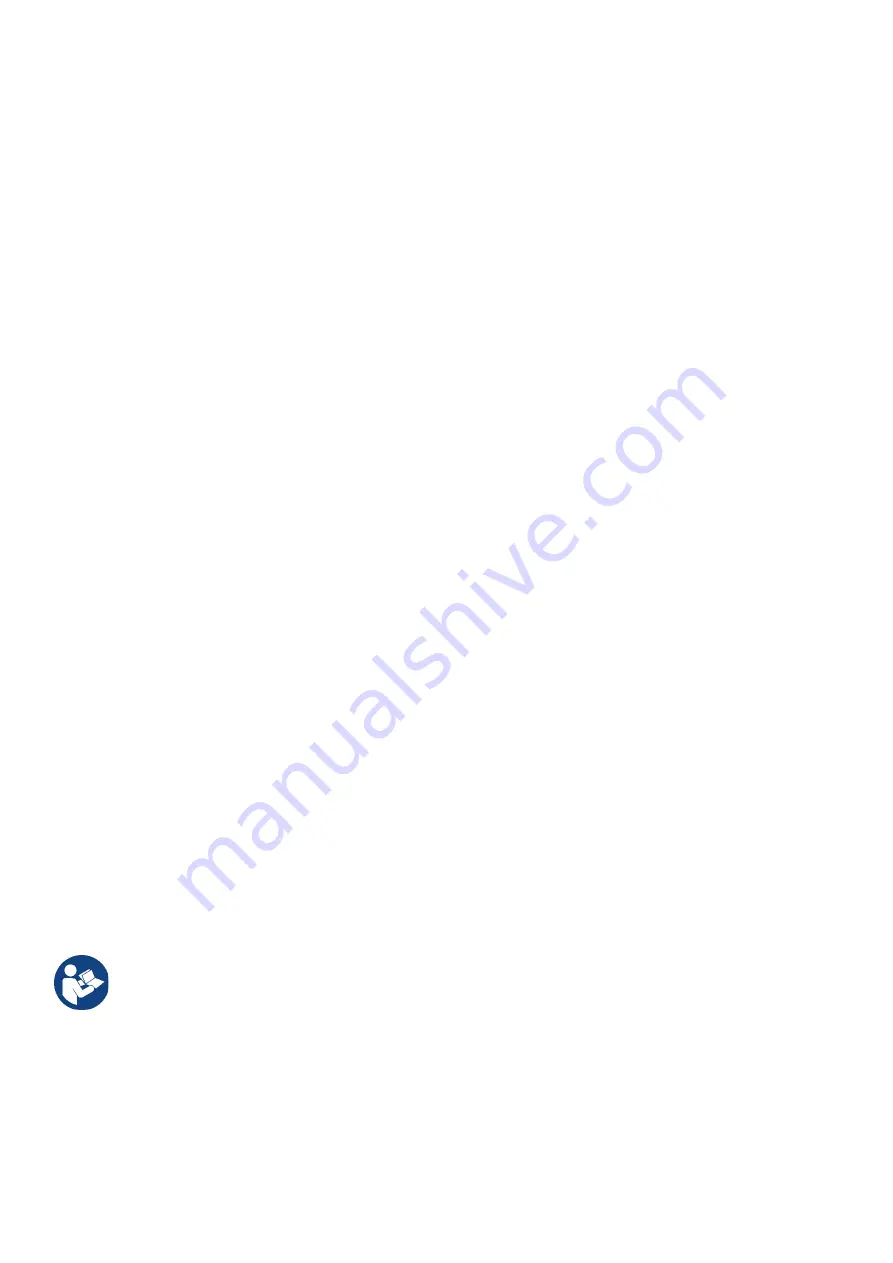
ENGLISH
57
8.6.10
IC: Configuration of the reserve
Configures the device as automatic or reserve. If set on auto (default) the device participates in normal pumping, if configured as reserves,
minimum starting priority is associated with it, this means that the device with this setting will always start last. If a number of active devices is
set that is one lower than the number of devices present and if one element is set as reserve, the effect obtained is that, if there are no
problems, the reserve device does not participate in regular pumping; instead, if one of the devices that participates in pumping develops a fault
(maybe loss of power supply, tripping of a protection, etc.), the reserve device will start.
