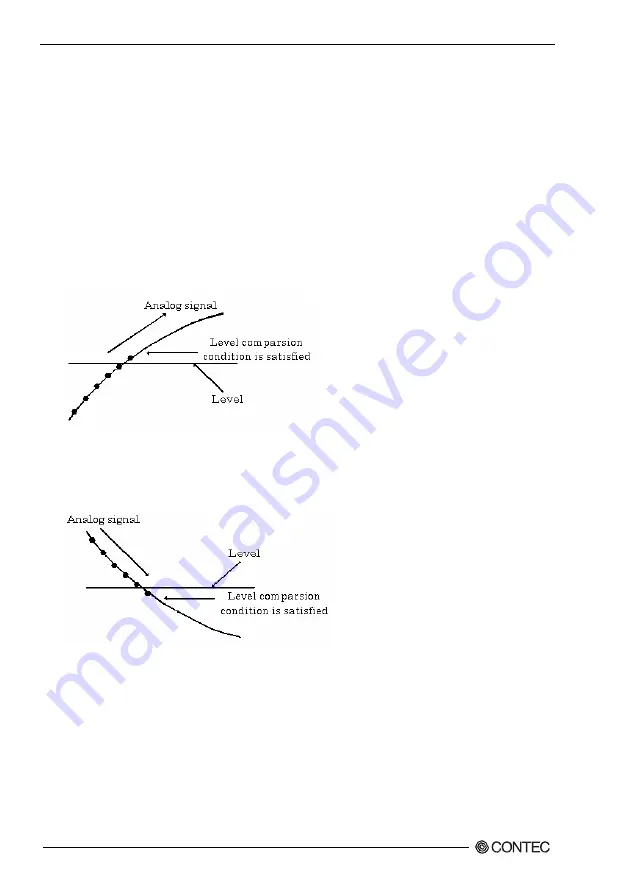
4. Functions
48
ADA16-32/2(PCI)F
Stop Condition
The condition for controlling the stop of sampling can be selected from among the last sampling count,
input data comparison, an external trigger, and software abort.
The board stops sampling whenever an error occurs irrespective of the stop condition setting.
-
Last sampling count
The board stops sampling after storing input data to memory for the specified number of times of
sampling.
- Input
data
comparison
Once the board has started sampling, it compares the analog signal input through a specified
channel to the value of the preset comparison level. If the analog signal satisfies the condition, the
board stops sampling.
Level comparison conditions are set as two conditions: level and direction.
The above sketch shows that the level comparison condition is satisfied in the rising direction.
The stop condition is satisfied when the analog signal at the specified channel passes the
comparison level in the rising direction. Input data items are stored to memory, ending until those
at solid dots.
The above sketch shows that the level comparison condition is satisfied in the falling direction.
The stop condition is satisfied when the analog signal at the specified channel passes the
comparison level in the falling direction. Input data items are stored to memory, ending until
those at solid dots
If you set the level comparison directions to both directions, the start condition is satisfied when the
analog signal passes the level both in the rising and falling directions.
Summary of Contents for ADA16-32/2(PCI)F
Page 7: ...vi ADA16 32 2 PCI F ...
Page 33: ...2 Setup 26 ADA16 32 2 PCI F ...
Page 45: ...3 External Connection 38 ADA16 32 2 PCI F ...
Page 99: ...5 About Software 92 ADA16 32 2 PCI F ...
Page 108: ......