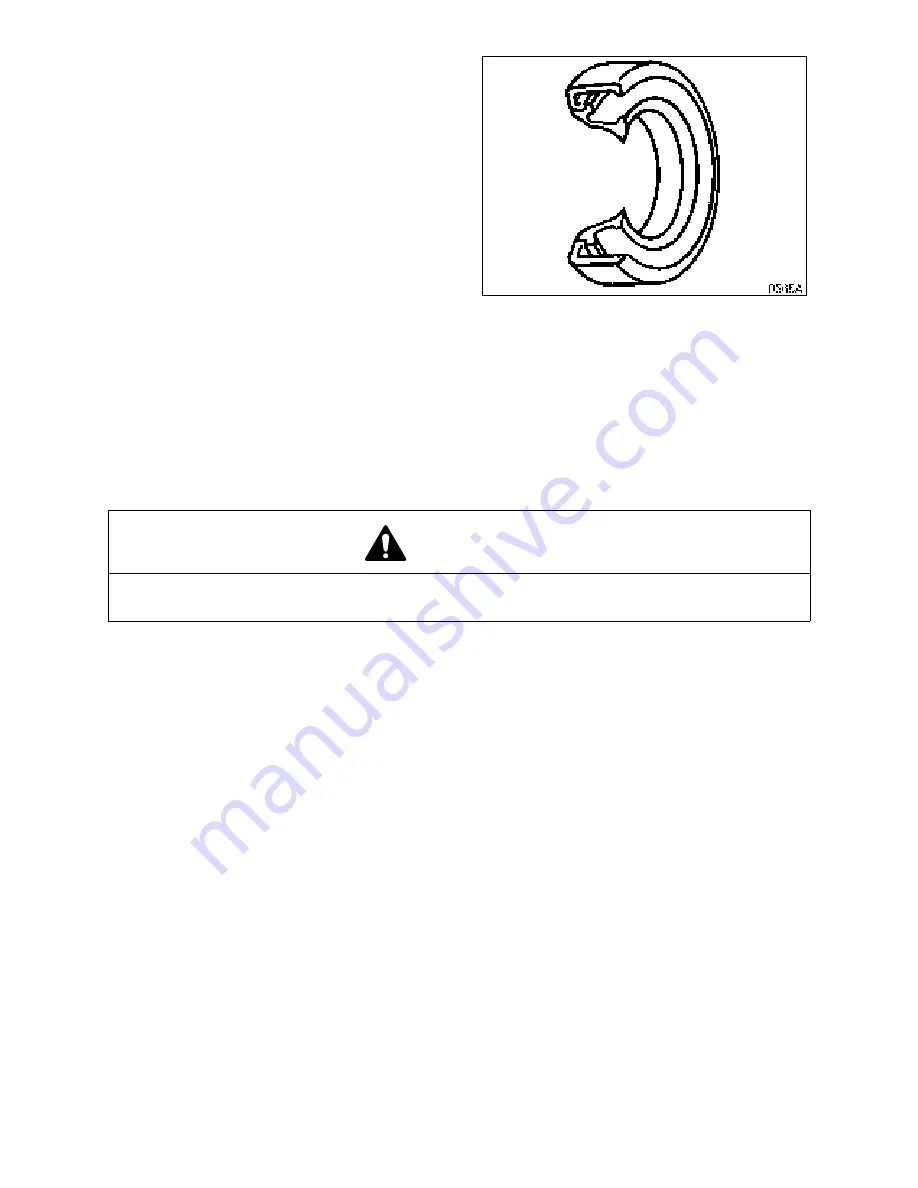
S0302000
Page 7
General Maintenance Procedures
NOTE:
Grease lip seals before
assembly.
CLEANING AND INSPECTION
GENERAL GUIDELINES
All parts must be clean to permit an effective inspection. During assembly, it is very important that no dirt or
foreign material enters unit being assembled. Even minute particles can cause malfunction of close fitting
parts such as thrust bearing, matched parts, etc.
1.
Clean all metal parts thoroughly using a suitable cleaning fluid. It is recommended that parts be
immersed in cleaning fluid and moved up and down slowly until all oils, lubricants, and/or foreign
materials are dissolved and parts are thoroughly clean.
2.
For bearings that can be removed, soak them in a suitable cleaning fluid for a minute or two, then
remove bearings from cleaning fluid and strike flat against a block of wood to dislodge solidified
particles of lubricant. Immerse again in cleaning fluid to flush out particles. Repeat above operation
until bearings are thoroughly clean. To dry bearings, use moisture-free compressed air. Be careful to
direct air stream across bearing to avoid spinning bearings that are not lubricated. DO NOT SPIN
BEARINGS WHEN DRYING; bearings may be rotated slowly by hand to facilitate drying process.
3.
