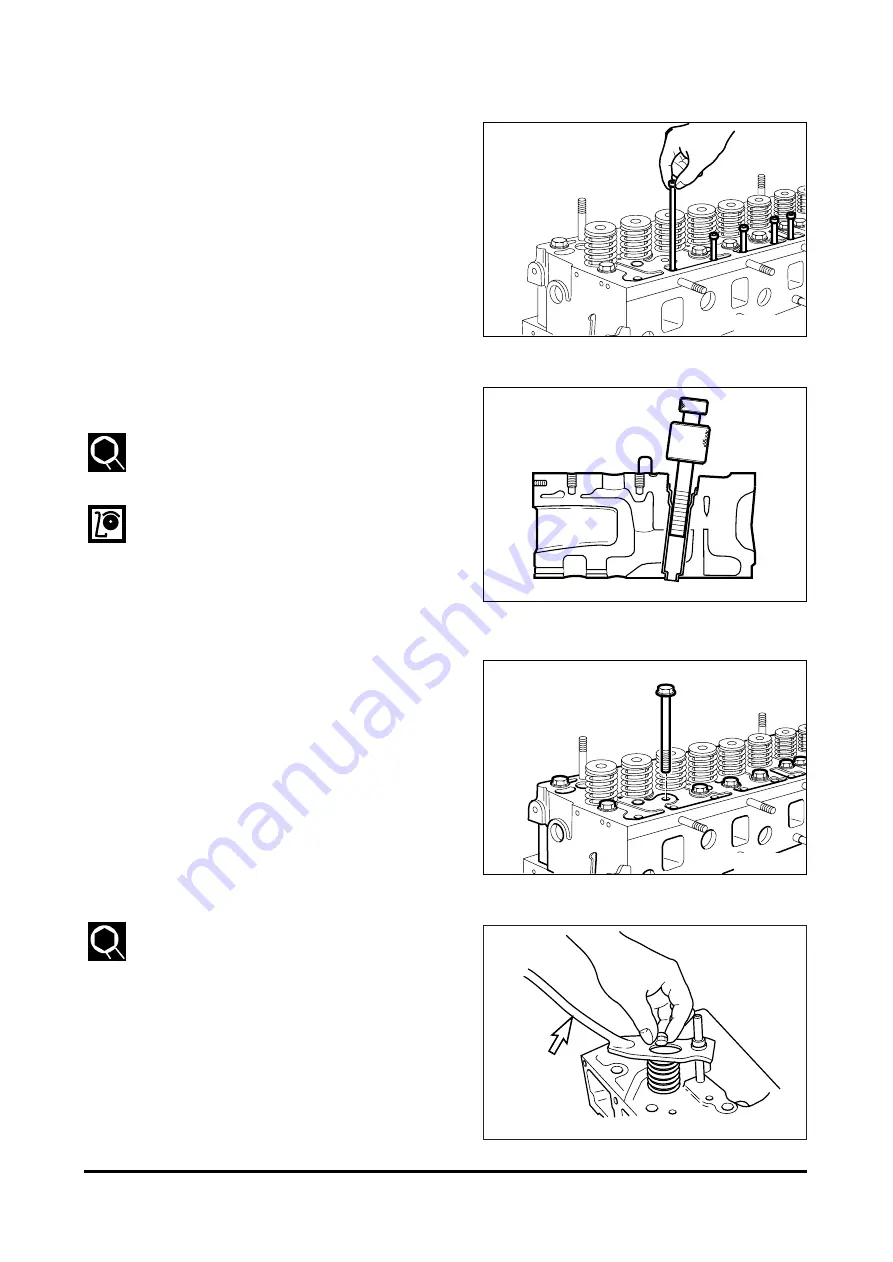
3.1.25. Rocker arm
•
Unscrew the rocker arm bracket bolts
and remove the rocker arm assembly.
•
Take off the snap rings to remove the
washers and rocker arm, then
unscrew the bracket fixing bolts to
take off the bracket and springs.
•
Take out the push rods.
3.1.26. Injection nozzle and tube
•
Remove the nozzle fixing nuts and
extract the nozzles.
•
Remove the nozzle tube using nozzle
tube removing jig.
NOTE :
Do not disassemble the nozzle tube
if coolant or gas, etc. does not come
out during engine operation.
3.1.27. Cylinder head
•
Unscrew the cylinder head fixing
borts and take off the cylinder head.
•
Remove the cylinder head gasket.
3.1.28. Valve and stem seal
•
Compress the valve spring retainer
using a jig and take off the valve cot-
ter pins.
•
Disassemble the valve springs and
retainers.
•
Take off the valves.
•
Remove and discard the valve stem
seal using a general tool as it should
not be re-used.
- 55 -
DISASSEMBLY
EAMD029I
EAMD030I
EAMD031I
밸브 스프링
압축공구
EA0M4007
Compress
the spring
Summary of Contents for DE12T
Page 2: ......
Page 187: ... Engine Assembly DE12TIS ECIEA 183 APPENDIX EE6OM026 ...
Page 188: ......