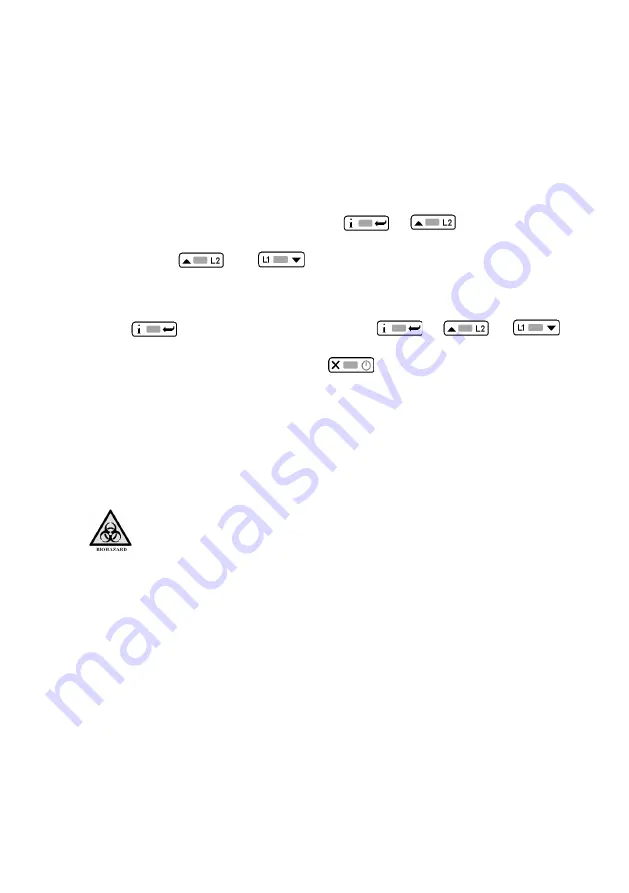
20
9.3. Servicing
This product should be serviced by a Antylia Scientific Service Engineer or by an agent
on behalf of Antylia Scientific Limited. If in doubt contact Antylia Scientific. See Section
11.
9.4. Calibration
9.4.1. Recalibration
• Have a precision reference thermometer of calibrator to hand. Ensure that OS1=0
and SIM = 0.
• Switch the controller off and on again.
• During the auto-test phase, press buttons + and keep them
pressed until the controlled shows 0AD.
• With buttons and selected 0AD or SAD; 0AD allows a calibration
of 0, inserting a constant corrective over the while scale of measurement. SAD allows
a calibration of the top part of the measurement scale with a proportional correction
between the calibration point and 0.
• Press to display the value and then use + or to
make the read value coincide with the value measured by the reference instrument.
• Exit from calibration by pressing button .
9.5. Spillage and Decontamination
In the event of spillage switch off and unplug this product from the mains electrical
supply. Wipe off all excess liquid from the unit and surrounding area using an
absorbent soft cloth.
If in doubt please consult Customer Support. Refer to section 11.
If the equipment has been exposed to contamination, the
Responsible Body is responsible for carrying out appropriatede
contamination. If hazardous material has been spilt on or inside the
equipment, decontamination should only be undertaken under the control of
the Responsible Body with due recognition of possible hazards. Before using
any cleaning or decontamination method, the Responsible Body should check
with the manufacturer the proposed method will not damage the equipment.
Prior to further use, the Responsible Body shall check the electrical safety of
the unit. Only if all safety requirements are met can the unit be used again.
The above procedure is intended as a guide. Should spillage occur with a toxic
or hazardous fluid then special precautions may be necessary.
Decontamination Certificate.
Note:
In the event of this equipment or any part of the unit becoming damaged, or
requiring service, the item(s) should be returned to the manufacturer for repair
accompanied by a completed decontamination certificate.
Copies of the Certificate
are available from Distributor/Manufacturer.
At the end of life, this product must be accompanied by a completed
Decontamination Certificate.
