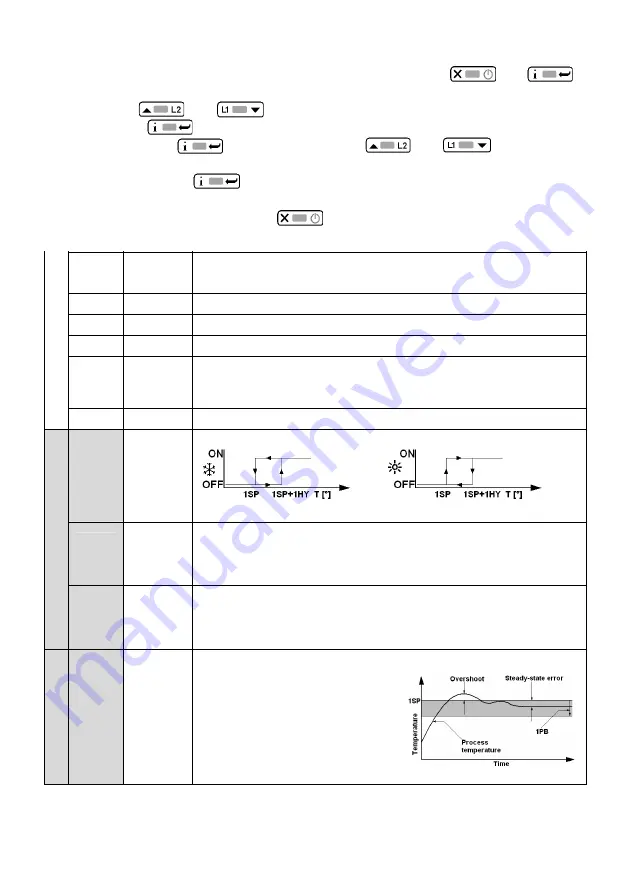
7.11. Configuring Parameters.
7.11.1. To select the parameter, enter Programming mode by pressing and
button for 5 seconds.
Use the and buttons to select the parameter for modification.
Press the button to display the value.
By keeping the button pressed, use the and buttons to set
the desired value.
When the button is release, the newly programmed value will be stored.
The newly programmed value is stored and the following parameter is displayed.
To exit from the setup, press the or wait for 30 seconds.
15
Page 12 of 24 M6493 Issue 10.3
7.3.3. Proportional, Integral and Derivative Control.
A proportional controller continuously adjusts the power, so the heat input to
the process is approximately in balance with the process heat requirements
in order to maintain a stable temperature. The range of temperature over
which power is adjusted is from 0% to 100%. This temperature range is
called the ‘Proportional Band’. The proportional band is adjustable for
differing process conditions (zero proportional band returns the controller to
basic on / off control).
The temperature difference between the stabilised temperature and the set
point is called the ‘Offset’. The offset can be reduced by adjusting the integral
term of the PID controller. This is achieved using the integrative action time
and integrative action reset.
A derivative function can be combined with the proportional controller to
provide the controller with the ability to shift the proportional band either up to
or down to compensate for rapidly changing temperature (i.e. when an oven
door is opened or cooler fluid is introduced into a controlled vessel). The
derivative function increases the controller gain during temperature changes,
and can help to reduce overshoot on start-up.
Hence, a three-mode PID controller combines the proportional, integral and
derivative actions, to allow the set point temperature to be approached
relatively smoothly with minimal overshoot.
7.4. Front Panel Controls
The MC810B controller has four front panel keys as described below.
7.4.1. The
key is used to increase the value of the parameter shown on
the display or to scroll through the parameter menu.
7.4.2. The
key is used to decrease the value of the parameter shown on
the display or to scroll through the parameter menu.
7.4.3. The
key is a dual function key. It is used to display and store the
value of the selected parameter when in ‘Programming’ mode. When used with
the
it is used to display the ‘Setpoint’ value.
7.4.4. The
is an ‘Exit / Stand-by button. Press of 3 seconds to turn unit on
or off.
