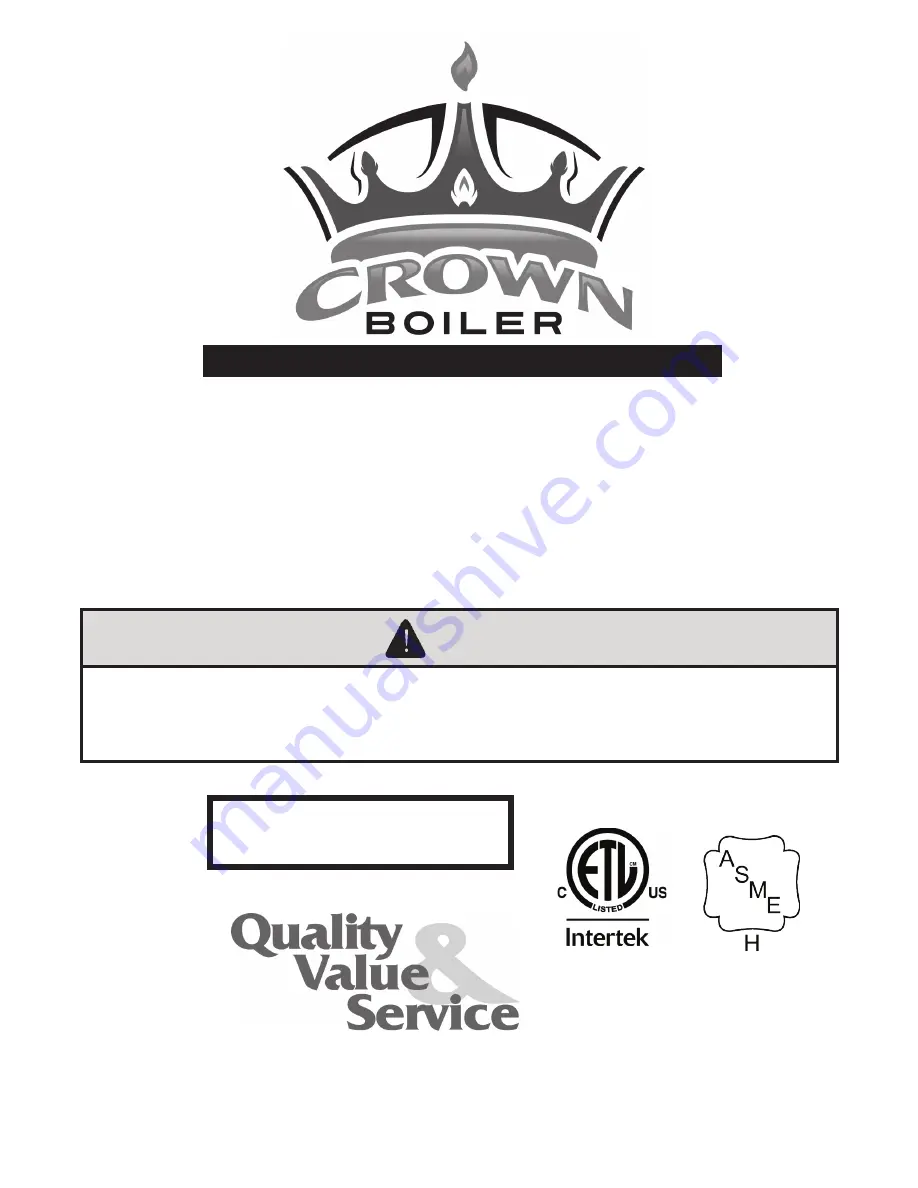
TWB Series
Oil-Fired Hot Water Boilers
INSTALLATION INSTRUCTIONS
These instructions must be affixed on or adjacent to the boiler
Models:
•
TWB065
•
TWB075
•
TWB100
•
TWB125
•
TWB150
•
TWB175
•
TWB200
D
E S I G N E D T O
L
E A D
Equipped with Hydrolevel
3250-Plus Control System
WARNING
Improper installation, adjustment, alteration, service or maintenance can cause property damage,
injury, or loss of life. For assistance or additional information, consult a qualified installer, service
agency or the fuel supplier. Read these instructions carefully before installing, operating, or
servicing this boiler. Keep boiler and any provided component instructions in legible condition and
posted near boiler for reference by owner and service technician.
980270B Rev 0, 11-20
Crown Boiler Company
P.O. Box 14818
3633 I Street
Philadelphia, PA 19134
www.crownboiler.com
9902339
Summary of Contents for TWB Series
Page 2: ......
Page 12: ...10 FIGURE 4 1 FIELD INSTALLATION OF FLUE BAFFLES...
Page 18: ...16 FIGURE 6 4 ALLAIR FROM OUTDOORS USING HORIZONTAL DUCTS INTO BOILER ROOM...
Page 23: ...21 FIGURE 8 3 BOILER BYPASS PIPING FIGURE 8 2 INDIRECT WATER HEATER BOILER SIDE PIPING...
Page 31: ...29 FIGURE 11 0 CONNECTIONS DIAGRAM BOILERS WITH OR LESS TANKLESS HEATER...
Page 51: ...49...
Page 53: ...51...
Page 54: ...52 SERVICE RECORD DATE SERVICE PERFORMED...
Page 55: ...53 Notes...