Page 12 of 24 M6493 Issue 10.3
7.3.3. Proportional, Integral and Derivative Control.
A proportional controller continuously adjusts the power, so the heat input to
the process is approximately in balance with the process heat requirements
in order to maintain a stable temperature. The range of temperature over
which power is adjusted is from 0% to 100%. This temperature range is
called the ‘Proportional Band’. The proportional band is adjustable for
differing process conditions (zero proportional band returns the controller to
basic on / off control).
The temperature difference between the stabilised temperature and the set
point is called the ‘Offset’. The offset can be reduced by adjusting the integral
term of the PID controller. This is achieved using the integrative action time
and integrative action reset.
A derivative function can be combined with the proportional controller to
provide the controller with the ability to shift the proportional band either up to
or down to compensate for rapidly changing temperature (i.e. when an oven
door is opened or cooler fluid is introduced into a controlled vessel). The
derivative function increases the controller gain during temperature changes,
and can help to reduce overshoot on start-up.
Hence, a three-mode PID controller combines the proportional, integral and
derivative actions, to allow the set point temperature to be approached
relatively smoothly with minimal overshoot.
7.4. Front Panel Controls
The MC810B controller has four front panel keys as described below.
7.4.1. The
key is used to increase the value of the parameter shown on
the display or to scroll through the parameter menu.
7.4.2. The
key is used to decrease the value of the parameter shown on
the display or to scroll through the parameter menu.
7.4.3. The
key is a dual function key. It is used to display and store the
value of the selected parameter when in ‘Programming’ mode. When used with
the
it is used to display the ‘Setpoint’ value.
7.4.4. The
is an ‘Exit / Stand-by button. Press of 3 seconds to turn unit on
or off.
7.5. Operating Modes.
7.5.1. The MB810B has two modes of operation: Function mode and Programming
mode. The unit enters Function mode immediately following power up in auto
test phase. In Function mode the display shows the temperature measured by
the temperature sensing probe. The output power will also be switched on or off
as appropriate. If the output power is on, the amber neon indicator on the front
panel will be illuminated. The only parameter which can be altered in the
function mode is the set-point. See 7.7.1
7.5.2. In Programming mode, all the other parameters apart from set-point can be
altered. To gain access to the programming mode from Function mode, press
the keys
and
. Keep them pressed for five seconds. The
output power is always off when in programming mode. If approximately 25
seconds elapse while in programming mode with out a key being pressed the
Page 12 of 24 M6493 Issue 10.3
7.3.3. Proportional, Integral and Derivative Control.
A proportional controller continuously adjusts the power, so the heat input to
the process is approximately in balance with the process heat requirements
in order to maintain a stable temperature. The range of temperature over
which power is adjusted is from 0% to 100%. This temperature range is
called the ‘Proportional Band’. The proportional band is adjustable for
differing process conditions (zero proportional band returns the controller to
basic on / off control).
The temperature difference between the stabilised temperature and the set
point is called the ‘Offset’. The offset can be reduced by adjusting the integral
term of the PID controller. This is achieved using the integrative action time
and integrative action reset.
A derivative function can be combined with the proportional controller to
provide the controller with the ability to shift the proportional band either up to
or down to compensate for rapidly changing temperature (i.e. when an oven
door is opened or cooler fluid is introduced into a controlled vessel). The
derivative function increases the controller gain during temperature changes,
and can help to reduce overshoot on start-up.
Hence, a three-mode PID controller combines the proportional, integral and
derivative actions, to allow the set point temperature to be approached
relatively smoothly with minimal overshoot.
7.4. Front Panel Controls
The MC810B controller has four front panel keys as described below.
7.4.1. The
key is used to increase the value of the parameter shown on
the display or to scroll through the parameter menu.
7.4.2. The
key is used to decrease the value of the parameter shown on
the display or to scroll through the parameter menu.
7.4.3. The
key is a dual function key. It is used to display and store the
value of the selected parameter when in ‘Programming’ mode. When used with
the
it is used to display the ‘Setpoint’ value.
7.4.4. The
is an ‘Exit / Stand-by button. Press of 3 seconds to turn unit on
or off.