7.5. Operating Modes.
7.5.1. The MB810B has two modes of operation: Function mode and Programming
mode. The unit enters Function mode immediately following power up in auto
test phase. In Function mode the display shows the temperature measured by
the temperature sensing probe. The output power will also be switched on or off
as appropriate. If the output power is on, the amber neon indicator on the front
panel will be illuminated. The only parameter which can be altered in the
function mode is the set-point. See 7.7.1
7.5.2. In Programming mode, all the other parameters apart from set-point can be
altered. To gain access to the programming mode from Function mode, press
the keys
and
. Keep them pressed for five seconds. The
output power is always off when in programming mode. If approximately 25
seconds elapse while in programming mode with out a key being pressed the
Page 12 of 24 M6493 Issue 10.3
7.3.3. Proportional, Integral and Derivative Control.
A proportional controller continuously adjusts the power, so the heat input to
the process is approximately in balance with the process heat requirements
in order to maintain a stable temperature. The range of temperature over
which power is adjusted is from 0% to 100%. This temperature range is
called the ‘Proportional Band’. The proportional band is adjustable for
differing process conditions (zero proportional band returns the controller to
basic on / off control).
The temperature difference between the stabilised temperature and the set
point is called the ‘Offset’. The offset can be reduced by adjusting the integral
term of the PID controller. This is achieved using the integrative action time
and integrative action reset.
A derivative function can be combined with the proportional controller to
provide the controller with the ability to shift the proportional band either up to
or down to compensate for rapidly changing temperature (i.e. when an oven
door is opened or cooler fluid is introduced into a controlled vessel). The
derivative function increases the controller gain during temperature changes,
and can help to reduce overshoot on start-up.
Hence, a three-mode PID controller combines the proportional, integral and
derivative actions, to allow the set point temperature to be approached
relatively smoothly with minimal overshoot.
7.4. Front Panel Controls
The MC810B controller has four front panel keys as described below.
7.4.1. The
key is used to increase the value of the parameter shown on
the display or to scroll through the parameter menu.
7.4.2. The
key is used to decrease the value of the parameter shown on
the display or to scroll through the parameter menu.
7.4.3. The
key is a dual function key. It is used to display and store the
value of the selected parameter when in ‘Programming’ mode. When used with
the
it is used to display the ‘Setpoint’ value.
7.4.4. The
is an ‘Exit / Stand-by button. Press of 3 seconds to turn unit on
or off.
7.5. Operating Modes.
7.5.1. The MB810B has two modes of operation: Function mode and Programming
mode. The unit enters Function mode immediately following power up in auto
test phase. In Function mode the display shows the temperature measured by
the temperature sensing probe. The output power will also be switched on or off
as appropriate. If the output power is on, the amber neon indicator on the front
panel will be illuminated. The only parameter which can be altered in the
function mode is the set-point. See 7.7.1
7.5.2. In Programming mode, all the other parameters apart from set-point can be
altered. To gain access to the programming mode from Function mode, press
the keys
and
. Keep them pressed for five seconds. The
output power is always off when in programming mode. If approximately 25
seconds elapse while in programming mode with out a key being pressed the
Page 12 of 24 M6493 Issue 10.3
7.3.3. Proportional, Integral and Derivative Control.
A proportional controller continuously adjusts the power, so the heat input to
the process is approximately in balance with the process heat requirements
in order to maintain a stable temperature. The range of temperature over
which power is adjusted is from 0% to 100%. This temperature range is
called the ‘Proportional Band’. The proportional band is adjustable for
differing process conditions (zero proportional band returns the controller to
basic on / off control).
The temperature difference between the stabilised temperature and the set
point is called the ‘Offset’. The offset can be reduced by adjusting the integral
term of the PID controller. This is achieved using the integrative action time
and integrative action reset.
A derivative function can be combined with the proportional controller to
provide the controller with the ability to shift the proportional band either up to
or down to compensate for rapidly changing temperature (i.e. when an oven
door is opened or cooler fluid is introduced into a controlled vessel). The
derivative function increases the controller gain during temperature changes,
and can help to reduce overshoot on start-up.
Hence, a three-mode PID controller combines the proportional, integral and
derivative actions, to allow the set point temperature to be approached
relatively smoothly with minimal overshoot.
