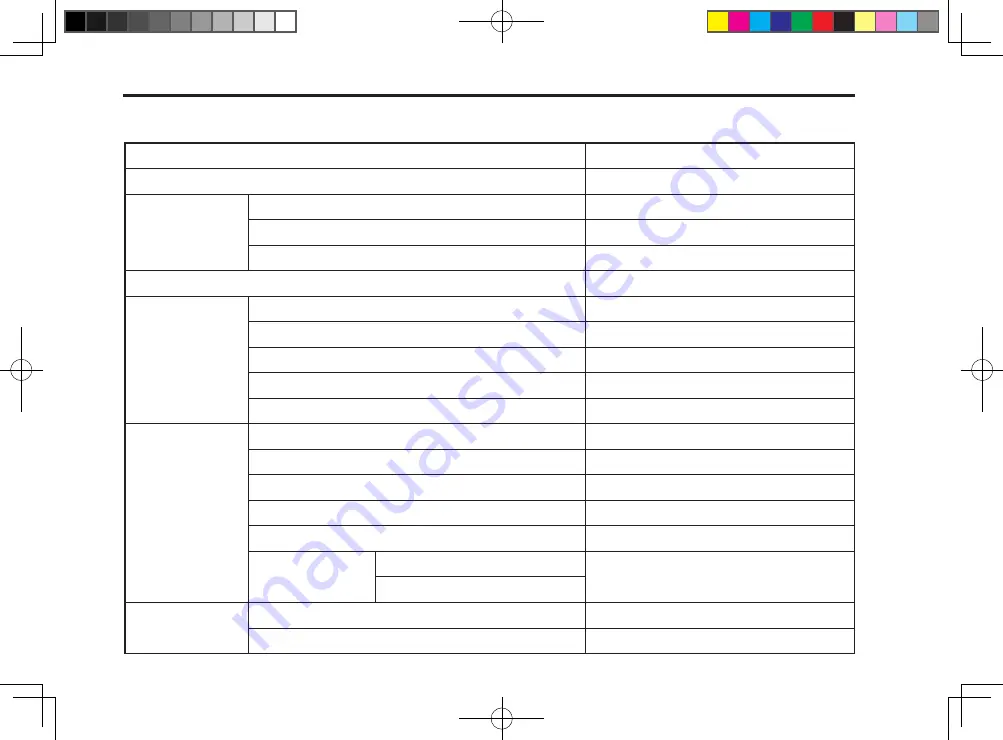
3-2.
DSC62
SpecificationS
Model
DSc62
Structural Quality
Crawler self-propelled half-feed model
Structural Quality
(Dimension of
working state)
Length
(mm)
4254(4385)
Width
(mm)
1954(2570)
Height
(mm)
2360
Total Weight
(kg)
2335
Engine
Model
4B243DITC-CH
Type
Water-cooled 4-cycle 4 cylinder in-line diesel
Displacement
(cc)
2435
Rated output/rotating speed
kW/(r/min)
45.6/2700
Fuel tank capacity
(ℓ)
65
Driving Unit
Crawler (Width x Length of ground contact)
(mm)
400x1350
Center distance of crawler
(mm)
1000
Average ground contact pressure
(kpa)
≤
21.2
Available speeds
Hydrostatic transmission (HST)
Minimum ground clearance
(mm)
190
Driving speed
(m/s)
Forward
Low Speed
:0
~
1.0
Standard
:0
~
1.5
High Speed
:0
~
1.9
Backward
Reaping Unit
Reaping width
(mm)
1450
Reaping rows
4
DSC62-영문판-3장.indd 2
2012-04-16 오후 6:33:20
Summary of Contents for DSC62
Page 10: ...DSC62 0 indd 10 2012 04 16 6 34 10...
Page 34: ...MEMO MEMO DSC62 1 indd 24 2012 04 17 10 20 24...
Page 35: ...ABOUT SERVICE 2 2 2 SERVICE 2 DSC62 2 indd 1 2012 04 16 6 32 54...
Page 37: ...Specifications 3 2 3 Specifications 3 DSC62 3 indd 1 2012 04 16 6 33 20...
Page 63: ...daily check 5 2 5 Pre starting Checks 5 DSC62 5 indd 1 2012 04 17 5 35 22...
Page 68: ...MEMO MEMO DSC62 5 indd 6 2012 04 17 5 35 27...
Page 98: ...MEMO MEMO DSC62 7 indd 22 2012 04 17 4 56 40...
Page 162: ...MEMO MEMO DSC62 8 indd 64 2012 04 17 5 36 57...
Page 163: ...LONG TERM STORAGE 9 2 9 LONG TERM STORAGE 9 DSC62 9 indd 1 2012 04 16 6 27 10...
Page 174: ...MEMO MEMO DSC62 10 indd 10 2012 04 16 6 26 10...
Page 178: ...MEMO MEMO DSC62 11 indd 4 2012 04 16 5 16 28...
Page 179: ...INDEX 12 1 12 INDEX 12 DSC62 12 indd 1 2012 04 16 5 15 55...