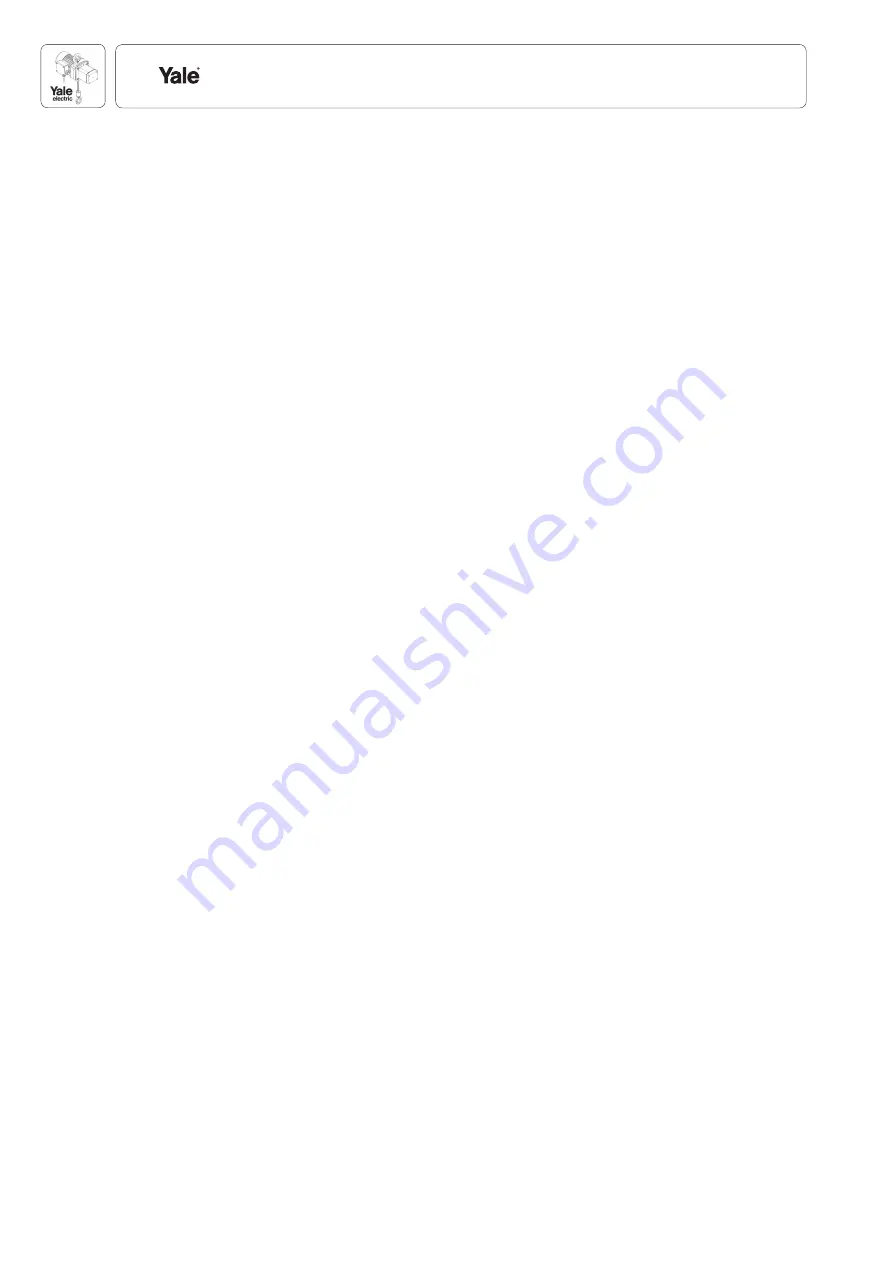
14 of 21
Pneumatic chain hoist CPA ATEX
8.6 MAINTENANCE OF THE OVERLOAD LOCK
Overload lock
The unit is equipped with an overload lock device as standard. This
device is factory set to the minimum 125% + 10% of the rated capacity
and reliably prevents overloading the hoist during load lifting. Adjustment
and testing of the overload lock may only be carried out by authorized
competent persons.
The force limiting factor, according to EN 14492-2:2006 is
φ
DAL
=1.35.