7.4. Front Panel Controls
The MC810B controller has four front panel keys as described below.
7.4.1. The
key is used to increase the value of the parameter shown on
the display or to scroll through the parameter menu.
7.4.2. The
key is used to decrease the value of the parameter shown on
the display or to scroll through the parameter menu.
7.4.3. The
key is a dual function key. It is used to display and store the
value of the selected parameter when in ‘Programming’ mode. When used with
the
it is used to display the ‘Setpoint’ value.
7.4.4. The
is an ‘Exit / Stand-by button. Press of 3 seconds to turn unit on
or off.
7.5. Operating Modes.
7.5.1. The MB810B has two modes of operation: Function mode and Programming
mode. The unit enters Function mode immediately following power up in auto
test phase. In Function mode the display shows the temperature measured by
the temperature sensing probe. The output power will also be switched on or off
as appropriate. If the output power is on, the amber neon indicator on the front
panel will be illuminated. The only parameter which can be altered in the
function mode is the set-point. See 7.7.1
7.5.2. In Programming mode, all the other parameters apart from set-point can be
altered. To gain access to the programming mode from Function mode, press
the keys
and
. Keep them pressed for five seconds. The
output power is always off when in programming mode. If approximately 25
seconds elapse while in programming mode with out a key being pressed the
Page 12 of 24 M6493 Issue 10.3
7.3.3. Proportional, Integral and Derivative Control.
A proportional controller continuously adjusts the power, so the heat input to
the process is approximately in balance with the process heat requirements
in order to maintain a stable temperature. The range of temperature over
which power is adjusted is from 0% to 100%. This temperature range is
called the ‘Proportional Band’. The proportional band is adjustable for
differing process conditions (zero proportional band returns the controller to
basic on / off control).
The temperature difference between the stabilised temperature and the set
point is called the ‘Offset’. The offset can be reduced by adjusting the integral
term of the PID controller. This is achieved using the integrative action time
and integrative action reset.
A derivative function can be combined with the proportional controller to
provide the controller with the ability to shift the proportional band either up to
or down to compensate for rapidly changing temperature (i.e. when an oven
door is opened or cooler fluid is introduced into a controlled vessel). The
derivative function increases the controller gain during temperature changes,
and can help to reduce overshoot on start-up.
Hence, a three-mode PID controller combines the proportional, integral and
derivative actions, to allow the set point temperature to be approached
relatively smoothly with minimal overshoot.
7.4. Front Panel Controls
The MC810B controller has four front panel keys as described below.
7.4.1. The
key is used to increase the value of the parameter shown on
the display or to scroll through the parameter menu.
7.4.2. The
key is used to decrease the value of the parameter shown on
the display or to scroll through the parameter menu.
7.4.3. The
key is a dual function key. It is used to display and store the
value of the selected parameter when in ‘Programming’ mode. When used with
the
it is used to display the ‘Setpoint’ value.
7.4.4. The
is an ‘Exit / Stand-by button. Press of 3 seconds to turn unit on
or off.
7.5. Operating Modes.
7.5.1. The MB810B has two modes of operation: Function mode and Programming
mode. The unit enters Function mode immediately following power up in auto
test phase. In Function mode the display shows the temperature measured by
the temperature sensing probe. The output power will also be switched on or off
as appropriate. If the output power is on, the amber neon indicator on the front
panel will be illuminated. The only parameter which can be altered in the
function mode is the set-point. See 7.7.1
7.5.2. In Programming mode, all the other parameters apart from set-point can be
altered. To gain access to the programming mode from Function mode, press
the keys
and
. Keep them pressed for five seconds. The
output power is always off when in programming mode. If approximately 25
seconds elapse while in programming mode with out a key being pressed the
Page 12 of 24 M6493 Issue 10.3
7.3.3. Proportional, Integral and Derivative Control.
A proportional controller continuously adjusts the power, so the heat input to
the process is approximately in balance with the process heat requirements
in order to maintain a stable temperature. The range of temperature over
which power is adjusted is from 0% to 100%. This temperature range is
called the ‘Proportional Band’. The proportional band is adjustable for
differing process conditions (zero proportional band returns the controller to
basic on / off control).
