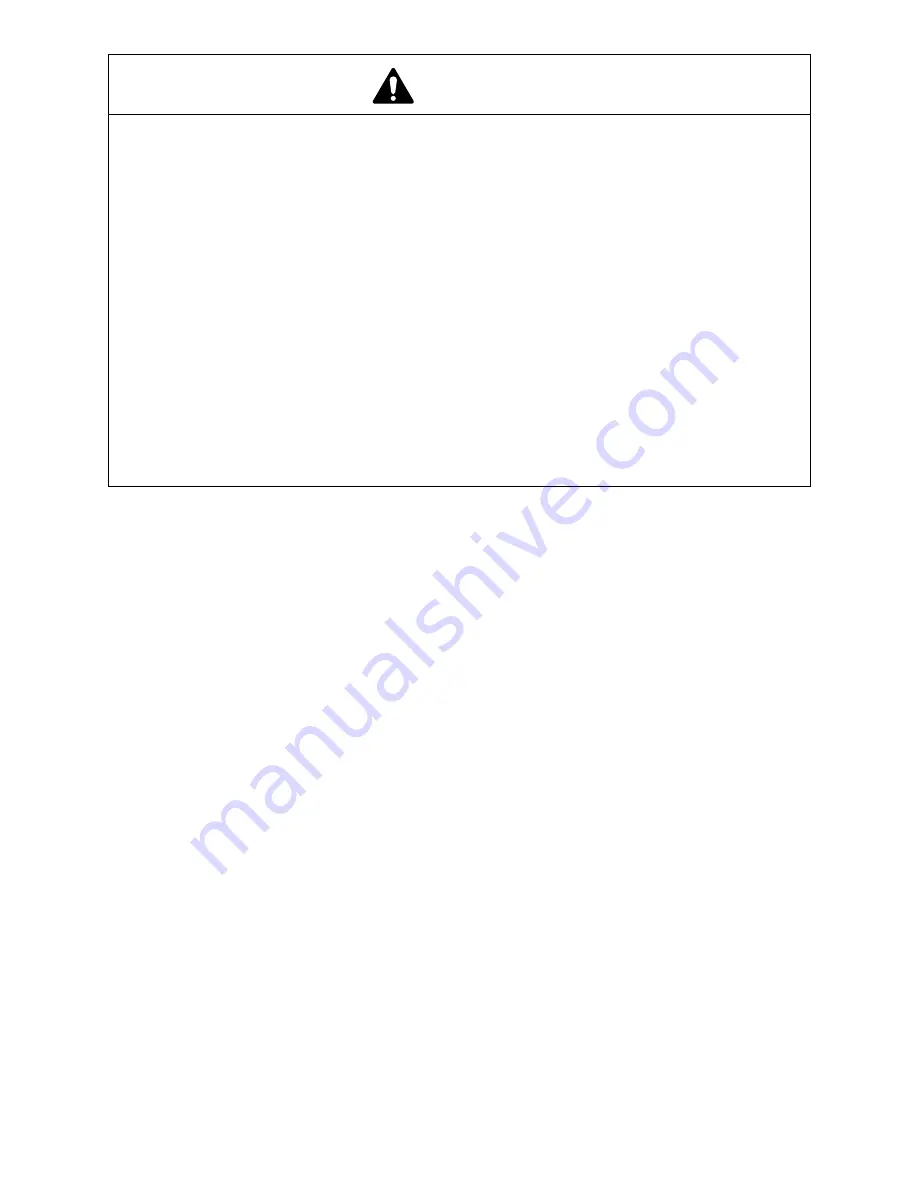
Page 4
General Maintenance Procedures
HYDRAULIC SYSTEM - GENERAL PRECAUTIONS
Always maintain oil l evel i n t he syst em at recom mended l evels. Assemblies t hat ope rate under hea vy
loads, at high speed, with extremely precise dimensional tolerances between moving parts – pistons and
cylinders, or shoes and swash plates, for example – can be severely damaged if oil supply runs dry.
Assemblies can be run dry and dam aged s everely in a v ery s hort t ime when pi ping or hoses are
disconnected to repair leaks and/or replace damaged components. Hoses that are inadvertently switched
during disassembly (inlet for outlet and vice versa), air introduced into the system or assemblies that are
low on oil due to neglect or careless maintenance, could all produce sufficient fluid loss to cause damage.
When starting the engine (particularly after long layoff or storage intervals), make sure that all hydraulic
controls and operating circuits are in neutral, or “OFF.” That will prevent pumps or other components that
may be temporarily oil-starved from being run under a load.
Replacement of an y h ydraulic s ystem component c ould r equire t horough c leaning, f lushing, and s ome
amount of pre-filling with fresh, clean oil if the protective seal on r eplacement par ts has obviously been
broken or i f s eal i ntegrity m ay h ave been c ompromised. When p rotective s eals are rem oved pr ior t o
installation and reassembly, inspect al l repl acement parts c arefully, b efore they are installed. I f t he
replacement par t is bone dr y (with no trace of factory pre-lube) or has been c ontaminated by dirt or b y
questionable oils, flushing and pre-filling with clean hydraulic fluid is recommended.
Vibration, irregular or difficult movement or unusual noise from any part of the hydraulic system could be
an indication of air in the system (as well as many other types of problems). As a general precaution (and
to help minimize the risk of potential long-term damage), a llow the engine to r un at no-load idle speed
immediately after initial start-up. Hydraulic fluid will circulate, releasing any air that may have been trapped
in the system before load demands are imposed.
A daily walk-around pre-start equipment safety inspection, including a quick visual scan for any exterior
evidence of leaking hydraulic fluid, can help extend the service life of system components.
CAUTION!
Observe the following safety precautions:
1.
Use extra caution and adequate safety shielding when welding near fuel and oil tanks,
batteries, hydraulic piping lines or other fire hazards.
2.
Never weld when the engine is running. Battery cables must be disconnected before the
welding procedure is started.
3.
Never weld on a wet or damp surface. The presence of moisture causes hydrogen
embrittlement and structural weakening of the weld.
4.
If welding procedures are being performed near cylinder rods, operator’s cab window areas
or any other assemblies that could be damaged by weld spatters, use adequate shielding
protection in front of the assembly.
5.
During equipment setup, always attach ground cables directly to the area or component
being welded to prevent arcing through bearings, bushings, or spacers.
6.
Always use correct welding rods for the type of weld being performed and observe
recommended precautions and time constraints. AWS Class E7018 welding rods for low
alloy to medium carbon steel must be used within two hours after removal from a freshly
opened container. Class E11018G welding rods for T-1 and other higher strength steel must
be used within 1/2 hour.