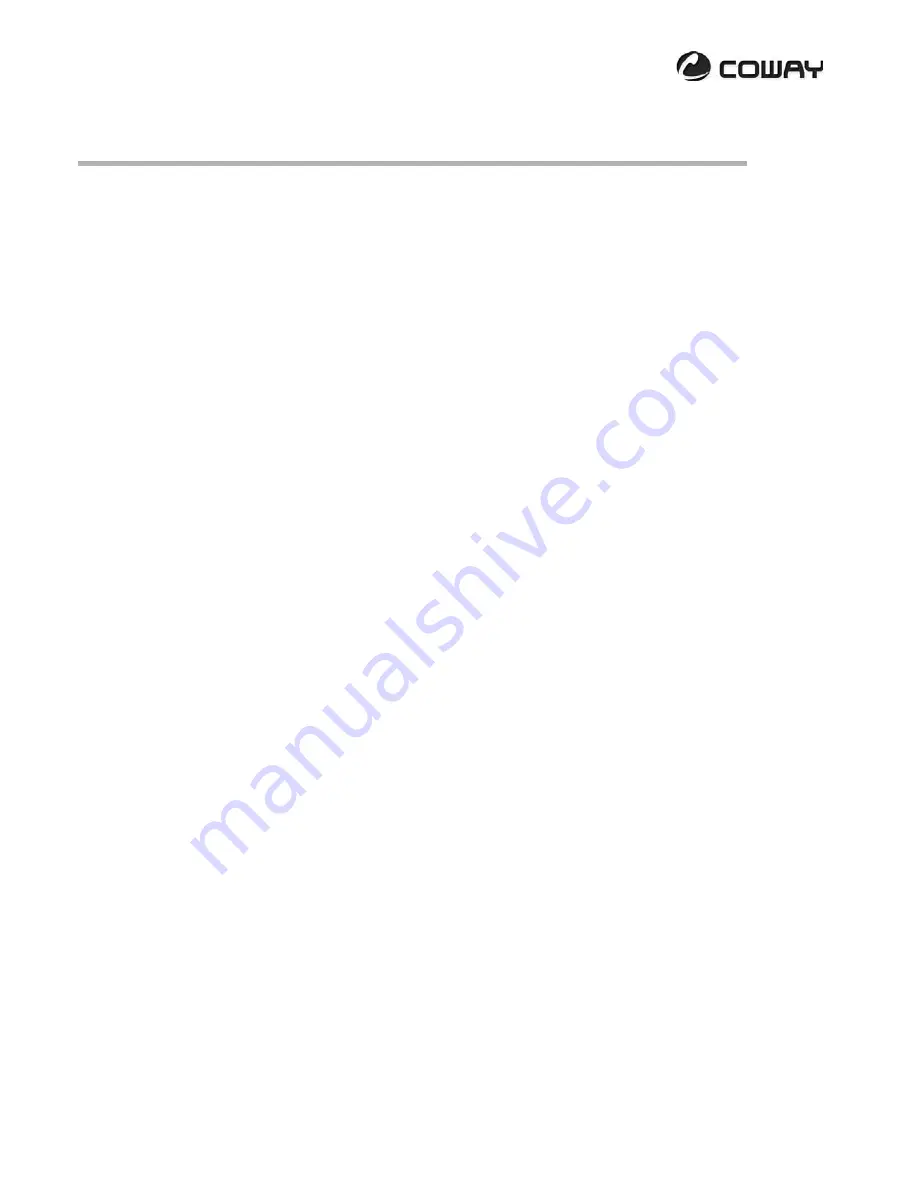
15
Specifications of Main Parts
1
Regulator
- Use
: It uniformly keeps the water pressure of the system inside.
- Operation Principle
: It keeps the pressure of supplying water under the setting
pressure by utilizing the spring tension.
3
Plus-Sediment Filter
- Material
: Polypropylene
- Feature
: By using a cartridge filter which has a stage-by-stage filtration method in
accordance with the size of pore, the early clogging condition of filter has been improved.
4
Pre-Carbon Filter
- Material
: 12 x 30 mesh by granular activated carbon of coconut.
- Feature
: It has an outstanding ability to reduce carcinogenic substance (THMs) and
organic chemical substance.
5
R/O Membrane Filter
- Capacity
: 50GPD on 25
℃
, 20psi
- Material
: Polyamide, Polysulfone
- Pore size
: 0.0001
μ
m
- Feature
: Various contaminating inorganic substances including bacteria and virus are
reduced through fine pores of 0.0001
㎛
in diameter.
6
Post-Carbon Filter
- Material
: 20 x 40 mesh by silver-added activated carbon of coconut.
- Feature
: It improves hygienic condition and taste of water by adding the silver- added
activated carbon to reduce odor in the water and prevent proliferation of microbe.
2
Thermistor
- Use
:
It controls the temperature of the cold water.
- Operation Principle
:
It controls the operation of compressor detecting the temperature of
the compressor by change of resistance that varies rapidly and predictably with temperature.
7
UV Lamp( Single body type )
- Material
: Quartz glass tube and pump
- Feature
: UV lamp circulates the treated water inside the reservoir tank so that it prevents
contamination inside it.
Summary of Contents for CHP-01AL
Page 1: ...0 A S...
Page 7: ...6 Names of Parts...
Page 8: ...7 Indication Parts Operating Parts...
Page 9: ...8 Wiring Diagram Water Flow Diagram...
Page 14: ...13 How to Use Water Spout...
Page 50: ...49 Harness Diagram...
Page 51: ...50 Harness Diagram...
Page 56: ...Installation Manual Saddle Valve Type Case 1...
Page 57: ...Installation Manual...