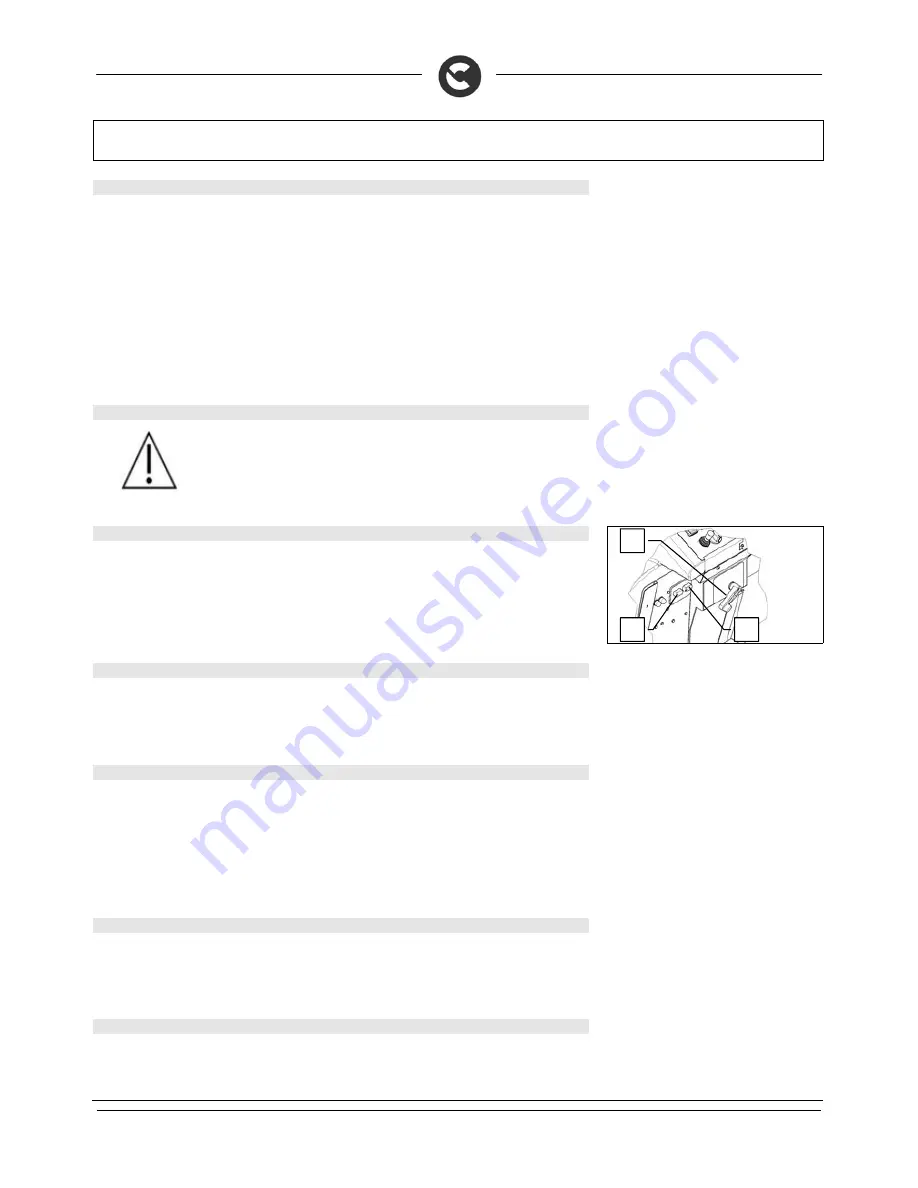
59
TROUBLESHOOTING
69.
THE MACHINE DOES NOT START
1.
Check the batteries are charged (battery version)
2.
Check the starter battery is charged (combustion engine version)
3.
Check the starter battery is connected to the machine system (combustion engine version)
4.
Check the electric system connector is connected to the battery connector (battery version)
5.
Check the electric system connector is connected to the generator connector (combustion engine
version)
6.
Check the key switch is ON/I
7.
Check there is fuel in the engine tank, and that the LPG cylinder is full (combustion engine version)
70.
THE COMBUSTION ENGINE DOES NOT START
WARNING: If the combustion engine does not start up, check the diagnostics
in the motor use and maintenance manual (the booklet supplied with the
machine itself).
71.
INSUFFICIENT WATER ON THE BRUSHES
1.
Check there is water in the solution tank
2.
Check that the water/detergent solution release adjustment lever (1) is open
3.
Check that the water/detergent selectors (2-3) are open (for CDS versions only)
4.
Clean the solution filter located at the front of the machine
5.
Make sure the detergent solution distribution tank (on the brush head unit) is not clogged
72.
THE SQUEEGEE DOES NOT DRY PERFECTLY
1.
Check the squeegee is clean
2.
Check the squeegee settings (see “MACHINE PREPARATION”)
3.
Clean the entire vacuum unit (see “WEEKLY MAINTENANCE”)
4.
Replace the rubbers, if worn
73.
THE MACHINE DOES NOT CLEAN WELL
1.
Check the state of wear and tear of the brushes and, if necessary, replace them. The brushes should
be changed when the bristles are about 15mm long. To replace them, see “REPLACING THE
BRUSHES”, or “DISASSEMBLING THE BRUSHES” and “ASSEMBLING THE BRUSHES”. Working
with over-worn brushes may cause damage to the floor
2.
Use a different kind of brush to the one fitted as standard. For cleaning floors where the dirt is
particularly resistant, we recommend the use of special brushes supplied upon request and according
to needs (see “CHOOSING AND USING THE BRUSHES”)
74.
EXCESSIVE FOAM PRODUCTION
Verify that a low foam detergent has been used. If necessary, add a small quantity of anti-foam liquid to the
recovery tank.
Remember that, when the floor is not very dirty, more foam is generated. In this case the detergent solution
should be more diluted.
75.
THE SUCTION MOTOR DOES NOT FUNCTION
1.
Check whether the recovery tank is full and, if necessary, empty it
2.
Check the float switch on the suction cap is working well (see also “CLEANING THE RECOVERY
TANK” under “DAILY MAINTENANCE”)
2
1
3