks as it is before major repairs. (Accumulated dirt attracts moisture, oil and
other fluids - and more dirt.)
•
Keep dismantled parts covered during disassembly. Use clean caps, plugs or tape to protect the
disconnected openings of flanges, manifolds and piping.
•
Do not allow cleaning solvents or other fluids to mix with the oil in the system. Use clean oil to
flush any traces of solvent or other residue before reassembly.
•
If metal or rubber fragments are found in the system, flush and replace all fluid in the system
and troubleshoot the circuit to identify the source of contamination.
OIL LEAKAGE PRECAUTIONS
Oil that is visibly seeping from joints or seals should always serve as a "red flag" alarm.
Leaks must alert the machine operator and maintenance crew that air, water and dirt have an open, free
passageway through which to enter the circuit. Harsh, corrosive salt air, freezing and thawing
condensation cycles and working environments that are full of fine dust are especially hazardous. Clogging
of valve spools or external piping (especially pilot circuit piping) can gradually diminish or very suddenly
put a complete stop to normal hydraulic function. You can prevent having to make these types of repairs by
following recommended assembly procedures:
1.
Use new O-rings and oil seals whenever hydraulic assemblies are rebuilt.
2.
Prepare joint surfaces before assembly by checking alignment and flatness. Clean and repair
corrosion or any other damage.
3.
Follow bolt torque recommendations and all other assembly requirements.
IMPORTANT
Make sure that cleaning solvents will be compatible with rubber materials used in the hydraulic
system. Many petroleum based compounds can cause swelling, softening, or other deterioration
of system sealing elements, such as O-rings, caps and other seals.
Summary of Contents for Solar 340LC-V
Page 2: ......
Page 4: ......
Page 7: ...1SAFETY...
Page 8: ......
Page 46: ...S0102000 Page 38 Track Excavator Safety...
Page 47: ...1SPECIFICATIONS...
Page 48: ......
Page 52: ...S0202110K Page 4 Specifications for Solar 340LC V COMPONENT LOCATIONS Figure 1...
Page 54: ...S0202110K Page 6 Specifications for Solar 340LC V...
Page 70: ...S0202110K Page 22 Specifications for Solar 340LC V...
Page 71: ...1GENERAL MAINTENANCE...
Page 72: ......
Page 86: ...S0302000 Page 14 General Maintenance Procedures Return to Master Table of Contents...
Page 99: ...1UPPER STRUCTURE...
Page 100: ......
Page 102: ...S0402040K Page 2 Cab TABLE OF CONTENTS Removal 3 Installation 6...
Page 116: ...S0403050K Page 8 Counterweight Return to Master Table of Contents...
Page 140: ...S0407000 Page 6 Swing Bearing...
Page 144: ...S0408030 Page 4 Swing Reduction Gearbox Return to Master Table of Contents PARTS LIST Figure 1...
Page 159: ...1LOWER STRUCTURE AND CHASSIS...
Page 160: ......
Page 184: ...S0505000 Page 24 Track Assembly 7 Tighten plug 1 Figure 48 Figure 48...
Page 185: ...S0505000 Page 25 Track Assembly TRACK SPRING AND TRACK ADJUSTING CYLINDER PARTS LIST Figure 49...
Page 187: ...1ENGINE AND DRIVE TRAIN...
Page 188: ......
Page 199: ...S0605060K Page 11 Air Conditioner Face and Defroster ARS1300L Figure 12...
Page 214: ...S0605060K Page 26 Air Conditioner...
Page 223: ...1HYDRAULICS...
Page 224: ......
Page 254: ...S0702180K Page 30 Hydraulic System Troubleshooting Testing and Adjustment...
Page 256: ...S0703010K Page 2 Accumulator TABLE OF CONTENTS General Description 3 Specifications 4...
Page 260: ...S0703010K Page 6 Accumulator...
Page 268: ...S0704030 Page 8 Center Joint Swivel...
Page 277: ...S0705000 Page 9 Cylinders...
Page 281: ...S0705000 Page 13 Cylinders...
Page 285: ...S0705000 Page 17 Cylinders...
Page 293: ...S0705000 Page 25 Cylinders...
Page 302: ...S0705000 Page 34 Cylinders 17 Force out pin bushing 1 from body of cylinder Figure 28...
Page 306: ...S0705000 Page 38 Cylinders...
Page 316: ...S0707280 Page 10 Swing Motor Return to Master Table of Contents Figure 6...
Page 339: ...S0707345K Page 11 Travel Motor with Gearbox...
Page 340: ...S0707345K Page 12 Travel Motor with Gearbox PARTS LIST Hydraulic Motor Figure 9...
Page 342: ...S0707345K Page 14 Travel Motor with Gearbox Reduction Gear Figure 10...
Page 386: ...S0707345K Page 58 Travel Motor with Gearbox...
Page 389: ...S0708355K Page 3 Main Pump Rexroth SECTIONAL VIEW A8VO140LA1KH1 63 AUS0010L Figure 1...
Page 390: ...S0708355K Page 4 Main Pump Rexroth AUS0020L Figure 2...
Page 401: ...S0708355K Page 15 Main Pump Rexroth 2 Sealing surface of the housing 2 AUS0140L Figure 33...
Page 415: ...S0708355K Page 29 Main Pump Rexroth 4 Remove bearing with extraction device ASS0550L Figure 61...
Page 418: ...S0708355K Page 32 Main Pump Rexroth 8 Pull out pinion bearing ASS0640L Figure 69...
Page 438: ...S0708355K Page 52 Main Pump Rexroth INSTALLATION OF COVER AUXILIARY DRIVE AUS0430L Figure 116...
Page 442: ...S0708355K Page 56 Main Pump Rexroth...
Page 448: ...S0709401K Page 6 Main Control Valve Kayaba Figure 1...
Page 449: ...S0709401K Page 7 Main Control Valve Kayaba Figure 2...
Page 451: ...S0709401K Page 9 Main Control Valve Kayaba...
Page 453: ...S0709401K Page 11 Main Control Valve Kayaba Figure 4...
Page 465: ...S0709401K Page 23 Main Control Valve Kayaba Figure 16...
Page 498: ...S0709401K Page 56 Main Control Valve Kayaba Figure 54...
Page 548: ...S0792190K Page 4 Hydraulic Schematic S340LC V SOLAR 340LC V Figure 2...
Page 549: ...S0792190K Page 5 Hydraulic Schematic S340LC V...
Page 550: ...S0792190K Page 6 Hydraulic Schematic S340LC V...
Page 551: ...1ELECTRICAL SYSTEM...
Page 552: ......
Page 606: ...S0802220K Page 54 Electrical System...
Page 625: ...S0802220K Page 73 Electrical System...
Page 632: ...S0892190K Page 4 Electrical Schematic S340LC V SOLAR 340LC V Figure 2...
Page 634: ...S0892190K Page 6 Electrical Schematic S340LC V...
Page 635: ...1ATTACHMENTS...
Page 636: ......
Page 656: ......