The state of configuration as a reserve can be seen as follows: on the Multi-pump System page, the top of the icon is coloured; on the AD and
main pages, the communication icon representing the address of the device appears with the number on a coloured background. There may be
more than one device configured as reserve in a pumping system.
Even though the devices configured as reserve do not participate in normal pumping, they are nevertheless kept efficient by the anti-stagnation
algorithm. The anti-stagnation algorithm changes the starting priority once every 23 hours and allows the accumulation of at least one
continuous minute of supply of flow from each device. The aim of this algorithm is to avoid the deterioration of the water inside the impeller and
to keep the moving parts efficient; it is useful for all devices and especially for those configured as reserve, which do not work in normal
conditions.
8.6.11
Configuration examples for multi-pump plants
Example 1:
A pump set composed of 2 devices (N=2 detected automatically) of which 1 set active (NA=1), one simultaneous (NC=1 or NC=NA since NA=1)
and one as reserve (IC=reserve on one of the two devices).
The result obtained is the following: the device not configured as a reserve will start and work by itself (even though it does not manage to bear
the hydraulic load and the pressure achieved is too low). If it has a fault, the reserve device steps in.
Example 2:
A pump set composed of 2 devices (N=2 detected automatically) in which all the devices are active and simultaneous (factory settings NA=N and
NC=NA) and one as reserve (IC=reserve on one of the two devices).
The result obtained is the following: the device that is not configured as reserve always starts first, if the pressure detected is too low the second
device, configured as reserve, also starts. In this way we always try to preserve the use of one device in particular (the one configured as
reserve), but this may be useful in case of necessity when a greater hydraulic load occurs.
Example 3:
A pump set composed of 4 devices (N=4 detected automatically) of which 3 set active (NA=3), 2 simultaneous (NC=2) and 1 as reserve
(IC=reserve on two devices).
The result obtained is the following: at the most 2 devices will start at the same time. The operation of the 2 that can work simultaneously will
take place in rotation among 3 devices so as to respect the maximum exchange time of each (ET). If one of the active devices develops a fault
no reserve starts up because more than 2 devices cannot start at one time (NC=2) and there are still 2 active devices present. The reserve
intervenes as soon as another of the 2 develops a fault.
8.6.12
ET: Max. switching time
Sets the maximum continuous working time of a device in a set. It is significant only on pump sets with interconnected devices. The time can be
set between 1 min and 9 hours; the factory setting is 2 hours.
When the ET of a device has elapsed the system starting order is reassigned so as to give minimum priority to the device on which the time has
elapsed. The aim of this strategy is to use less the device that has already worked and to balance the working time between the various
machines that make up the set. If the hydraulic load still requires the intervention of the device, even though it has been put last in starting order,
it will start to guarantee pressure boosting of the system.
The starting priority is reassigned in two conditions based on the ET time:
Exchange during pumping: when the pump remains on without interruption until the absolute maximum pumping time has been
exceeded.
1.
Exchange to standby: when the pump is on standby but 50% of the ET time has been exceeded.
If ET has been set at 0 there will be exchange to standby. Whenever a pump in the set stops, a different pump will start first next time it is
restarted.
If the parameter ET (Max. switching time) is set at 0, there will be exchange at each restart, irrespective of the pump’s actual
work time.
8.6.13
AY: Anti Cycling
As described in paragraph 10.1.2 this function is for avoiding frequent switching on and off in the case of leaks in the system. The function can
be enabled in 2 different modes, normal and smart. In normal mode the electronic control blocks the motor after N identical start/stop cycles. In
smart mode it acts on the parameter RP to reduce the negative effects due to leaks. If set on “Disable”, the function does not intervene.
8.6.14
AE: Enabling the anti-block function
This function is for avoiding mechanical blocks in the case of long inactivity; it acts by periodically rotating the pump.
When the function is enabled, every 23 hours the pump performs an unblocking cycle lasting 1 min.