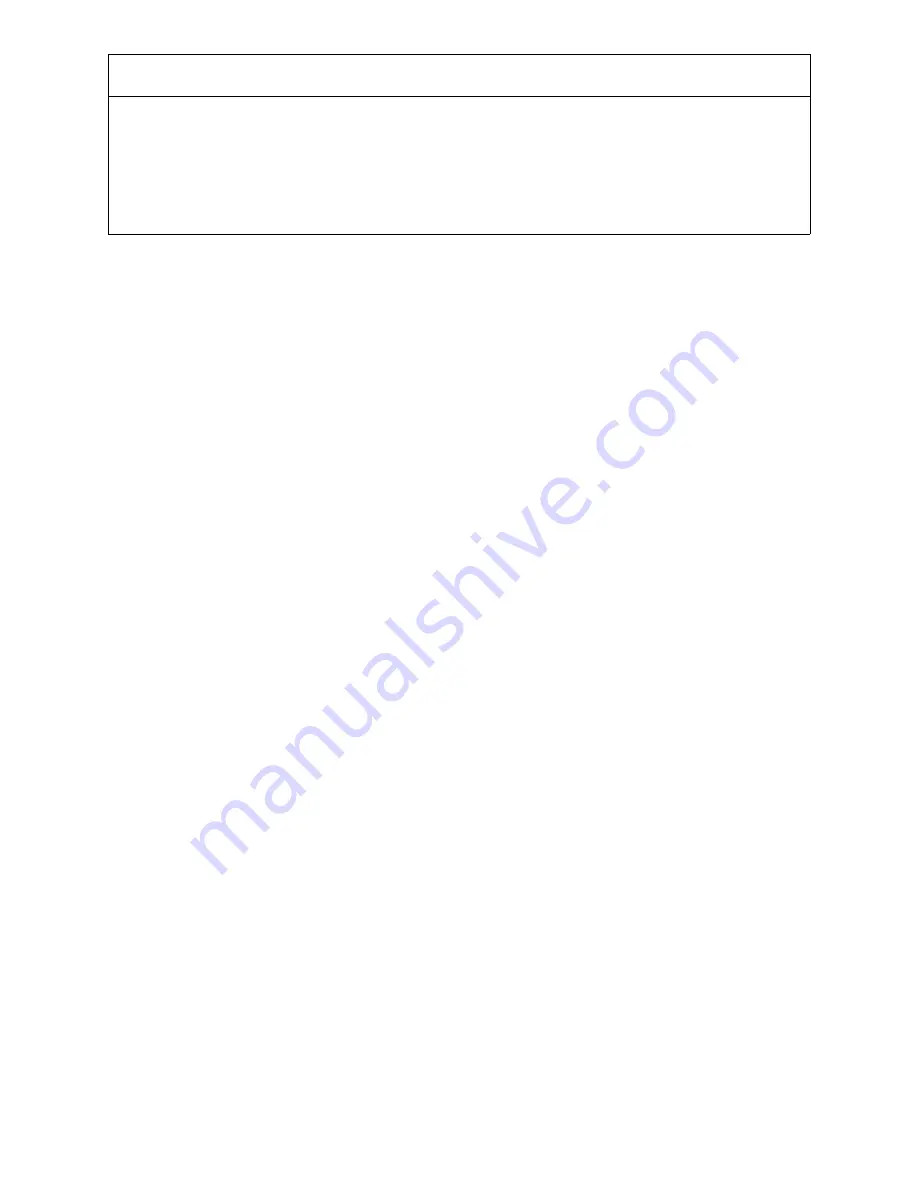
S0302000
Page 5
General Maintenance Procedures
Return to Master Table of Contents
MAINTENANCE SERVICE AND REPAIR PROCEDURE
GENERAL PRECAUTIONS
Fluid level and condition should always be checked whenever any other type of maintenance service or
repair is being performed.
NOTE:
If the unit is being used in an extreme temperature environment (in sub-freezing climates
or in high temperature, high humidity tropical conditions), frequent purging of moisture
condensation from the hydraulic reservoir drain tap should be a regular and frequent part
of the operating routine. In more moderate, temperate climates, draining reservoir
sediment and moisture may not be required more than once or twice every few months.
Inspect drained oil and used filters for signs of abnormal coloring or visible fluid contamination at every oil
change. Abrasive grit or dust particles will cause discoloration and darkening of the fluid. Visible
accumulations of dirt or grit could be an indication that filter elements are overloaded (and will require more
frequent replacement) or that disintegrating bearings or other component failures in the hydraulic circuit
may be imminent or have already occurred. Open the drain plugs on the main pump casings and check
and compare drain oil in the pumps. Look for evidence of grit or metallic particles.
Vibration or unusual noise during operation could be an indication of air leaking into the circuit (Refer to the
appropriate Troubleshooting section for component or unit for procedures.), or it may be evidence of a
defective pump. The gear-type pilot pump could be defective, causing low pilot pressure, or a main pump
broken shoe or piston could be responsible.
NOTE:
If equipped, indicated operating pressure, as shown on the multidisplay digital gauge on
the Instrument Panel ("F-Pump" and "R-Pump") will be reduced as a result of a
mechanical problem inside the pump. However, pressure loss could also be due to
cavitation or air leakage, or other faults in the hydraulic system.
Check the exterior case drain oil in the main pumps. If no metallic particles are found, make sure there is
no air in the system. Unbolt and remove the tank return drain line from the top part of the swing motor, both
travel motors and each main pump. If there is air in any one of the drain lines, carefully pre-fill the
assembly before bolting together the drain line piping connections. Run the system at low rpm.
