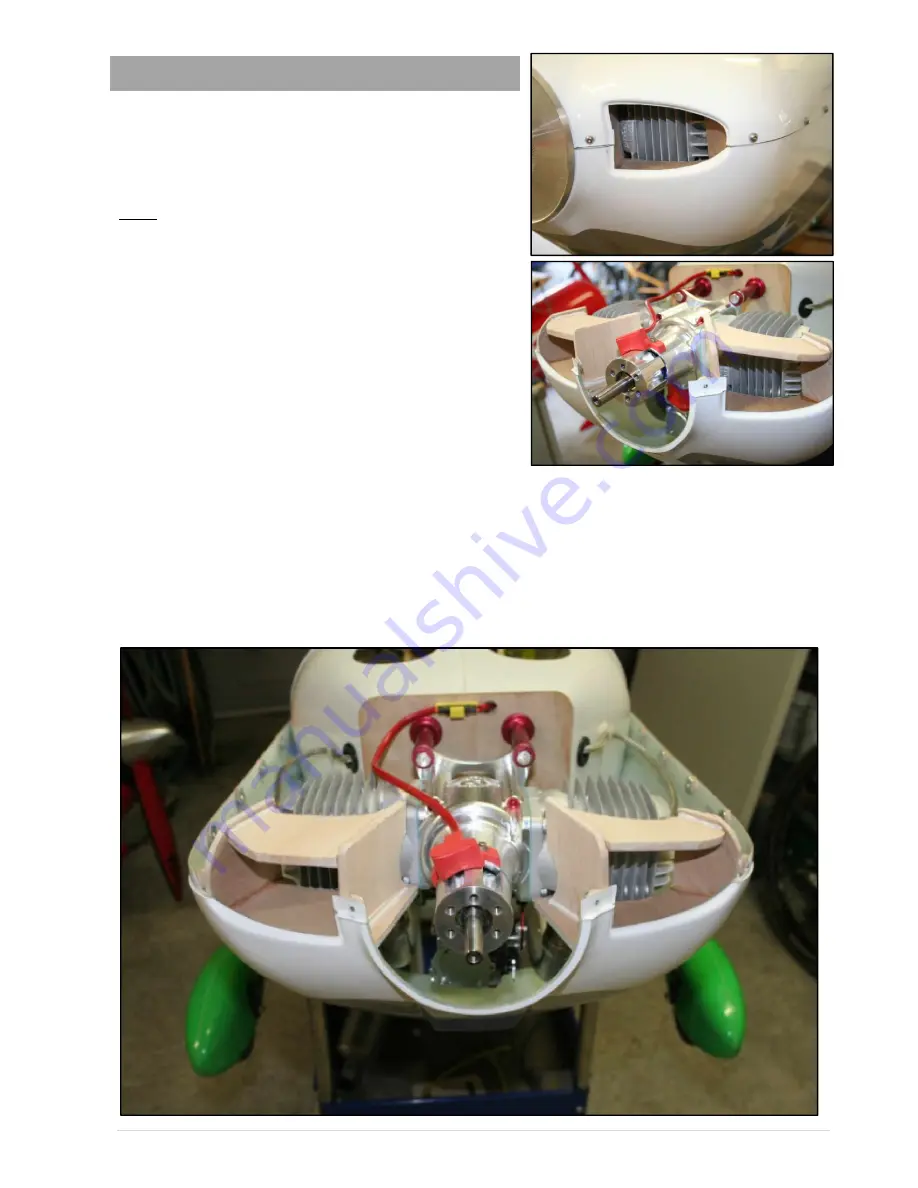
31 |
P a g e
Edge 540/2.6m
It is important to keep your engine cool, regardless of the engine
manufacturer. Keeping your engine cool is good practice, your
engine will like love for it! Another area you must also consider is
the fuselage. If you are running canisters or tuned pipes this is a
must!
We will show you how we ducted the air to the DA120 that we
used. Clearly with so many engine choices, it would be
impossible to cover all variations. But the principle is the same,
and the following is a good guideline for you to follow.
Remember, what we are trying to achieve, is to channel all the
incoming air from the two openings at the front of the cowl
directly onto the cylinder fins, before it can disburse or be forced
to other areas of the cowl. It’s important that your ducting
components are close to, but not touching your engine. About
2mm is sufficient.
We manufactured our ducting components from 4mm balsa and
0.5mm ply. The balsa is easily shaped to your requirements and is also very light. The ply is added as the top layer
when most of the shaping is done to add strength and a tough surface. Use some card to get the basic shape you
require, and then trace the shape onto the balsa. The thin ply can be easily cut with scissors and the final shape
trimmed with a sanding block. We used medium CA to glue the ply to the balsa.
Tack your components in place with some CA and kicker. Make sure you trial fit as you go. It is also a good idea to
bolt the upper part of the cowl in place from time to time just in case some of the components are getting fowled or
the lower cowl is getting slightly pulled out of shape. When you are satisfied with the fit epoxy the components in
place. While the epoxy is curing, reassemble the cowl and fit to the fuselage, so as everything stays in shape.
Engine cooling and vents