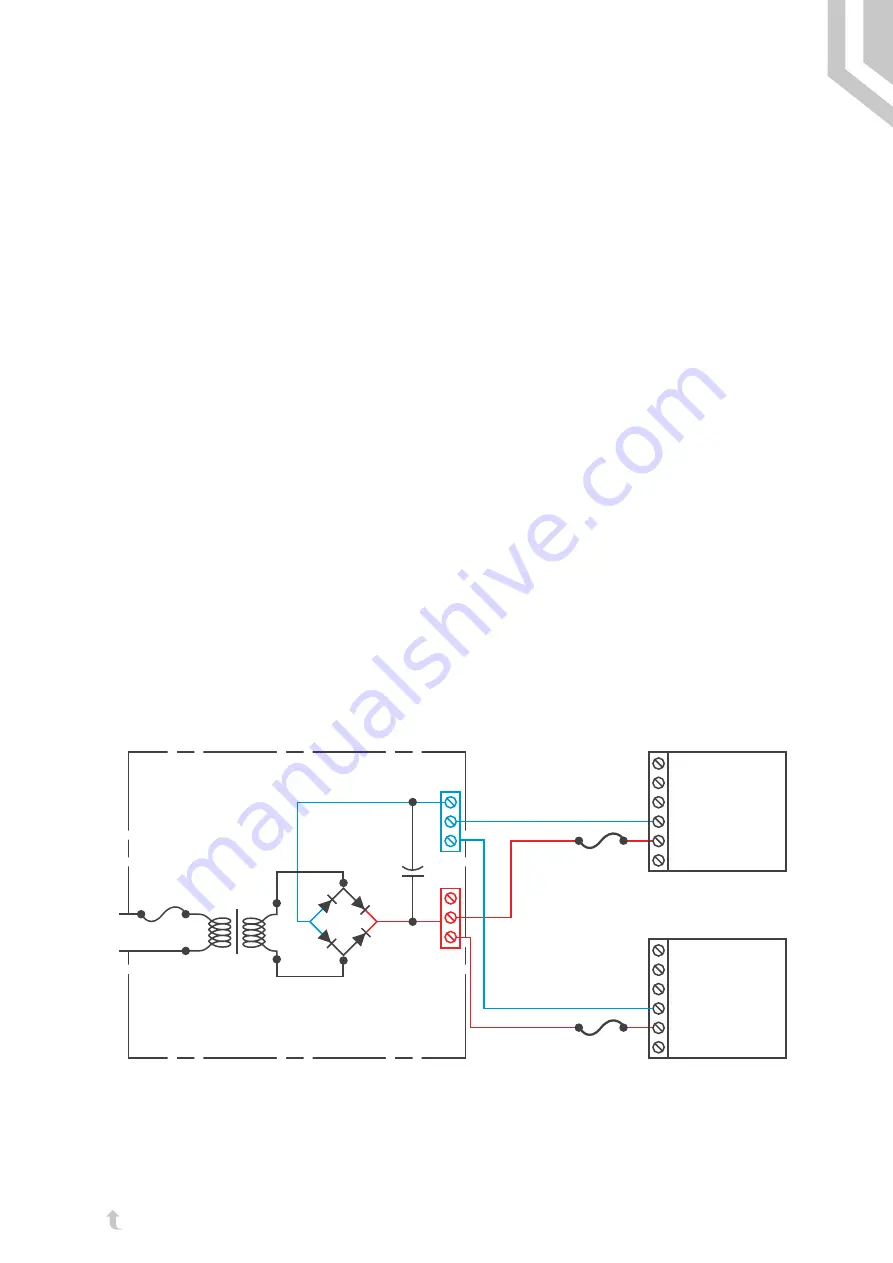
17
6.
Power Supply selection and
filtering
The drive needs 2 power supplies for operation, one to feed the digital circuit and one to
feed the motor. The digital power supply can be tipically a 12V DC voltage source with that
has smoothed and regulated output and meets the other electrical requirements.
The motor power supply should be a ‘linear’ power transformer with continuous current
capability at least of motor’s rated continuous current rating.
The DC output should be smoothed with capacitors downstream of the rectifier using the
following sizing rules;
1000uF per amp up to 80V
2000uF per amp over 80V
Connect each drive with separate feed wires from these main capacitors. Do not ‘daisy
chain’ the drives to the power supply.
Keep the wires from the power supply to the drives under 30cm (12 inches) in length. If
that is not possible, then install an additional 1000uf (or greater) capacitor directly across
the power terminals on the drive.
Figure 6. Ideal basic motor power supply configuration
Drive
Drive
Power Supply
Capacitor
Rectifier
V -
V +
Transformer
Fuse
Fuse
Fuse
+
Power -
Power -
Power +
Power +
AC
MAIN
Summary of Contents for DG4S Series
Page 1: ...DG4S series DC Servo drive...
Page 21: ...21 CONTENTS...