The temperature difference between the stabilised temperature and the set
point is called the ‘Offset’. The offset can be reduced by adjusting the integral
term of the PID controller. This is achieved using the integrative action time
and integrative action reset.
A derivative function can be combined with the proportional controller to
provide the controller with the ability to shift the proportional band either up to
or down to compensate for rapidly changing temperature (i.e. when an oven
door is opened or cooler fluid is introduced into a controlled vessel). The
derivative function increases the controller gain during temperature changes,
and can help to reduce overshoot on start-up.
Hence, a three-mode PID controller combines the proportional, integral and
derivative actions, to allow the set point temperature to be approached
relatively smoothly with minimal overshoot.
7.4. Front Panel Controls
The MC810B controller has four front panel keys as described below.
7.4.1. The
key is used to increase the value of the parameter shown on
the display or to scroll through the parameter menu.
7.4.2. The
key is used to decrease the value of the parameter shown on
the display or to scroll through the parameter menu.
7.4.3. The
key is a dual function key. It is used to display and store the
value of the selected parameter when in ‘Programming’ mode. When used with
the
it is used to display the ‘Setpoint’ value.
7.4.4. The
is an ‘Exit / Stand-by button. Press of 3 seconds to turn unit on
or off.
7.5. Operating Modes.
7.5.1. The MB810B has two modes of operation: Function mode and Programming
mode. The unit enters Function mode immediately following power up in auto
test phase. In Function mode the display shows the temperature measured by
the temperature sensing probe. The output power will also be switched on or off
as appropriate. If the output power is on, the amber neon indicator on the front
panel will be illuminated. The only parameter which can be altered in the
function mode is the set-point. See 7.7.1
7.5.2. In Programming mode, all the other parameters apart from set-point can be
altered. To gain access to the programming mode from Function mode, press
the keys
and
. Keep them pressed for five seconds. The
output power is always off when in programming mode. If approximately 25
seconds elapse while in programming mode with out a key being pressed the
Page 12 of 24 M6493 Issue 10.3
7.3.3. Proportional, Integral and Derivative Control.
A proportional controller continuously adjusts the power, so the heat input to
the process is approximately in balance with the process heat requirements
in order to maintain a stable temperature. The range of temperature over
which power is adjusted is from 0% to 100%. This temperature range is
called the ‘Proportional Band’. The proportional band is adjustable for
differing process conditions (zero proportional band returns the controller to
basic on / off control).
The temperature difference between the stabilised temperature and the set
point is called the ‘Offset’. The offset can be reduced by adjusting the integral
term of the PID controller. This is achieved using the integrative action time
and integrative action reset.
A derivative function can be combined with the proportional controller to
provide the controller with the ability to shift the proportional band either up to
or down to compensate for rapidly changing temperature (i.e. when an oven
door is opened or cooler fluid is introduced into a controlled vessel). The
derivative function increases the controller gain during temperature changes,
and can help to reduce overshoot on start-up.
Hence, a three-mode PID controller combines the proportional, integral and
derivative actions, to allow the set point temperature to be approached
relatively smoothly with minimal overshoot.
7.4. Front Panel Controls
The MC810B controller has four front panel keys as described below.
7.4.1. The
key is used to increase the value of the parameter shown on
the display or to scroll through the parameter menu.
7.4.2. The
key is used to decrease the value of the parameter shown on
the display or to scroll through the parameter menu.
7.4.3. The
key is a dual function key. It is used to display and store the
value of the selected parameter when in ‘Programming’ mode. When used with
the
it is used to display the ‘Setpoint’ value.
7.4.4. The
is an ‘Exit / Stand-by button. Press of 3 seconds to turn unit on
or off.
