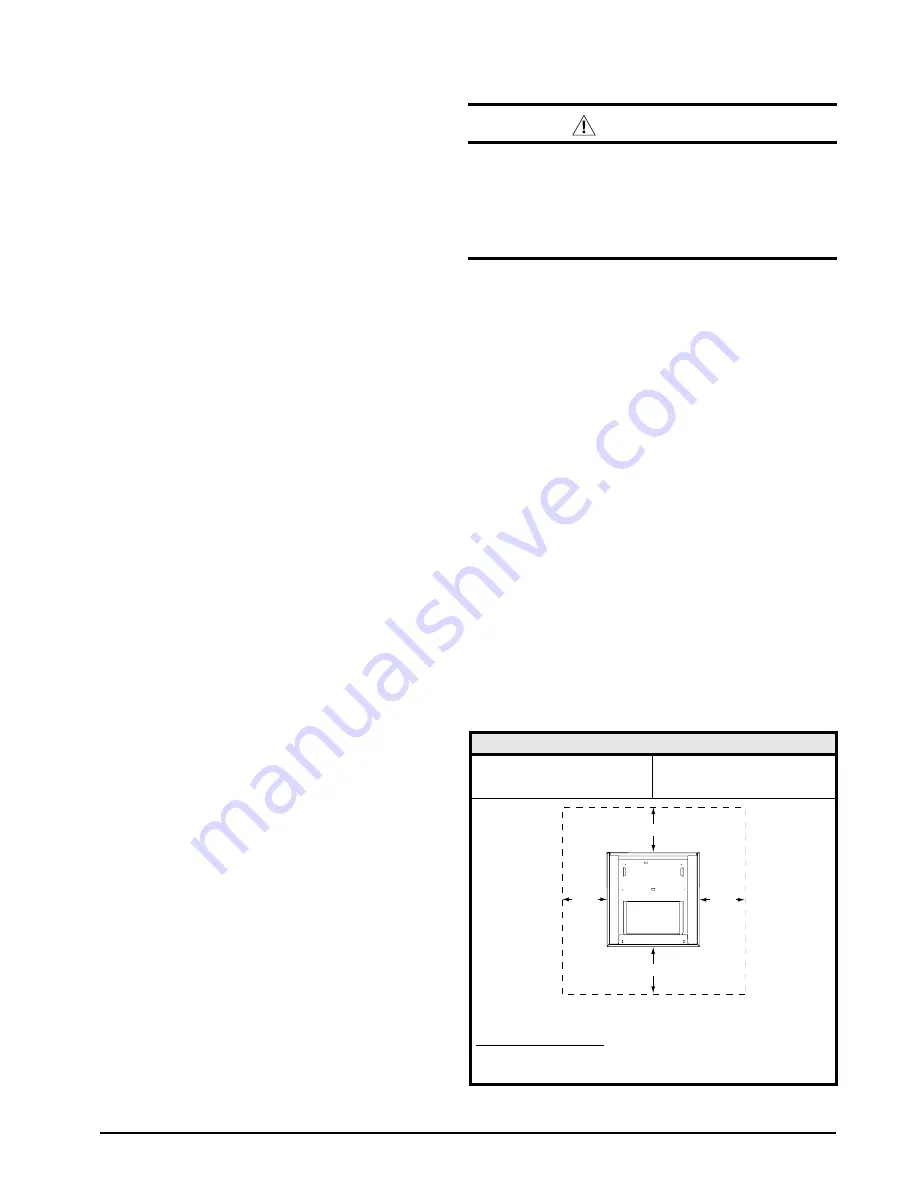
4
GENERAL INFORMATION
This appliance has been tested for capacity and efficiency
in accordance with AHRI Standards and will provide
many years of safe and dependable comfort, providing
it is properly installed and maintained. Abuse, improper
use, and/or improper maintenance can shorten the life
of the appliance and create unsafe hazards. Please read
all instructions before installing the unit.
Before You Install this Unit
√
This equipment is securely packaged at the time of
shipment and upon arrival should be carefully inspected
for damage prior to installing the equipment at the job
site. Claims for damage (apparent or concealed) should
be filed immediately with the carrier.
√
it is recommended that the cooling load of the area to
be conditioned should be calculated and a system of
the proper capacity selected.
√
Check the electrical supply and verify the power supply
is adequate for unit operation. The system must be wired
and provided with circuit protection in accordance with
local building codes. If there is any question concerning
the power supply, contact the local power company.
√
Verify the duct system is appropriate for the air handler
being installed. Please note that when replacing an
existing system with lower air-flow, the duct system
may require modification.
Locating the Air Handler
• Survey the job site to determine the best location for
mounting the unit. Consideration should be given to
availability of electric power, service access, and noise.
• The dimensions of the room or alcove must be able
to accommodate the overall size of the unit and the
installation clearances listed in Table 1. Physical
dimensions for this air handler are also shown in Figure
12 (page 17).
• The air handler should be set into position before routing
the refrigerant tubing.
Minimum Clearances
• This appliance must be installed in accordance with
clearances listed in Table 1. The air handler must be
installed with ample clearance for easy access to the
air filter, blower assembly, heater assembly, controls,
and vent connections. Applicable building codes may
require additional clearance to equipment. Refer to
applicable building codes for details.
• Static pressure drop through louvered openings and
through return air plenums should be considered in
the overall duct design in the determination of the total
external static pressure.
Table 1. Minimum Unit Clearances
INSTALLATION CLEARANCES
Left Side ......... 0 Inches Right Side ...... 0 Inches
Back ............... 0 Inches Front ...........
†
See Notes
†
NOTES:
Alcove Installations - Allow 24 in. minimum clearance
from front of unit to nearest wall or partition for servicing.
Recommended clearance is 36 in.
REAR
RIGHT
SIDE
LEFT
SIDE
FRONT
Operation of Air Handler During Construction
CAUTION:
Failure to follow these instructions will void the
factory warranty and may significantly reduce
the life or the performance of the air handler,
and/or result in other unsafe conditions. It is
the responsibility of the installing contractor
to insure these provisions are met.
Operating an air handler in a construction environment
can cause the appliance a variety of problems. Proper
use of commercial portable space heating equipment
during construction is recommended. This air handler
may be used during construction if it is not in violation of
any applicable codes and the following criteria are met:
• The installation must meet all applicable codes and
be permanently installed according to the instructions
supplied with the air handler including electrical supply
and duct work.
• The air handler must be controlled by a properly installed
thermostat that complies with the current provisions
of the NEC (ANSI/NFPA 70) and all applicable codes
having jurisdiction. Thermostat connections must be
made in accordance with instructions supplied with the
air handler and thermostat. See pages 11 - 12.
• The installation must include a properly installed filter in
the return air system with no by-pass air. The filter must
be inspected frequently and replaced when necessary.
• Return air must be supplied unrestricted and located
such that dust and gases from construction activity are
not introduced into the circulating air system.
• Before occupying the structure: The filter must be
replaced or cleaned, the duct work must be inspected
and cleaned of any construction debris, and the air