7.5. Operating Modes.
7.5.1. The MB810B has two modes of operation: Function mode and Programming
mode. The unit enters Function mode immediately following power up in auto
test phase. In Function mode the display shows the temperature measured by
the temperature sensing probe. The output power will also be switched on or off
as appropriate. If the output power is on, the amber neon indicator on the front
panel will be illuminated. The only parameter which can be altered in the
function mode is the set-point. See 7.7.1
7.5.2. In Programming mode, all the other parameters apart from set-point can be
altered. To gain access to the programming mode from Function mode, press
the keys
and
. Keep them pressed for five seconds. The
output power is always off when in programming mode. If approximately 25
seconds elapse while in programming mode with out a key being pressed the
Page 12 of 24 M6493 Issue 10.3
7.3.3. Proportional, Integral and Derivative Control.
A proportional controller continuously adjusts the power, so the heat input to
the process is approximately in balance with the process heat requirements
in order to maintain a stable temperature. The range of temperature over
which power is adjusted is from 0% to 100%. This temperature range is
called the ‘Proportional Band’. The proportional band is adjustable for
differing process conditions (zero proportional band returns the controller to
basic on / off control).
The temperature difference between the stabilised temperature and the set
point is called the ‘Offset’. The offset can be reduced by adjusting the integral
term of the PID controller. This is achieved using the integrative action time
and integrative action reset.
A derivative function can be combined with the proportional controller to
provide the controller with the ability to shift the proportional band either up to
or down to compensate for rapidly changing temperature (i.e. when an oven
door is opened or cooler fluid is introduced into a controlled vessel). The
derivative function increases the controller gain during temperature changes,
and can help to reduce overshoot on start-up.
Hence, a three-mode PID controller combines the proportional, integral and
derivative actions, to allow the set point temperature to be approached
relatively smoothly with minimal overshoot.
7.4. Front Panel Controls
The MC810B controller has four front panel keys as described below.
7.4.1. The
key is used to increase the value of the parameter shown on
the display or to scroll through the parameter menu.
7.4.2. The
key is used to decrease the value of the parameter shown on
the display or to scroll through the parameter menu.
7.4.3. The
key is a dual function key. It is used to display and store the
value of the selected parameter when in ‘Programming’ mode. When used with
the
it is used to display the ‘Setpoint’ value.
7.4.4. The
is an ‘Exit / Stand-by button. Press of 3 seconds to turn unit on
or off.
7.5. Operating Modes.
7.5.1. The MB810B has two modes of operation: Function mode and Programming
mode. The unit enters Function mode immediately following power up in auto
test phase. In Function mode the display shows the temperature measured by
the temperature sensing probe. The output power will also be switched on or off
as appropriate. If the output power is on, the amber neon indicator on the front
panel will be illuminated. The only parameter which can be altered in the
function mode is the set-point. See 7.7.1
7.5.2. In Programming mode, all the other parameters apart from set-point can be
altered. To gain access to the programming mode from Function mode, press
the keys
and
. Keep them pressed for five seconds. The
output power is always off when in programming mode. If approximately 25
seconds elapse while in programming mode with out a key being pressed the
Page 12 of 24 M6493 Issue 10.3
7.3.3. Proportional, Integral and Derivative Control.
A proportional controller continuously adjusts the power, so the heat input to
the process is approximately in balance with the process heat requirements
in order to maintain a stable temperature. The range of temperature over
which power is adjusted is from 0% to 100%. This temperature range is
called the ‘Proportional Band’. The proportional band is adjustable for
differing process conditions (zero proportional band returns the controller to
basic on / off control).
The temperature difference between the stabilised temperature and the set
point is called the ‘Offset’. The offset can be reduced by adjusting the integral
term of the PID controller. This is achieved using the integrative action time
and integrative action reset.