7.5. Operating Modes.
7.5.1. The MB810B has two modes of operation: Function mode and Programming
mode. The unit enters Function mode immediately following power up in auto
test phase. In Function mode the display shows the temperature measured by
the temperature sensing probe. The output power will also be switched on or off
as appropriate. If the output power is on, the amber neon indicator on the front
panel will be illuminated. The only parameter which can be altered in the
function mode is the set-point. See 7.7.1
7.5.2. In Programming mode, all the other parameters apart from set-point can be
altered. To gain access to the programming mode from Function mode, press
the keys
and
. Keep them pressed for five seconds. The
output power is always off when in programming mode. If approximately 25
seconds elapse while in programming mode with out a key being pressed the
Page 12 of 24 M6493 Issue 10.3
7.3.3. Proportional, Integral and Derivative Control.
A proportional controller continuously adjusts the power, so the heat input to
the process is approximately in balance with the process heat requirements
in order to maintain a stable temperature. The range of temperature over
which power is adjusted is from 0% to 100%. This temperature range is
called the ‘Proportional Band’. The proportional band is adjustable for
differing process conditions (zero proportional band returns the controller to
basic on / off control).
The temperature difference between the stabilised temperature and the set
point is called the ‘Offset’. The offset can be reduced by adjusting the integral
term of the PID controller. This is achieved using the integrative action time
and integrative action reset.
A derivative function can be combined with the proportional controller to
provide the controller with the ability to shift the proportional band either up to
or down to compensate for rapidly changing temperature (i.e. when an oven
door is opened or cooler fluid is introduced into a controlled vessel). The
derivative function increases the controller gain during temperature changes,
and can help to reduce overshoot on start-up.
Hence, a three-mode PID controller combines the proportional, integral and
derivative actions, to allow the set point temperature to be approached
relatively smoothly with minimal overshoot.
7.4. Front Panel Controls
The MC810B controller has four front panel keys as described below.
7.4.1. The
key is used to increase the value of the parameter shown on
the display or to scroll through the parameter menu.
7.4.2. The
key is used to decrease the value of the parameter shown on
the display or to scroll through the parameter menu.
7.4.3. The
key is a dual function key. It is used to display and store the
value of the selected parameter when in ‘Programming’ mode. When used with
the
it is used to display the ‘Setpoint’ value.
7.4.4. The
is an ‘Exit / Stand-by button. Press of 3 seconds to turn unit on
or off.
7.5. Operating Modes.
7.5.1. The MB810B has two modes of operation: Function mode and Programming
mode. The unit enters Function mode immediately following power up in auto
test phase. In Function mode the display shows the temperature measured by
the temperature sensing probe. The output power will also be switched on or off
as appropriate. If the output power is on, the amber neon indicator on the front
panel will be illuminated. The only parameter which can be altered in the
function mode is the set-point. See 7.7.1
7.5.2. In Programming mode, all the other parameters apart from set-point can be
altered. To gain access to the programming mode from Function mode, press
the keys
and
. Keep them pressed for five seconds. The
output power is always off when in programming mode. If approximately 25
seconds elapse while in programming mode with out a key being pressed the
Page 12 of 24 M6493 Issue 10.3
7.3.3. Proportional, Integral and Derivative Control.
A proportional controller continuously adjusts the power, so the heat input to
the process is approximately in balance with the process heat requirements
in order to maintain a stable temperature. The range of temperature over
which power is adjusted is from 0% to 100%. This temperature range is
called the ‘Proportional Band’. The proportional band is adjustable for
differing process conditions (zero proportional band returns the controller to
basic on / off control).
The temperature difference between the stabilised temperature and the set
point is called the ‘Offset’. The offset can be reduced by adjusting the integral
term of the PID controller. This is achieved using the integrative action time
and integrative action reset.
A derivative function can be combined with the proportional controller to
provide the controller with the ability to shift the proportional band either up to
or down to compensate for rapidly changing temperature (i.e. when an oven
door is opened or cooler fluid is introduced into a controlled vessel). The
derivative function increases the controller gain during temperature changes,
and can help to reduce overshoot on start-up.
Hence, a three-mode PID controller combines the proportional, integral and
derivative actions, to allow the set point temperature to be approached
relatively smoothly with minimal overshoot.
7.4. Front Panel Controls
The MC810B controller has four front panel keys as described below.
7.4.1. The
key is used to increase the value of the parameter shown on
the display or to scroll through the parameter menu.
7.4.2. The
key is used to decrease the value of the parameter shown on
the display or to scroll through the parameter menu.