The maximum force that occurs on activation of the overload lock is
calculated depending on the total load:
F
LIM
= (
φ
DAL
x m
RC
+ m
H
- m
RC
) x g
φ
DAL
= 1.35
m
RC
= Load carrying capacity of the hoist [kg]
m
H
= Hoist load [kg]
Hoist load m
H
: Load, which includes all the masses of a load equal to
the load carrying capacity of the hoist, the hoist medium and the fi xed
load lifting attachments, e.g. hooks, grabs, magnets, lifting beams,
vacuum lifters.
g = Acceleration due to gravity (9.81) [m/s
2
]
Adjustment of the overload lock (Fig. 23)
Attention:
The settings of the overload lock should be defi ned only by
qualifi ed personnel.
Attention:
The unit is ready for operation during this activity and there
is a risk of physical injury caused by rotating parts.
• Loosen the cylinder screws (item 52) that hold the gearbox cover in
place (item 51).
• Loosen the threaded pin (item 47) which the ball (item 46) presses
on the housing to secure the straining screw.
• Check the adjustment with a suitable load (min. 125% of the rated
load capacity).
• Increase the friction torque of the overload lock by turning the straining
screw (item 42) in clockwise direction until the load is raised.
Attention:
The maximum operating time of the overload lock is 60
seconds. Then, the unit has to cool down to room temperature (min.
20 minutes).
• Screw in the threaded pin (item 47) using Loctite® 243
• Screw on the gearbox cover (item 51) using the cylinder screws
(item 52).
8.7 MAINTENANCE OF THE GEARS
The gearbox is practically maintenance-free. Service is therefore limited
to changing the oil.
8.5 MAINTENANCE OF THE TROLLEY
In particular check following parts:
• Side plate: For cracks or deformation in particular around the areas
of screwed connections.
• Plain rollers: Visual inspection for cracks. Wear and tear on wheel
fl anges. Grease the transmission.
• Beams: In particular around threaded areas for cracks and deforma-
tions.
• Fasteners: Check nuts, screws and locking devices for tightness.
Oil change
The gearbox oil should be changed every 5 years, however after 400
hours of operation at the latest (oil volume: ca. 0.3 Litre).
Attention:
The compressed air supply must be shut off during the oil
change.
To replace the gear oil, you must fi rst dismantle the gearbox cover (item
51). To do this, remove the cylinder bolts (item 52). Then remove the
screw plug (item 44). Place the hoist horizontally and turn so that the oil
can drain from the fi ll hole into a suitable container (approx. 30 minutes).
Replenish the gearbox oil. We recommend using a mineral oil with the
ISO-VG 460 viscosity class, e.g. FINA GIRAN L 460. Then assemble
the unit again in reverse order. Finally, re-adjust the overload protection
device.
Disassembly/Assembly of the gearbox (Fig. 23)
Attention:
The gearbox has oil lubrication.
Disassembling
1. Pull the coupling (item 50) off the gear shaft (item 35).
Loosen screws (item 52) and remove the gearbox cover (item 51).
2. Remove screw plug (item 44) and seal (item 45).
3. Place gearbox upside down and drain oil from the fi ll hole into a
suitable container.
4. Loosen the threaded pin (item 47), remove the ball (item 46) and
unscrew the fi xing screw (item 42).
5. Remove cup springs (item 41).
6. Loosen locking screw (item 38) and remove locking bolt (item 39).
7. Loosen locking ring (item 37), remove the bearing plate (item 33)
and ball bearing (item 36). Remove locking ring (item 34) and
press ball bearing (item 36) out of bearing plate (item 33). Remove
locking ring (item 37) from gear shaft (item 35).
8. Remove friction pads (item 28) and ring gear (item 29).
9. Remove planet gears (item 32), needle bearings (item 31), stop
washers (item 30) as well as the planet gear carrier assembly (item
27) and pinion (item 26). Remove the gear shaft (item 35).
10. Remove the threaded pin (item 17).
11. Press out remaining gears inside the housing (item 1) in the direction
of the fl ange. Light blows with a rubber hammer in axial direction
onto the rim of the housing (fl ange side) may be helpful to loosen
the bearing race (item 15).
12. Remove planet gears (item 25), needle bearings (item 24) and stop
washers (item 23) from the planet gear carrier (item 22).
13. Pull planet gear carrier (item 22) and pinion (item 21) out of planet
gear carrier (item 3).
14. Remove ball bearing (item 20) and bearing race (item 15) from the
planet gear carrier (item 3).
15. Remove locking ring (item 11) from planet gear carrier (item 3) and
press out the planet gear shaft (item 10).
16. Remove planet gears (item 7), needle bearings (item 8), stop wash-
ers (item 6) and spacer rings (item 9).
17. Remove bearing (item 5) and packing rings (item 4).
After cleaning, inspection and replacement of all worn parts, re-assembly
can be started.