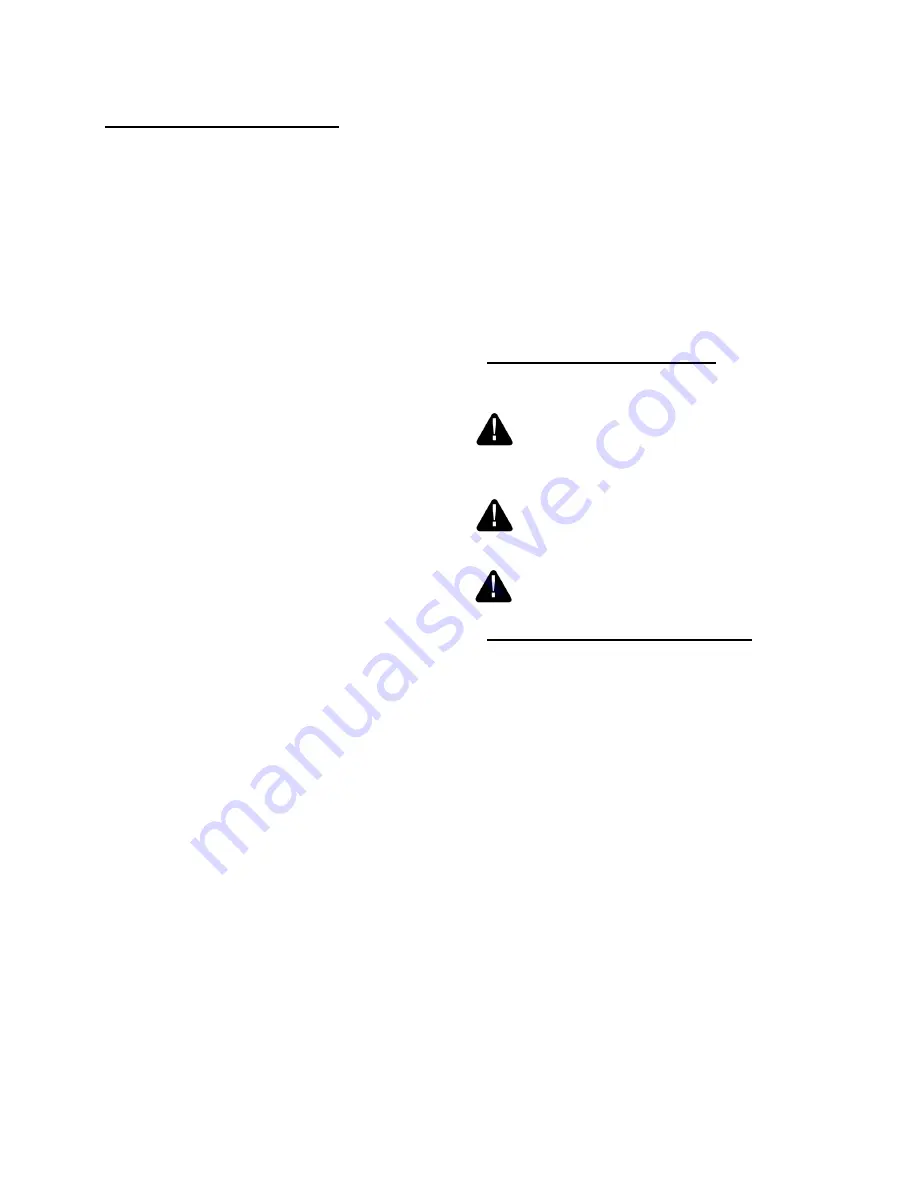
SECTION: D START-UP OPERATION
D-1) Check Voltage and Phase:
Before operating pump, compare the voltage and phase
information stamped on the pump’s identification plate to the
available power.
D-2) Check Pump Rotation:
Before putting pump into service for the first time, the motor
rotation must be checked. Improper motor rotation can result
in poor pump performance and can damage the motor and/or
pump. To check the rotation, suspend the pump freely,
momentarily apply power and observe the "kickback".
"Kickback" should always be in a counter-clockwise direction
as viewed from the top of the pump motor housing.
D-2.1) Incorrect Rotation for Three-Phase Pumps:
In the event that the rotation is incorrect for a three-phase
installation, interchange any two power cable leads at the
control box. Recheck the "kickback" rotation again by
momentarily applying power.
D-2.2) Operation Precautions:
1. Do not operate the pump in the "hand" control position
and leave the pump unattended.
2. Minimize the amount of cooking grease entering the
system.
3. Prevent large articles of clothing, large amounts of
chemicals, other materials or substances such as
are uncommon in domestic sewage from entering
the system.
4. During power black-outs, discontinue water
consumption to prevent sewage from backing up.
5. Prevent infiltration or direct flow of rain or run-off water
into the system to minimize pump cycling.
This will prevent overloading the treatment facility, and
will facilitate swift transportation of sewage.
6. Always keep the shut-off valve completely open when
system is in operation, (unless advised otherwise by the
proper authorities).
7. Keep the control panel locked or confined to prevent
unauthorized access to it.
8. If the pump is idle for long periods of time, it is
advisable to start the pump occasionally by adding
water to the system.
9. Before removing the pump from the system, be sure
to close the shut-off valve. (This prevents backflow from
the pressure sewer.)
10. Make sure level controls are provided at time of
installation.
11. Recommended starts per hour, 6 to 8, no more than 10.
D-3) Start-Up Report:
Included at the end of this manual are two start-up report
sheets, these sheets are to be completed as applicable.
Return one copy to Barnes Pumps and store the second in
the control panel or with the pump manual if no control panel
is used. It is important to record this data at initial start-up
since it will be useful to refer to should servicing the pump be
required in the future.
D-3.1) Identification Plate:
Record the numbers from the pump’s identification plate on
both START-UP REPORTS provided at the end of the
manual for future reference.
SECTION E: SERVICE AND REPAIR
NOTE:
All item numbers in ( ) refer to Figures 6 & 7.
WARNING ! - Electrical power to the pump
motors must be disconnected and locked out to
prevent any dangerous electrical hazards or personnel
danger before any service work is done to the pump.
CAUTION ! - Operating pump builds up heat and
pressure; allow time for pump to cool to room
temperature before handling or servicing.
CAUTION ! - Always wear eye protection when
working on pumps.
E-1) Impeller ,Cutters and Volute Service:
E-1.1) Disassembly and Inspection:
To obtain access to the impeller (14) or shredding ring (16),
first remove screw (6) and washer (5). Then holding the motor
shaft stationary with a screwdriver, tap the radial cutter (4)
loose in the counter-clockwise direction and remove, (Heat
may be needed to break the screw (6) loose.) Next remove
nuts (21) and washers (9) from stud (22) and pull the body
(19) and square ring (20) from the rest of the pump. Now
impeller (14) can be removed by turning it counter-clockwise
while holding stationary the motor shaft with a screwdriver.
NOTE:
With the impeller (14) removed, the seal spring is
relaxed.
DO NOT
store this pump without the impeller (14) in
place to hold the seal shut.
To remove or reverse the shredding ring (16) first remove the
three flat head allen screws (18) and lift the throat (17) out of
the body (19). The shredding ring (16) is press fitted in the
body (19) and must be removed with an arbor press.
After a number of years of service or whenever the shredding
ring (16) cutting edges dull, the part can be pressed out of
the body (19) and reversed to utilize the opposite cutting
edges and replaced in the body (19).
7