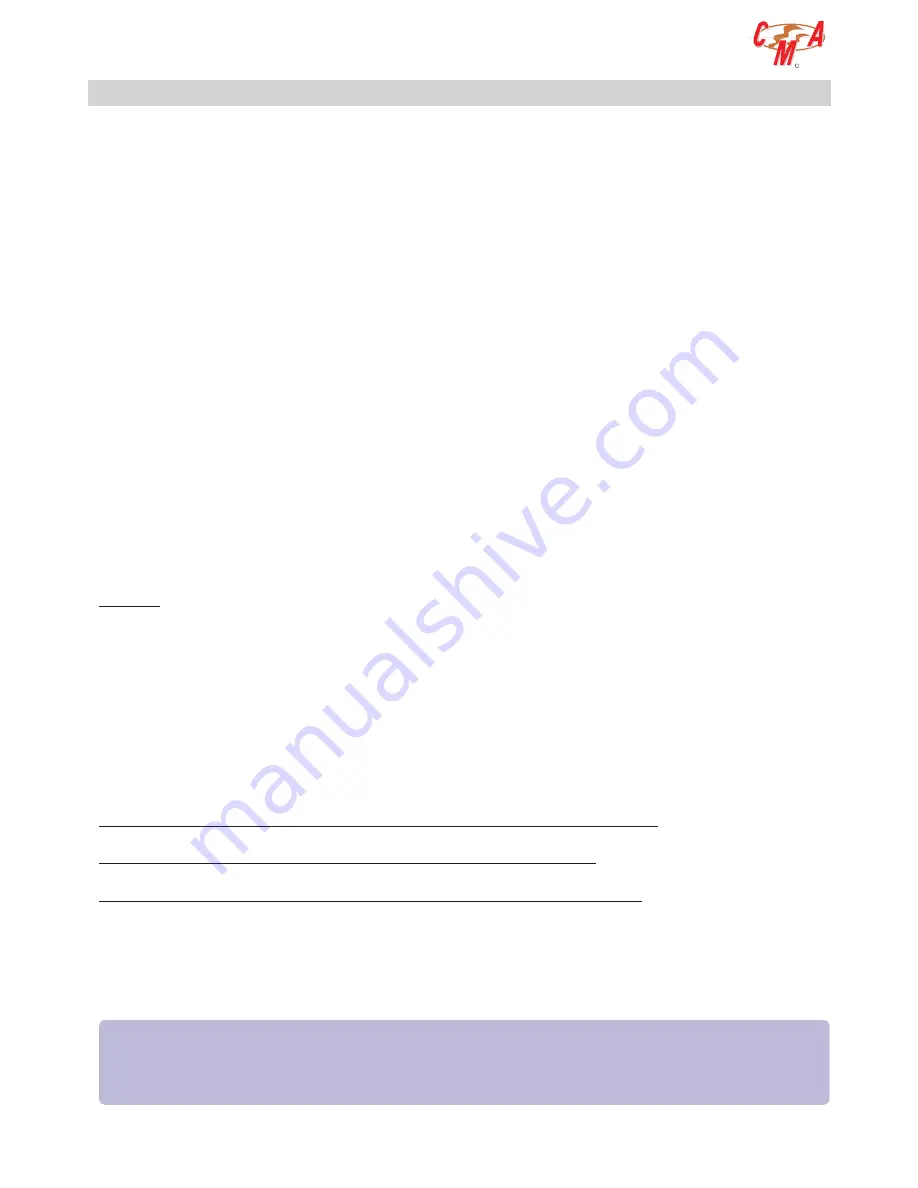
english -
41
R
espresso coffee machine - technician instructions
24. LIST OF HAZARDS
This chapter describes possible hazards for the user if the specific safety standards (described in this manual) are not adhered to.
The appliance must be connected to an efficient grounding system
If this is not done, the appliance can be a source of dangerous electrical discharges as it is no longer able to discharge electricity to earth.
Do not use running water for washing
The use of pressurized water directly on the machine can seriously damage the electrical equipment. Never use water jets to wash any part
of the appliance.
Be careful of the autosteamer, steam and hot water nozzles
During use, the autosteamer, steam, and hot water nozzles become very hot and are thus a potential source of danger. Handle these parts
carefully. Never direct steam or hot water jets directly on parts of the body.
Do not work on the machine when it is supplied with electrical power
Before carrying out any maintenance or repair work on the machine you must turn it off using the main switch or, better yet, disconnecting the
mains connection terminals. Never remove any body panel when the machine is supplied with electrical power.
Never work on the hydraulic system before having emptied it
All work regarding the hydraulic system and the related boiler is to be avoided when there is still water and pressure in the system. Thus you
must empty it beforehand by closing the mains tap and dry-running the delivery group for a short time. Switch off the machine and turn on all
the steam and water taps. When the pressure is zero, empty the boiler completely by unscrewing the special pipe fitting located on the lower
part of boiler.
If the above procedure is not carried out correctly, opening any part of the hydraulic system can cause a sudden outburst of superheated
water under pressure.
Lever machines
Never lower the lever if there is no coffee in the filter, or if the filter holder is not installed on the group: the sudden upwards movement of the
lever may damage the appliance and injure individuals.
Gas machines
Periodically check for gas leaks in the system by applying a soapy solution to the ducts.
For safety reasons, close the gas heating system when the machine is not in use (at night or during hours of closure)
Use of the appliance
This espresso coffee machine is an appliance for professional use only. Any other type of use is considered incorrect and therefore dangerous.
Never allow children or people not familiar with it to use the machine.
Non-observance of the above-described standards can cause serious harm to people, property or animals.
Never work on the electronic apparatus when the machine is still supplied with electrical energy.
Shut down the machine completely by disconnecting it from the mains before carrying out any operation.
ATTENTION
Any action taken by a technician on the electronics of the machine when the machine is still supplied with electrical power
automatically invalidates any guarantee.
The technician needs to be aware that the machine is electrically connected and act accordingly.