Carefully inspect all bearing rollers, cages and cups for wear, chipping or nicks to determine
condition. Do not replace a bearing cone or cup individually without replacing mating cup or cone at
the same time. After inspection, dip bearings in light weight oil and wrap in clean lintless cloth or
paper to protect them until installation.
For those bearings that are to be inspected in place; inspect bearings for roughness of rotation,
scoring, pitting, cracked or chipped races. If any of these defects are found, replace bearings. Also
inspect defective bearing housing and/or shaft for grooved, galled or burred conditions that indicate
bearing has been turning in its housing or on its shaft.
4.
It is more economical to replace oil seals, O-rings, sealing rings, gaskets and snap rings when unit is
disassembled than waiting for premature failures; refer to latest Micro Fiche and/or Parts Book for
replacement items. Be extremely careful when installing sealing members, to avoid cutting or
WARNING!
Care should be exercised to avoid inhalation of vapors, exposure to skin and creating fire
hazards when using solvent type cleaners.
Figure 1
Summary of Contents for Solar 225LC-V
Page 2: ......
Page 4: ......
Page 7: ...1SAFETY ...
Page 8: ......
Page 46: ...S0102000 Page 38 Track Excavator Safety ...
Page 47: ...1SPECIFICATIONS ...
Page 48: ......
Page 54: ...S0205015K Page 6 Specifications for Solar 225LC V Return to Master Table of Contents ...
Page 70: ...S0205015K Page 22 Specifications for Solar 225LC V Return to Master Table of Contents ...
Page 71: ...1GENERAL MAINTENANCE ...
Page 72: ......
Page 86: ...S0302000 Page 14 General Maintenance Procedures ...
Page 99: ...1UPPER STRUCTURE ...
Page 100: ......
Page 102: ...S0402040K Page 2 Cab TABLE OF CONTENTS Removal 3 Installation 6 ...
Page 116: ...S0403050K Page 8 Counterweight Return to Master Table of Contents ...
Page 140: ...S0407000 Page 6 Swing Bearing ...
Page 165: ...1LOWER STRUCTURE AND CHASSIS ...
Page 166: ......
Page 192: ...S0505030 Page 26 Track Assembly Return to Master Table of Contents ...
Page 193: ...1ENGINE AND DRIVE TRAIN ...
Page 194: ......
Page 205: ...S0605060K Page 11 Air Conditioner Face and Defroster ARS1300L Figure 12 ...
Page 229: ...S0609000 Page 9 Drive Coupling Main Pump Figure 10 DRIVE COUPLING INSTALLATION UCHIDA PUMP ...
Page 234: ...S0609000 Page 14 Drive Coupling Main Pump ...
Page 235: ...1HYDRAULICS ...
Page 236: ......
Page 249: ...S0702170K Page 13 Hydraulic System Troubleshooting Testing and Adjustment ...
Page 272: ...S0702170K Page 36 Hydraulic System Troubleshooting Testing and Adjustment ...
Page 274: ...S0703010K Page 2 Accumulator TABLE OF CONTENTS General Description 3 Specifications 4 ...
Page 297: ...S0705000 Page 9 Cylinders ...
Page 301: ...S0705000 Page 13 Cylinders ...
Page 311: ...S0705000 Page 23 Cylinders ...
Page 315: ...S0705000 Page 27 Cylinders ...
Page 324: ...S0705000 Page 36 Cylinders 17 Force out pin bushing 1 from body of cylinder Figure 28 ...
Page 328: ...S0705000 Page 40 Cylinders ...
Page 335: ...S0707200 Page 7 Swing Motor Return to Master Table of Contents ...
Page 341: ...S0707200 Page 13 Swing Motor Return to Master Table of Contents SPECIAL TOOLS Figure 6 ...
Page 358: ...S0707200 Page 30 Swing Motor Return to Master Table of Contents ...
Page 452: ...S0708320 Page 40 Main Pump With Regulator Return to Master Table of Contents ...
Page 458: ...S0709401K Page 6 Main Control Valve Kayaba Figure 1 ...
Page 459: ...S0709401K Page 7 Main Control Valve Kayaba Figure 2 ...
Page 461: ...S0709401K Page 9 Main Control Valve Kayaba ...
Page 463: ...S0709401K Page 11 Main Control Valve Kayaba Figure 4 ...
Page 475: ...S0709401K Page 23 Main Control Valve Kayaba Figure 16 ...
Page 508: ...S0709401K Page 56 Main Control Valve Kayaba Figure 54 ...
Page 563: ...1ELECTRICAL SYSTEM ...
Page 564: ......
Page 618: ...S0802220K Page 54 Electrical System ...
Page 637: ...S0802220K Page 73 Electrical System ...
Page 649: ...1ATTACHMENTS ...
Page 650: ......
Page 670: ......