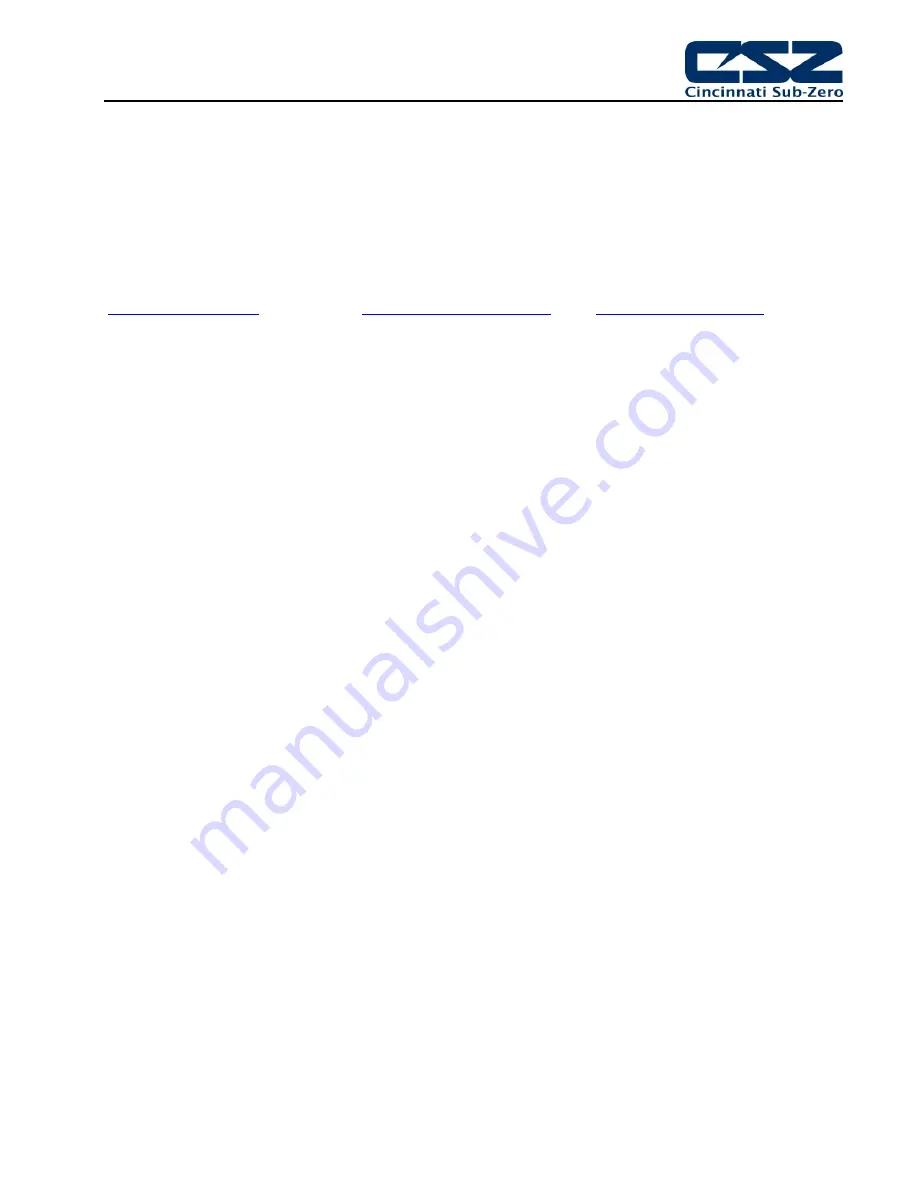
EZT-430i Communications Manual
Serial
Communication
CSZ
EZT-430i
REV
C
4.6
4.3 Creating
your
own Modbus Application
Listed below are a few of the more common software packages that claim to support the Modbus protocol.
This list is provided as informational only. Contact the software manufacturer for more information on
applying their software.
LabView by National Instruments
Wonderware by Wonderware
SpecView by SpecView Corporation
11500 N Mopac Expwy
26561 Rancho Pkwy. South
13409 53
rd
Ave NW
Austin, TX 78759-3504
Lake Forest, CA 92630
Gig Harbor, WA 98332
Phone 800-683-8411
Phone 949-727-3200
Phone 253-853-3199
http://www.natinst.com
http://www.wonderware.com
http://www.specview.com
If you already have a software application that uses Modbus, you can simply skip to the EZT-430i parameter
table in the Getting Started section for the information your program requires. The rest of this section
provides information on writing a software application that uses Modbus.
1. You must code messages in eight-bit bytes, with even parity, one stop bit (8, even, 1). EZT-430i has its
parity set to even as default from the factory.
2. Negative parameter values must be written in twos' complement format. Parameters are stored in two-
byte registers accessed with read and write commands to a relative address.
3. Messages are sent in packets that must be delimited by a pause at least as long as the time it takes to
send 28 bits (3.5 characters). To determine this time in seconds, divide 28 by the baud rate. In the case
of EZT-430i communications at 9600 baud, this caulates to a minimum period of ~3ms.
In addition, the EZT-430i timeout period must be added to that in order to properly time the send and
receive messages between the host computer and multiple EZT-430i controllers on the serial link. With a
default timeout period in EZT-430i of 135ms, it makes a total pause of 138ms minimum. Thus, after you
receive a response from an EZT-430i controller at your PC, you must wait a minimum of 138ms before
sending the next command.
4. Values containing decimal points such as process values and set points, have the decimal point implied,
i.e., the data exchange can only be performed using whole numbers. Thus, the value must be scaled
appropriately in order to exchange the data correctly. For example, a setpoint of 78.4 degrees must be
sent as a value of 784 in order for EZT-430i to be set correctly. Likewise, a process value read from EZT-
430i with a value of 827 is actually 82.7 degrees. Consult the parameter table for the proper format and
allowable range of each value.
5. When monitoring a process, try to keep the number of read and write commands to a minimum of 500ms
between exchanges to a single controller. Continuously reading data at a faster rate consumes an
excess amount of the controller’s processor time and does not provided any additional benefits in process
monitoring.
Handling Communication Errors
Messages with the wrong format or illegal values will receive an exception response. Messages with the
wrong CRC or timing will receive no response. It is the user’s responsibility to handle the error appropriately
within their own software and determine whether to resend the message or halt for operator intervention.
User Responsibility
Refrain from reading or writing from/to a register that does not exist or is currently disabled. Writing values to
unassigned registers could cause system instability, malfunction or failure. Care must also be taken in that
the process can not cause damage to property or injury to personnel if the wrong commands are sent due to
operator error or equipment malfunction.