A derivative function can be combined with the proportional controller to
provide the controller with the ability to shift the proportional band either up to
or down to compensate for rapidly changing temperature (i.e. when an oven
door is opened or cooler fluid is introduced into a controlled vessel). The
derivative function increases the controller gain during temperature changes,
and can help to reduce overshoot on start-up.
Hence, a three-mode PID controller combines the proportional, integral and
derivative actions, to allow the set point temperature to be approached
relatively smoothly with minimal overshoot.
7.4. Front Panel Controls
The MC810B controller has four front panel keys as described below.
7.4.1. The
key is used to increase the value of the parameter shown on
the display or to scroll through the parameter menu.
7.4.2. The
key is used to decrease the value of the parameter shown on
the display or to scroll through the parameter menu.
7.4.3. The
key is a dual function key. It is used to display and store the
value of the selected parameter when in ‘Programming’ mode. When used with
the
it is used to display the ‘Setpoint’ value.
7.4.4. The
is an ‘Exit / Stand-by button. Press of 3 seconds to turn unit on
or off.
7.5. Operating Modes.
7.5.1. The MB810B has two modes of operation: Function mode and Programming
mode. The unit enters Function mode immediately following power up in auto
test phase. In Function mode the display shows the temperature measured by
the temperature sensing probe. The output power will also be switched on or off
as appropriate. If the output power is on, the amber neon indicator on the front
panel will be illuminated. The only parameter which can be altered in the
function mode is the set-point. See 7.7.1
7.5.2. In Programming mode, all the other parameters apart from set-point can be
altered. To gain access to the programming mode from Function mode, press
the keys
and
. Keep them pressed for five seconds. The
output power is always off when in programming mode. If approximately 25
seconds elapse while in programming mode with out a key being pressed the
Page 12 of 24 M6493 Issue 10.3
7.3.3. Proportional, Integral and Derivative Control.
A proportional controller continuously adjusts the power, so the heat input to
the process is approximately in balance with the process heat requirements
in order to maintain a stable temperature. The range of temperature over
which power is adjusted is from 0% to 100%. This temperature range is
called the ‘Proportional Band’. The proportional band is adjustable for
differing process conditions (zero proportional band returns the controller to
basic on / off control).
The temperature difference between the stabilised temperature and the set
point is called the ‘Offset’. The offset can be reduced by adjusting the integral
term of the PID controller. This is achieved using the integrative action time
and integrative action reset.
A derivative function can be combined with the proportional controller to
provide the controller with the ability to shift the proportional band either up to
or down to compensate for rapidly changing temperature (i.e. when an oven
door is opened or cooler fluid is introduced into a controlled vessel). The
derivative function increases the controller gain during temperature changes,
and can help to reduce overshoot on start-up.
Hence, a three-mode PID controller combines the proportional, integral and
derivative actions, to allow the set point temperature to be approached
relatively smoothly with minimal overshoot.
7.4. Front Panel Controls
The MC810B controller has four front panel keys as described below.
7.4.1. The
key is used to increase the value of the parameter shown on
the display or to scroll through the parameter menu.
7.4.2. The
key is used to decrease the value of the parameter shown on
the display or to scroll through the parameter menu.
7.4.3. The
key is a dual function key. It is used to display and store the
value of the selected parameter when in ‘Programming’ mode. When used with
the
it is used to display the ‘Setpoint’ value.
7.4.4. The
is an ‘Exit / Stand-by button. Press of 3 seconds to turn unit on
or off.
7.5. Operating Modes.
7.5.1. The MB810B has two modes of operation: Function mode and Programming
mode. The unit enters Function mode immediately following power up in auto
test phase. In Function mode the display shows the temperature measured by
the temperature sensing probe. The output power will also be switched on or off
as appropriate. If the output power is on, the amber neon indicator on the front
panel will be illuminated. The only parameter which can be altered in the
function mode is the set-point. See 7.7.1
7.5.2. In Programming mode, all the other parameters apart from set-point can be
altered. To gain access to the programming mode from Function mode, press
the keys
and
. Keep them pressed for five seconds. The
output power is always off when in programming mode. If approximately 25
seconds elapse while in programming mode with out a key being pressed the
Page 12 of 24 M6493 Issue 10.3
7.3.3. Proportional, Integral and Derivative Control.
A proportional controller continuously adjusts the power, so the heat input to
the process is approximately in balance with the process heat requirements
in order to maintain a stable temperature. The range of temperature over
which power is adjusted is from 0% to 100%. This temperature range is
called the ‘Proportional Band’. The proportional band is adjustable for
differing process conditions (zero proportional band returns the controller to
basic on / off control).