7.4.3. The
key is a dual function key. It is used to display and store the
value of the selected parameter when in ‘Programming’ mode. When used with
the
it is used to display the ‘Setpoint’ value.
7.4.4. The
is an ‘Exit / Stand-by button. Press of 3 seconds to turn unit on
or off.
7.5. Operating Modes.
7.5.1. The MB810B has two modes of operation: Function mode and Programming
mode. The unit enters Function mode immediately following power up in auto
test phase. In Function mode the display shows the temperature measured by
the temperature sensing probe. The output power will also be switched on or off
as appropriate. If the output power is on, the amber neon indicator on the front
panel will be illuminated. The only parameter which can be altered in the
function mode is the set-point. See 7.7.1
7.5.2. In Programming mode, all the other parameters apart from set-point can be
altered. To gain access to the programming mode from Function mode, press
the keys
and
. Keep them pressed for five seconds. The
output power is always off when in programming mode. If approximately 25
seconds elapse while in programming mode with out a key being pressed the
Page 12 of 24 M6493 Issue 10.3
7.3.3. Proportional, Integral and Derivative Control.
A proportional controller continuously adjusts the power, so the heat input to
the process is approximately in balance with the process heat requirements
in order to maintain a stable temperature. The range of temperature over
which power is adjusted is from 0% to 100%. This temperature range is
called the ‘Proportional Band’. The proportional band is adjustable for
differing process conditions (zero proportional band returns the controller to
basic on / off control).
The temperature difference between the stabilised temperature and the set
point is called the ‘Offset’. The offset can be reduced by adjusting the integral
term of the PID controller. This is achieved using the integrative action time
and integrative action reset.
A derivative function can be combined with the proportional controller to
provide the controller with the ability to shift the proportional band either up to
or down to compensate for rapidly changing temperature (i.e. when an oven
door is opened or cooler fluid is introduced into a controlled vessel). The
derivative function increases the controller gain during temperature changes,
and can help to reduce overshoot on start-up.
Hence, a three-mode PID controller combines the proportional, integral and
derivative actions, to allow the set point temperature to be approached
relatively smoothly with minimal overshoot.
7.4. Front Panel Controls
The MC810B controller has four front panel keys as described below.
7.4.1. The
key is used to increase the value of the parameter shown on
the display or to scroll through the parameter menu.
7.4.2. The
key is used to decrease the value of the parameter shown on
the display or to scroll through the parameter menu.
7.4.3. The
key is a dual function key. It is used to display and store the
value of the selected parameter when in ‘Programming’ mode. When used with
the
it is used to display the ‘Setpoint’ value.
7.4.4. The
is an ‘Exit / Stand-by button. Press of 3 seconds to turn unit on
or off.
7.5. Operating Modes.
7.5.1. The MB810B has two modes of operation: Function mode and Programming
mode. The unit enters Function mode immediately following power up in auto
test phase. In Function mode the display shows the temperature measured by
the temperature sensing probe. The output power will also be switched on or off
as appropriate. If the output power is on, the amber neon indicator on the front
panel will be illuminated. The only parameter which can be altered in the
function mode is the set-point. See 7.7.1
7.5.2. In Programming mode, all the other parameters apart from set-point can be
altered. To gain access to the programming mode from Function mode, press
the keys
and
. Keep them pressed for five seconds. The
output power is always off when in programming mode. If approximately 25
seconds elapse while in programming mode with out a key being pressed the
Page 15 of 24
M6493 Issue 10.3
7.11.
Configuring Parameters.
7.11.1.
To select the parameter, enter Programming mode press
and
button for 5 seconds.
Use the
and
buttons to select the parameter for modification.
Press the
button to display the value.
By keeping the
button pressed, use the
and
buttons to
set the desired value.
When the
button is release, the newly programmed value will be stored.
The newly programmed value is stored and the following parameter is displayed.
To exit from the setup, press the
or wait for 30 seconds.
PAR
RANGE
DESCRIPTION
SCL
1°C;
2°C;
°F
Read out scale (see Input Specification table on page 17)
Caution: upon changing the SCL value, it is the absolutely necessary to reconfigure the
parameters relevant to the absolute and relative temperatures (SPL, SPH, 1SP, 1HY etc.).