IMPORTANT
Hydraulic system operating conditions (repetitive cycling, heavy work loads, fluid circulating
under high pressure) make it extremely critical that dust, grit or any other type of contamination
be kept out of the system. Observe fluid and filter change maintenance interval
recommendations and always pre-clean any exterior surface of the system before it is exposed
to air. For example, the reservoir filler cap and neck area, hoses that have to be disassembled,
and the covers and external surfaces of filter canisters should all be cleaned before
disassembly.
Summary of Contents for Solar 340LC-V
Page 2: ......
Page 4: ......
Page 7: ...1SAFETY...
Page 8: ......
Page 46: ...S0102000 Page 38 Track Excavator Safety...
Page 47: ...1SPECIFICATIONS...
Page 48: ......
Page 52: ...S0202110K Page 4 Specifications for Solar 340LC V COMPONENT LOCATIONS Figure 1...
Page 54: ...S0202110K Page 6 Specifications for Solar 340LC V...
Page 70: ...S0202110K Page 22 Specifications for Solar 340LC V...
Page 71: ...1GENERAL MAINTENANCE...
Page 72: ......
Page 86: ...S0302000 Page 14 General Maintenance Procedures Return to Master Table of Contents...
Page 99: ...1UPPER STRUCTURE...
Page 100: ......
Page 102: ...S0402040K Page 2 Cab TABLE OF CONTENTS Removal 3 Installation 6...
Page 116: ...S0403050K Page 8 Counterweight Return to Master Table of Contents...
Page 140: ...S0407000 Page 6 Swing Bearing...
Page 144: ...S0408030 Page 4 Swing Reduction Gearbox Return to Master Table of Contents PARTS LIST Figure 1...
Page 159: ...1LOWER STRUCTURE AND CHASSIS...
Page 160: ......
Page 184: ...S0505000 Page 24 Track Assembly 7 Tighten plug 1 Figure 48 Figure 48...
Page 185: ...S0505000 Page 25 Track Assembly TRACK SPRING AND TRACK ADJUSTING CYLINDER PARTS LIST Figure 49...
Page 187: ...1ENGINE AND DRIVE TRAIN...
Page 188: ......
Page 199: ...S0605060K Page 11 Air Conditioner Face and Defroster ARS1300L Figure 12...
Page 214: ...S0605060K Page 26 Air Conditioner...
Page 223: ...1HYDRAULICS...
Page 224: ......
Page 254: ...S0702180K Page 30 Hydraulic System Troubleshooting Testing and Adjustment...
Page 256: ...S0703010K Page 2 Accumulator TABLE OF CONTENTS General Description 3 Specifications 4...
Page 260: ...S0703010K Page 6 Accumulator...
Page 268: ...S0704030 Page 8 Center Joint Swivel...
Page 277: ...S0705000 Page 9 Cylinders...
Page 281: ...S0705000 Page 13 Cylinders...
Page 285: ...S0705000 Page 17 Cylinders...
Page 293: ...S0705000 Page 25 Cylinders...
Page 302: ...S0705000 Page 34 Cylinders 17 Force out pin bushing 1 from body of cylinder Figure 28...
Page 306: ...S0705000 Page 38 Cylinders...
Page 316: ...S0707280 Page 10 Swing Motor Return to Master Table of Contents Figure 6...
Page 339: ...S0707345K Page 11 Travel Motor with Gearbox...
Page 340: ...S0707345K Page 12 Travel Motor with Gearbox PARTS LIST Hydraulic Motor Figure 9...
Page 342: ...S0707345K Page 14 Travel Motor with Gearbox Reduction Gear Figure 10...
Page 386: ...S0707345K Page 58 Travel Motor with Gearbox...
Page 389: ...S0708355K Page 3 Main Pump Rexroth SECTIONAL VIEW A8VO140LA1KH1 63 AUS0010L Figure 1...
Page 390: ...S0708355K Page 4 Main Pump Rexroth AUS0020L Figure 2...
Page 401: ...S0708355K Page 15 Main Pump Rexroth 2 Sealing surface of the housing 2 AUS0140L Figure 33...
Page 415: ...S0708355K Page 29 Main Pump Rexroth 4 Remove bearing with extraction device ASS0550L Figure 61...
Page 418: ...S0708355K Page 32 Main Pump Rexroth 8 Pull out pinion bearing ASS0640L Figure 69...
Page 438: ...S0708355K Page 52 Main Pump Rexroth INSTALLATION OF COVER AUXILIARY DRIVE AUS0430L Figure 116...
Page 442: ...S0708355K Page 56 Main Pump Rexroth...
Page 448: ...S0709401K Page 6 Main Control Valve Kayaba Figure 1...
Page 449: ...S0709401K Page 7 Main Control Valve Kayaba Figure 2...
Page 451: ...S0709401K Page 9 Main Control Valve Kayaba...
Page 453: ...S0709401K Page 11 Main Control Valve Kayaba Figure 4...
Page 465: ...S0709401K Page 23 Main Control Valve Kayaba Figure 16...
Page 498: ...S0709401K Page 56 Main Control Valve Kayaba Figure 54...
Page 548: ...S0792190K Page 4 Hydraulic Schematic S340LC V SOLAR 340LC V Figure 2...
Page 549: ...S0792190K Page 5 Hydraulic Schematic S340LC V...
Page 550: ...S0792190K Page 6 Hydraulic Schematic S340LC V...
Page 551: ...1ELECTRICAL SYSTEM...
Page 552: ......
Page 606: ...S0802220K Page 54 Electrical System...
Page 625: ...S0802220K Page 73 Electrical System...
Page 632: ...S0892190K Page 4 Electrical Schematic S340LC V SOLAR 340LC V Figure 2...
Page 634: ...S0892190K Page 6 Electrical Schematic S340LC V...
Page 635: ...1ATTACHMENTS...
Page 636: ......
Page 656: ......