The temperature difference between the stabilised temperature and the set
point is called the ‘Offset’. The offset can be reduced by adjusting the integral
term of the PID controller. This is achieved using the integrative action time
and integrative action reset.
A derivative function can be combined with the proportional controller to
provide the controller with the ability to shift the proportional band either up to
or down to compensate for rapidly changing temperature (i.e. when an oven
door is opened or cooler fluid is introduced into a controlled vessel). The
derivative function increases the controller gain during temperature changes,
and can help to reduce overshoot on start-up.
Hence, a three-mode PID controller combines the proportional, integral and
derivative actions, to allow the set point temperature to be approached
relatively smoothly with minimal overshoot.
7.4. Front Panel Controls
The MC810B controller has four front panel keys as described below.
7.4.1. The
key is used to increase the value of the parameter shown on
the display or to scroll through the parameter menu.
7.4.2. The
key is used to decrease the value of the parameter shown on
the display or to scroll through the parameter menu.
7.4.3. The
key is a dual function key. It is used to display and store the
value of the selected parameter when in ‘Programming’ mode. When used with
the
it is used to display the ‘Setpoint’ value.
7.4.4. The
is an ‘Exit / Stand-by button. Press of 3 seconds to turn unit on
or off.
7.5. Operating Modes.
7.5.1. The MB810B has two modes of operation: Function mode and Programming
mode. The unit enters Function mode immediately following power up in auto
test phase. In Function mode the display shows the temperature measured by
the temperature sensing probe. The output power will also be switched on or off
as appropriate. If the output power is on, the amber neon indicator on the front
panel will be illuminated. The only parameter which can be altered in the
function mode is the set-point. See 7.7.1
7.5.2. In Programming mode, all the other parameters apart from set-point can be
altered. To gain access to the programming mode from Function mode, press
the keys
and
. Keep them pressed for five seconds. The
output power is always off when in programming mode. If approximately 25
seconds elapse while in programming mode with out a key being pressed the
Page 12 of 24 M6493 Issue 10.3
7.3.3. Proportional, Integral and Derivative Control.
A proportional controller continuously adjusts the power, so the heat input to
the process is approximately in balance with the process heat requirements
in order to maintain a stable temperature. The range of temperature over
which power is adjusted is from 0% to 100%. This temperature range is
called the ‘Proportional Band’. The proportional band is adjustable for
differing process conditions (zero proportional band returns the controller to
basic on / off control).
The temperature difference between the stabilised temperature and the set
point is called the ‘Offset’. The offset can be reduced by adjusting the integral
term of the PID controller. This is achieved using the integrative action time
and integrative action reset.
A derivative function can be combined with the proportional controller to
provide the controller with the ability to shift the proportional band either up to
or down to compensate for rapidly changing temperature (i.e. when an oven
door is opened or cooler fluid is introduced into a controlled vessel). The
derivative function increases the controller gain during temperature changes,
and can help to reduce overshoot on start-up.
Hence, a three-mode PID controller combines the proportional, integral and
derivative actions, to allow the set point temperature to be approached
relatively smoothly with minimal overshoot.
7.4. Front Panel Controls
The MC810B controller has four front panel keys as described below.
7.4.1. The
key is used to increase the value of the parameter shown on
the display or to scroll through the parameter menu.
7.4.2. The
key is used to decrease the value of the parameter shown on
the display or to scroll through the parameter menu.
7.4.3. The
key is a dual function key. It is used to display and store the
value of the selected parameter when in ‘Programming’ mode. When used with
the
it is used to display the ‘Setpoint’ value.
