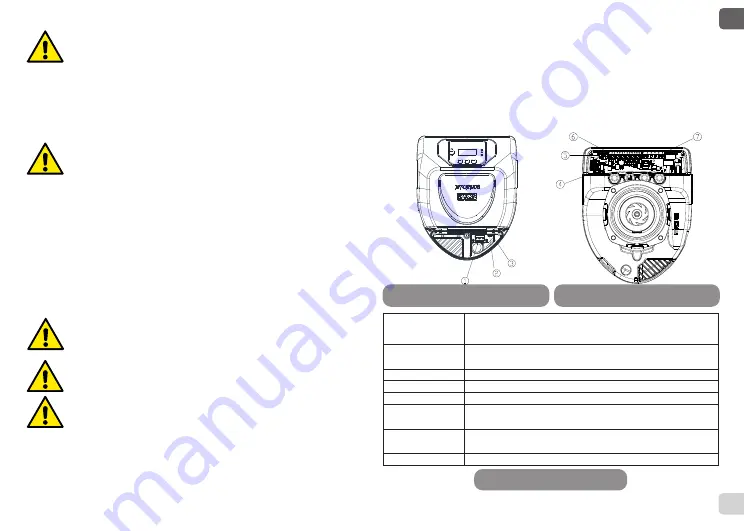
ENGLISH
GB
14
Never insulate the electronic control device.
- In the case of maintenance, always use a set of new gaskets.
5.2 Rotation of the Motor Heads
If the circulator is installed on pipes in a horizontal position, it will be necessary to rotate
the motor with the respective electronic device through 90 degrees in order to maintain
the grade of IP protection and to allow the user a more convenient interaction with the
graphic interface (see Figure 2-3).
Before rotating the circulator, ensure that it has been completely drained.
Should it be necessary to rotate the motor heads, follow the instructions below with care
to ensure correct installation:
1.
Unscrew the 4 screws fixing the motor assembly to the pump body (figure A).
2.
Rotate the motor assembly keeping it in the seat where it couples with the pump
body (figure A-B).
3.
Once the head has been rotated into the desired position, tighten the 4 screws,
always proceeding in cross formation (figure C).
If the motor assembly has been removed from its seat, pay the greatest attention during
assembly, taking care to insert the impeller completely in the floating ring before tighten
-
ing the retaining screws (figure D). If it has been correctly assembled, the motor assembly
rests completely on the pump body.
Incorrect assembly may damage the impeller, causing a typical rubbing
noise when the circulator starts.
T
he electronic control device must always remain in vertical position!
Ensure that the connecting cable of the pressure sensor never comes in
contact with the motor casing.
5.3 Non-return valve
If the system is equipped with a non-return valve, ensure that the minimum pressure of
the circulator is always higher than the valve closing pressure.
6. ELECTRICAL CONNECTIONS
The electrical connections must be made by expert, qualified personnel.
-
The circulator does not require any external motor protection.
-
Ensure that the supply voltage and frequency are the same as the values indicated on
the electrical data plate of the circulator.
Figure 4: Electrical connections (front)
Figure 5: Electrical connections (rear)
Reference
(Figure 4 and Figure 5)
Description
1
Pull-out terminal board for connection of the supply line:
1x220-240 V, 50/60 Hz
2
auxiliary LED
3
system live indicating LED
4
Connector for connecting twin circulators
5
Connector for connecting the fluid pressure and temperature sen
-
sor (standard)
6
Pull-out 13-pole terminal board for connecting the inputs and the
MODBUS systems
7
Pull-out 6-pole terminal board for alarm signals and system status
Table 1 Electrical connections