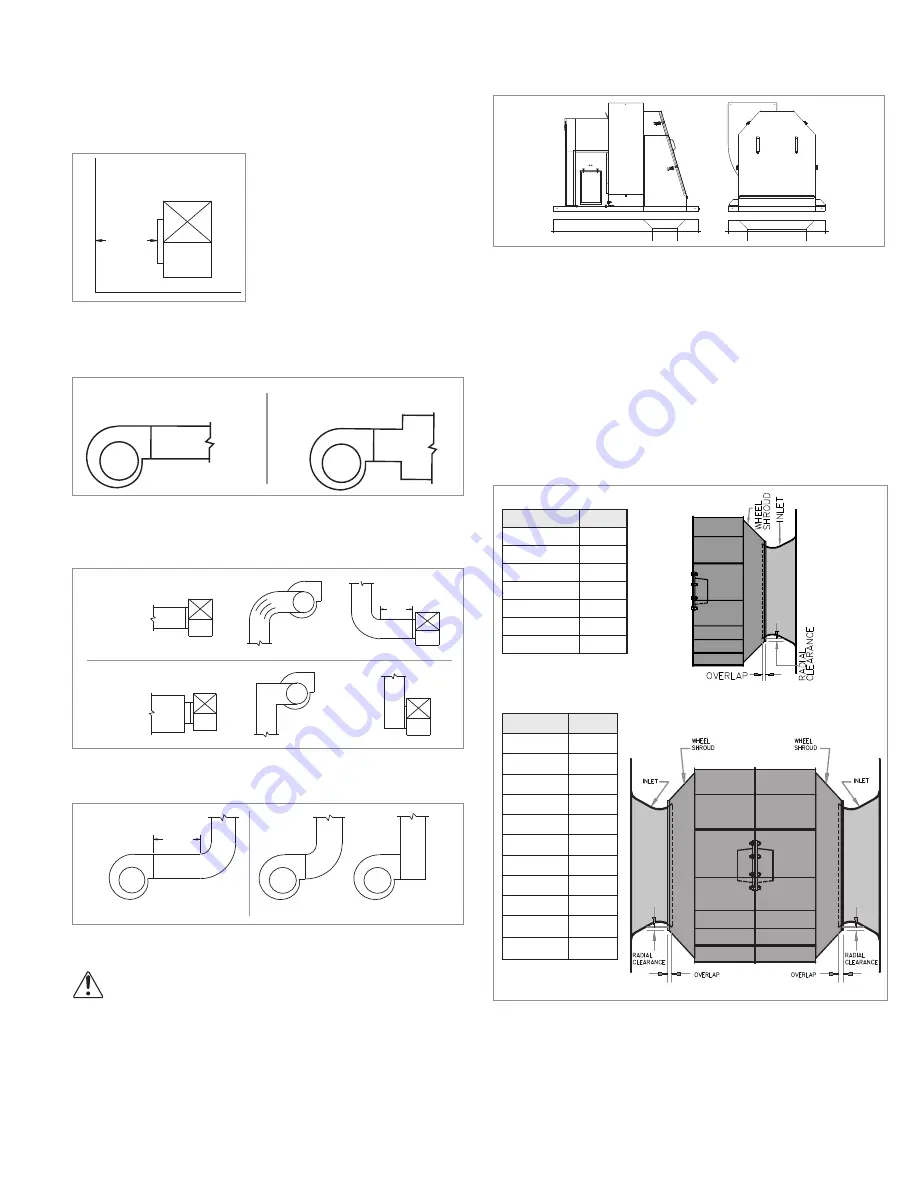
3
sealed with UL recognized fire caulk to both the curb cap
duct adapter and the bottom of the fan. A minimum of two
separate outlines of caulk is recommended at the outer
portion of the curb cap duct adapter.
Wheel-to-Inlet Clearance
The correct wheel-to-inlet clearance is critical to proper
fan performance. This clearance should be verified before
initial start-up since rough handling during shipment could
cause a shift in fan components. Refer to wheel/inlet draw-
ing for correct overlap.
Adjust the overlap by loosening the wheel hub and mov-
ing the wheel along the shaft to obtain the correct value.
A uniform radial gap (space between the edge of the
cone and the edge of the inlet) is obtained by loosening the
inlet cone bolts and repositioning the inlet cone.
CA, CF, & CP
CAF-DW
Size
Overlap
60 - 165
3/16”
180 - 245
1/4”
270 - 300
5/16”
330 - 365
3/8”
402
7/16”
445 - 490
1/2”
540 - 730
13/16”
Size
Overlap
120
1/8”
135 - 165
5/32”
180
1/4”
195
5/32”
210
1/4”
225
5/32”
245
9/32”
270 - 445
1/4”
490
17/32”
540 - 600
27/32”
660 - 730
25/32”
Duct Installation
Efficient fan performance relies on the proper installation
of inlet and discharge ducts. Be sure your fan conforms to
the following guidelines.
Non-Ducted Inlet Clearance:
If your fan has an open
inlet (no duct work), the fan must be placed 1 fan wheel
diameter away from walls and bulkheads.
Free Discharge:
Avoid a free discharge into the plenum.
This will result in lost efficiency because it doesn’t allow for
a static regain.
Inlet Duct Turns:
For ducted inlets, allow at least 3 fan
wheel diameters between duct turns or elbows and the
fan
inlet.
Discharge Duct Turns:
Where possible, allow 3 duct
diameters between duct turns or elbows and the fan outlet.
CP with Optional Curb Cap & Inlet Box
UL 762 / NFPA96 and local codes may dictate
additional or modifications to this installation.
The installation diagram below has a solid curb cap duct
adapter placed over the top of the curb. The welded grease
duct with recommended transition is either welded or
MIN 1 DIA
Correct
Incorrect
Correct
Incorrect
MIN 3
DIA
Correct
Incorrect
MIN 3
DIA
Summary of Contents for CA DWDI
Page 15: ...15...