7.4.4. The
is an ‘Exit / Stand-by button. Press of 3 seconds to turn unit on
or off.
7.5. Operating Modes.
7.5.1. The MB810B has two modes of operation: Function mode and Programming
mode. The unit enters Function mode immediately following power up in auto
test phase. In Function mode the display shows the temperature measured by
the temperature sensing probe. The output power will also be switched on or off
as appropriate. If the output power is on, the amber neon indicator on the front
panel will be illuminated. The only parameter which can be altered in the
function mode is the set-point. See 7.7.1
7.5.2. In Programming mode, all the other parameters apart from set-point can be
altered. To gain access to the programming mode from Function mode, press
the keys
and
. Keep them pressed for five seconds. The
output power is always off when in programming mode. If approximately 25
seconds elapse while in programming mode with out a key being pressed the
Page 12 of 24 M6493 Issue 10.3
7.3.3. Proportional, Integral and Derivative Control.
A proportional controller continuously adjusts the power, so the heat input to
the process is approximately in balance with the process heat requirements
in order to maintain a stable temperature. The range of temperature over
which power is adjusted is from 0% to 100%. This temperature range is
called the ‘Proportional Band’. The proportional band is adjustable for
differing process conditions (zero proportional band returns the controller to
basic on / off control).
The temperature difference between the stabilised temperature and the set
point is called the ‘Offset’. The offset can be reduced by adjusting the integral
term of the PID controller. This is achieved using the integrative action time
and integrative action reset.
A derivative function can be combined with the proportional controller to
provide the controller with the ability to shift the proportional band either up to
or down to compensate for rapidly changing temperature (i.e. when an oven
door is opened or cooler fluid is introduced into a controlled vessel). The
derivative function increases the controller gain during temperature changes,
and can help to reduce overshoot on start-up.
Hence, a three-mode PID controller combines the proportional, integral and
derivative actions, to allow the set point temperature to be approached
relatively smoothly with minimal overshoot.
7.4. Front Panel Controls
The MC810B controller has four front panel keys as described below.
7.4.1. The
key is used to increase the value of the parameter shown on
the display or to scroll through the parameter menu.
7.4.2. The
key is used to decrease the value of the parameter shown on
the display or to scroll through the parameter menu.
7.4.3. The
key is a dual function key. It is used to display and store the
value of the selected parameter when in ‘Programming’ mode. When used with
the
it is used to display the ‘Setpoint’ value.
7.4.4. The
is an ‘Exit / Stand-by button. Press of 3 seconds to turn unit on
or off.
7.5. Operating Modes.
7.5.1. The MB810B has two modes of operation: Function mode and Programming
mode. The unit enters Function mode immediately following power up in auto
test phase. In Function mode the display shows the temperature measured by
the temperature sensing probe. The output power will also be switched on or off
as appropriate. If the output power is on, the amber neon indicator on the front
panel will be illuminated. The only parameter which can be altered in the
function mode is the set-point. See 7.7.1
7.5.2. In Programming mode, all the other parameters apart from set-point can be
altered. To gain access to the programming mode from Function mode, press
the keys
and
. Keep them pressed for five seconds. The
output power is always off when in programming mode. If approximately 25
seconds elapse while in programming mode with out a key being pressed the
Page 20 of 24 M6493 Issue 10.3
9.3. Servicing.
This product should be serviced by a Bibby Scientific Service Engineer or by an agent
on behalf of Bibby Scientific l. If in doubt contact Bibby Scientific. See Section 10.
9.4. Calibration
9.4.1. Recalibration
•
Have a precision reference thermometer of calibrator to hand. Ensure that
OS1=0 and SIM=0
•
Switch the controller off and on again.
•
During the auto-test phase, press buttons button’s
+
and
keep them pressed until the controlled shows 0AD.
