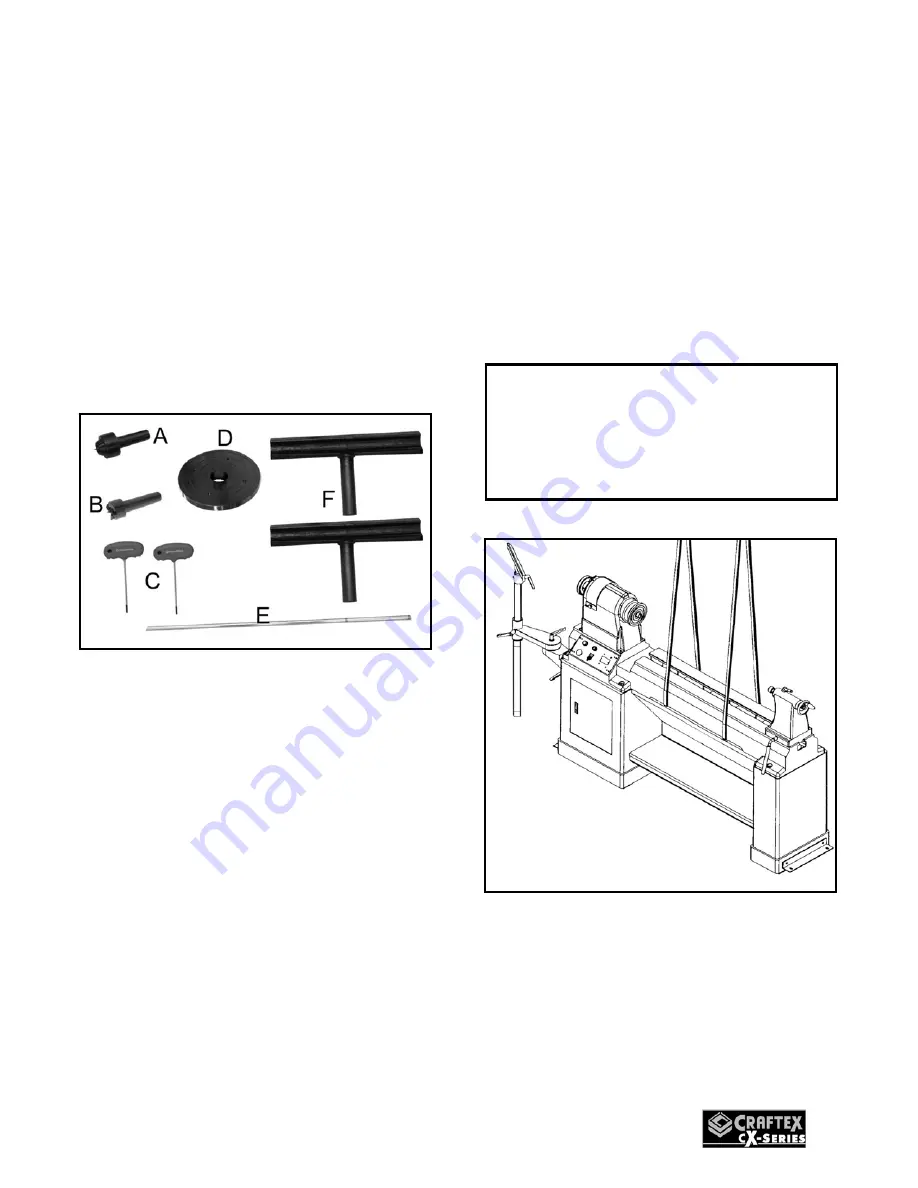
8
UNPACKING
The machine is properly packaged and
shipped complete in a crate for safe
transportation. When unpacking, carefully
inspect the crate to ensure that nothing has
been damaged during transit. Open the
crate and check that the lathe and the parts
are in good condition.
While doing inventory, if you can not find
any part, check if the part is already
installed on the machine. Some of the parts
come pre-assembled.
Figure-2 Inventory
LIST OF CONTENTS QTY
A.
Tailstock Center ..................................1
B.
Headstock Center................................1
C.
T-Handle Wrenches ............................2
D.
Faceplate ............................................1
E.
Knockout Rod......................................1
F.
Tool Rests ...........................................2
G.
Lathe (No Shown) ...............................1
SETUP
Before setting up your machine, you should
read and understand the instructions given
in this manual.
The unpainted surfaces of this lathe are
coated with rust preventive waxy oil and
you will want to remove this before you
begin assembly. Use a solvent cleaner that
will not damage the painted surfaces.
Figure-3 Lifting straps positioned to lift the
lathe
Figure-3 shows where to position the straps
to lift the lathe safely. Make sure when
lifting, the lathe is balance on both sides.
WARNING
CX800 is a very heavy machine. Do not
over-exert yourself. Use a fork truck or
other mechanical devices for safe
moving.
Summary of Contents for CX800
Page 1: ...CX800 43 X 20 HEAVY DUTY WOOD LATHE with VARIABLE SPEED User Manual ...
Page 6: ...6 CX800 HEAVY DUTY WOOD LATHE PHYSICAL FEATURES ...
Page 21: ...21 ...
Page 22: ...22 ...
Page 23: ...23 ...