SPL
-50°..SPH
Minimum limit for 1SP setting.
SPH
SPL..150°C
Maximum limit for 1SP setting.
1SP
SPL..SPH
Set-point (value to be maintained in the room).
1CM
HY;PID
Control mode.
With 1CM=HY you select control with hysteresis: parameters 1HY, 1T0 and 1T1 are used.
With 1CM=PD you select a Proportional-Integral-Derivative control mode: parameters 1PB, 1IT,
1DT, 1AR, 1CT will be used.
1CH
REF;HEAS
Refrigerating (REF) or Heating (HEA) control mode.
1
CM
=
H
Y
1HY
0…19.9°C
OFF/ON thermostat differential. With 1HY =
0 the output is always off.
1TO
0…30min
Minimum off time.
After output 1 has been turned off’ it remains inactive for 1TO minutes regardless of the
temperature value measured.
1T1
0…30 min
Minimum on time. (The following parameter will be 1PF).
After output 1 has been turned on, it remains active for 1T1 minutes regardless of the
temperature value measured.
1
C
M
=
P
ID
1PB
0.19.0°C
Proportional bandwidth.
Temperature control takes place by changing the
ON time to the output: the closer the temperature
to the set-point, the less time to activate. A small
proportional band increases the promptness of the
response of the system to temperature variations,
but tends to make it less stable. A purely
proportional control stabilises the temperature
within the proportional band but does not cancel
the deviation from the set-point.
With
1PB=0
the output is always off.
On/Off heating control
(
1CM
= HY,
1CH
+ HEA).
On/Off refrigeration control
(
1CM
= HY,
1CH
+ REF).
Page 12 of 24 M6493 Issue 10.3
7.3.3. Proportional, Integral and Derivative Control.
A proportional controller continuously adjusts the power, so the heat input to
the process is approximately in balance with the process heat requirements
in order to maintain a stable temperature. The range of temperature over
which power is adjusted is from 0% to 100%. This temperature range is
called the ‘Proportional Band’. The proportional band is adjustable for
differing process conditions (zero proportional band returns the controller to
basic on / off control).
The temperature difference between the stabilised temperature and the set
point is called the ‘Offset’. The offset can be reduced by adjusting the integral
term of the PID controller. This is achieved using the integrative action time
and integrative action reset.
A derivative function can be combined with the proportional controller to
provide the controller with the ability to shift the proportional band either up to
or down to compensate for rapidly changing temperature (i.e. when an oven
door is opened or cooler fluid is introduced into a controlled vessel). The
derivative function increases the controller gain during temperature changes,
and can help to reduce overshoot on start-up.
Hence, a three-mode PID controller combines the proportional, integral and
derivative actions, to allow the set point temperature to be approached
relatively smoothly with minimal overshoot.
7.4. Front Panel Controls
The MC810B controller has four front panel keys as described below.
7.4.1. The
key is used to increase the value of the parameter shown on
the display or to scroll through the parameter menu.
7.4.2. The
key is used to decrease the value of the parameter shown on
the display or to scroll through the parameter menu.
7.4.3. The
key is a dual function key. It is used to display and store the
value of the selected parameter when in ‘Programming’ mode. When used with
the
it is used to display the ‘Setpoint’ value.
7.4.4. The
is an ‘Exit / Stand-by button. Press of 3 seconds to turn unit on
or off.
7.5. Operating Modes.
7.5.1. The MB810B has two modes of operation: Function mode and Programming
mode. The unit enters Function mode immediately following power up in auto
test phase. In Function mode the display shows the temperature measured by
the temperature sensing probe. The output power will also be switched on or off
as appropriate. If the output power is on, the amber neon indicator on the front
panel will be illuminated. The only parameter which can be altered in the
function mode is the set-point. See 7.7.1
7.5.2. In Programming mode, all the other parameters apart from set-point can be
altered. To gain access to the programming mode from Function mode, press
the keys
and
. Keep them pressed for five seconds. The
output power is always off when in programming mode. If approximately 25
seconds elapse while in programming mode with out a key being pressed the