•
With buttons
and
selected 0AD or SAD;0AD allows a
calibration of 0, inserting a constant corrective over the while scale of
measurement. SAD allows a calibration of the top part of the measurement
scale with a proportional correction between the calibration point and 0
•
Press
o display the value and then use
+
or
to make the read value coincide with the value measured by the
reference instrument.
•
Exit from calibration by pressing button
.
9.5. Spillage and Decontamination.
In the event of spillage switch off and unplug this product from the mains electrical
supply. Wipe off all excess liquid from the unit and surrounding area using an
absorbent soft cloth.
If in doubt please consult Customer Support. Refer to section 10.
If the equipment has been exposed to contamination, the
Responsible Body is responsible for carrying out appropriate
decontamination. If hazardous material has been spilt on or inside the
equipment, decontamination should only be undertaken under the control of
the Responsible Body with due recognition of possible hazards. Before using
any cleaning or decontamination method, the Responsible Body should check
with the manufacturer the proposed method will not damage the equipment.
Prior to further use, the Responsible Body shall check the electrical safety of
the unit. Only if all safety requirements are met can the unit be used again. The
above procedure is intended as a guide. Should spillage occur with a toxic or
hazardous fluid then special precautions may be necessary.
Decontamination Certificate.
Note: In the event of this equipment or any part of the unit becoming damaged, or
requiring service, the item(s) should be returned to the manufacturer for repair
accompanied by a decontamination certificate.
Copies of the Certificate are
available from Distributor/Manufacturer. Appendix A of this instructions book
may be copied and enlarged.
At the end of life, this product must be accompanied by a Decontamination
Certificate. See section 6.3 and 6.4
If in doubt please consult Customer support. Refer to section 10.
Page 12 of 24 M6493 Issue 10.3
7.3.3. Proportional, Integral and Derivative Control.
A proportional controller continuously adjusts the power, so the heat input to
the process is approximately in balance with the process heat requirements
in order to maintain a stable temperature. The range of temperature over
which power is adjusted is from 0% to 100%. This temperature range is
called the ‘Proportional Band’. The proportional band is adjustable for
differing process conditions (zero proportional band returns the controller to
basic on / off control).
The temperature difference between the stabilised temperature and the set
point is called the ‘Offset’. The offset can be reduced by adjusting the integral
term of the PID controller. This is achieved using the integrative action time
and integrative action reset.
A derivative function can be combined with the proportional controller to
provide the controller with the ability to shift the proportional band either up to
or down to compensate for rapidly changing temperature (i.e. when an oven
door is opened or cooler fluid is introduced into a controlled vessel). The
derivative function increases the controller gain during temperature changes,
and can help to reduce overshoot on start-up.
Hence, a three-mode PID controller combines the proportional, integral and
derivative actions, to allow the set point temperature to be approached
relatively smoothly with minimal overshoot.
7.4. Front Panel Controls
The MC810B controller has four front panel keys as described below.
7.4.1. The
key is used to increase the value of the parameter shown on
the display or to scroll through the parameter menu.
7.4.2. The
key is used to decrease the value of the parameter shown on
the display or to scroll through the parameter menu.
7.4.3. The
key is a dual function key. It is used to display and store the
value of the selected parameter when in ‘Programming’ mode. When used with
the
it is used to display the ‘Setpoint’ value.
7.4.4. The
is an ‘Exit / Stand-by button. Press of 3 seconds to turn unit on
or off.
7.5. Operating Modes.
7.5.1. The MB810B has two modes of operation: Function mode and Programming
mode. The unit enters Function mode immediately following power up in auto
test phase. In Function mode the display shows the temperature measured by
the temperature sensing probe. The output power will also be switched on or off
as appropriate. If the output power is on, the amber neon indicator on the front
panel will be illuminated. The only parameter which can be altered in the
function mode is the set-point. See 7.7.1
7.5.2. In Programming mode, all the other parameters apart from set-point can be
altered. To gain access to the programming mode from Function mode, press
the keys
and
. Keep them pressed for five seconds. The
output power is always off when in programming mode. If approximately 25
seconds elapse while in programming mode with out a key being pressed the